わが社のモノ作り戦略 第16回
秋田ファイブワン工業 代表取締役社長 佐賀 善美氏
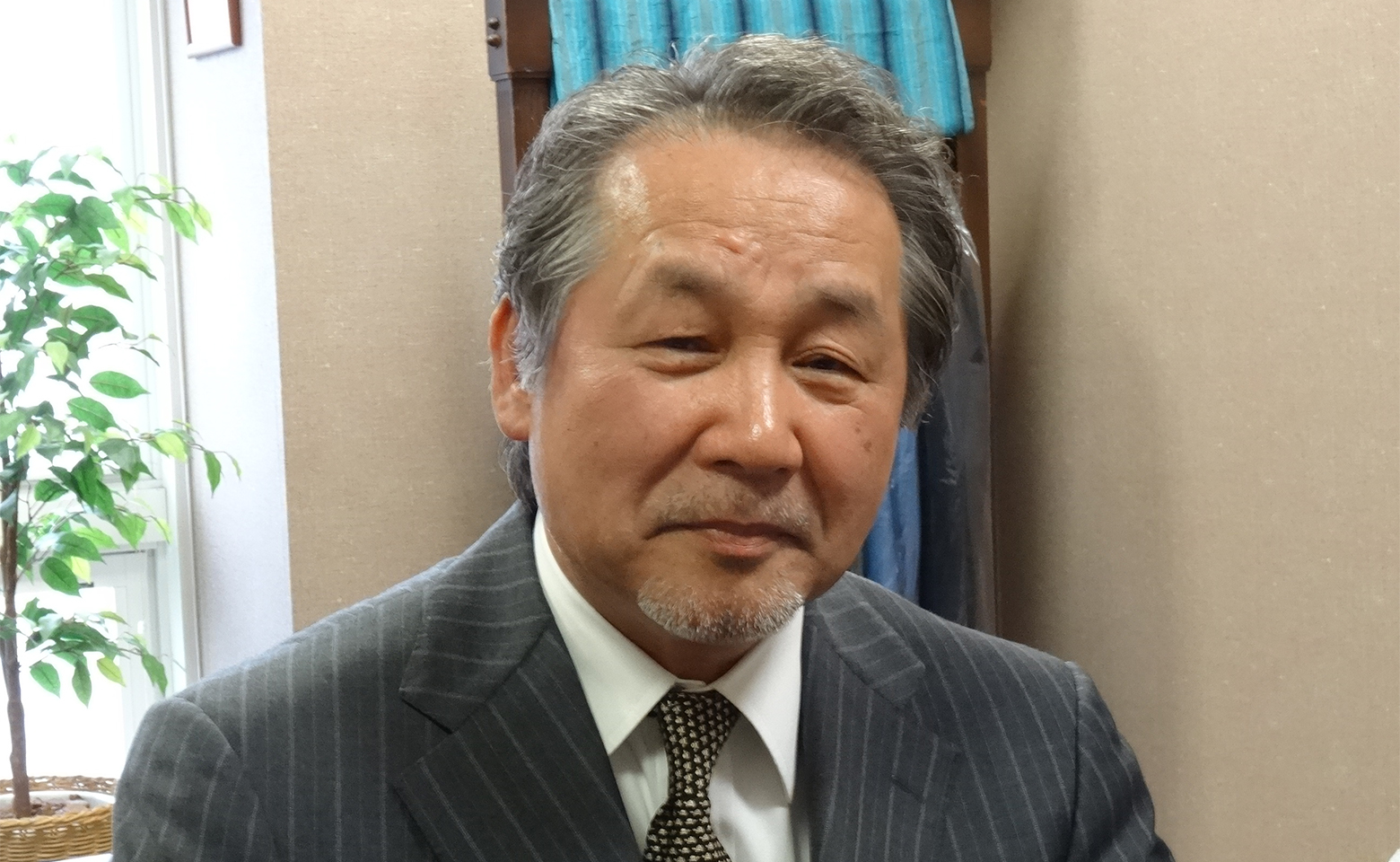
国内最大の縫製産地と言われる東北には有力工場が今でも多く残っている。秋田市にある秋田ファイブワン工業もその1社です。大阪にあるファイブワン工業(現ファイブワン・ファクトリー)の秋田工場としてスタートし、メンズの高い技術をベースにメンズ・レディスのスーツ、ジャケット、コート、カジュアルなどを生産しています。「ヒューマン・ファクトリー」を企業理念に掲げ、働きやすい自己啓発型の工場を目指して人材を育成し、次世代への継承も進めています。佐賀善美社長に現状と今後の方向をうかがいました。
「考える技術者集団」を目指す
ーまず概要をお聞かせください。
大阪のファイブワン工業の秋田工場として、昭和48(1973)年6月に秋田県の誘致工場として操業を開始し、50年2月に会社組織として今の秋田ファイブワン工業がスタートしたわけです。操業時はメンズのスーツだけでしたが、55年4月にレディスライン、58年6月からカジュアルラインを設け、生産アイテムを拡大してきました。また海外生産が本格化する中、国内で生き残っていこうと平成12年10月には現在の新社屋を建設しました。ボクは昭和24年1月生まれの地元出身で、当時は東京の会社に勤めていた。ところが父が誘致工場が出来るというニュースを知って勝手に応募し、長男なのでいずれ帰らなければという考えもあって面接を受けたら担当者からハッパを掛けられて就職することになった。現在、人員は105人で平均年齢は39.4歳。100人前後の体制というのはずっと変わっていません。今春も5人が新卒で入社してきたが、この5年間は新卒社員が1人も辞めてない。来年は6、7人を採用する計画です。取引先・ブランドはランバン、イトキン、パパス、ユナイテッドアローズ、イッセイミヤケ、ヨウジヤマモト、エイ・ネットなどで、メンズラインが年間2万7千着、レディスラインが1万4千着、カジュアルラインが1万3千5百着、それに協力工場二社でカジュアルを約3万着生産しています。メンズラインではレディスの高級ブランドも流しています。また教授が着用するような高級白衣も生産しています。
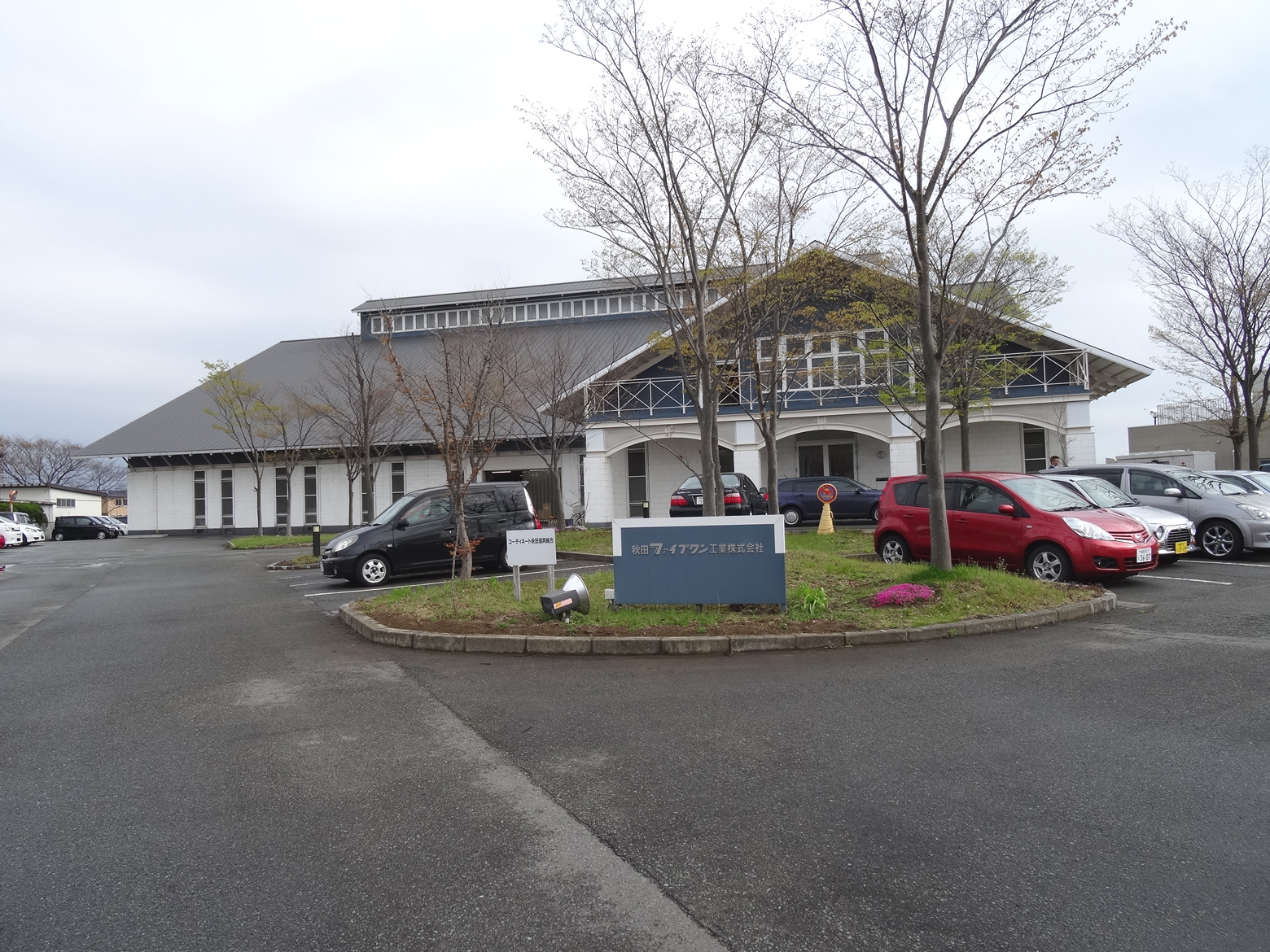
高級ブランドの生産を主力にする秋田ファイブワン工業
ー大阪の「ファイブワン」は高級メンズスーツ作りでは高い評価を受けています。そのDNAを秋田も継承して来たわけですね。
豊島均取締役技術部長も大阪と同じくらいのレベルの技術力を持っているし、大阪から技術者を招いて指導も受けてきました。だから総毛芯からカジュアルまでこなせるというのがうちの売りです。しかし量だけを追うのではなく、モノ作りに妥協せず、多くの消費者の方々に喜ばれる製品を提供し続けることを重視していますし、社員みんながいろいろなものを作って楽しめるように、社員たちがこの仕事を受けるかどうかを営業の1つの判断にしてきました。ただ、相手の経営者の方のポリシーとあったら、量が少なくても取り組んでいます。最近ではデザイナー皆川明さんの「ミナペルホネン」がそう。ブランド担当者の1人が知り合いで、声を掛けられた。当時はまだ量も少なくて現場に負担を強いることになるのでお断りしようと思ったが、皆川さんのモノ作りをすごく大切にする姿勢に共感したんです。最初は20、30着で、しかも1枚裁断のため大変でしたが、今では1ロットも100着を超え、みんなすごく楽しそうにやっている。大きなロットは確かに管理者も楽だし、オペレーターの生産性も上がる。だけどそれはゆくゆく中国や海外に行く可能性がある。そういう商品ではなく、高感度で味のあるモノ作りにこだわる。真心が入っていれば、洋服は着るものだから、作り手の気持ちが伝わるはずです。この姿勢を国内で貫こうと考えています。取引先の理想的な比率は1社10%で10社。10%の1社がなくなっても半年以内で立ち直れるが、それが15%を超えていると1年掛かります。だから毎年必ず小さくても新しいブランドに挑戦する。そうすると素材もそれぞれ違うし、別の形で技術開発につながるわけです。
ーヒューマン・ファクトリーを企業理念に掲げられていますが、その目的は何でしょうか。
縫製企業は労働集約型ですが、知識集約型産業、つまり考える集団になっていかないといけないと考えているんですね。その目指すべき姿が「ヒューマン・ファクトリー」。人間性を重視した働きやすい生産工場であり、別の言い方をすると自己啓発型の工場です。ややもすると縫製企業はワンマン社長になりがちで、うちもかつてはそんな感じだったが、ボトムアップ経営に転換しないといけないと気付いた。スポーツでもあるところまでは鍛え方で強くなるが、優勝出来ないケースがある。それは最後に選手たちのモチベーションが影響している。言われてやるんじゃなくて、自分たちからやるんだという意識変革をしていく。それがなにかを変える。同じように我々の工場も自分たちで考えて仕事をすると失敗が少なくなる。例えば技術担当が作成したパターンをサンプル班が受け取り1着先上げし、それに基づいて現場のリーダーが作業配分している。でも、それぞれがパーフェクトじゃないはず。何割かは問題が見落とされ、それが直しになってしまうことがある。だから前工程の仕事を待つ姿勢ではなく、これで良いのだろうかとか、こう変えたらどうだろう、と考える。それを繰り返していくと、今より120%アップの力を発揮できる能力が眠っていると言っているんです。
高感度で味のあるモノ作り
ーそのために人材育成に力を入れられているわけですね。
人材育成としては「5S活動」と「プロジェクト5」が柱です。5S活動はもう10年間くらい続けてきたもので定着してきました。プロジェクト5は2年前から外部コンサルタントと契約して毎月1回来てもらっていますが、1番のポイントは中間管理者の活性化。先ほどの自己啓発型の工場を目指すのが狙いです。この取り組みで特に力を入れているのがコミュニケーション力ですね。おはようの挨拶から始まって意思疎通をスムーズに出来るようにする。コミュニケーション力を高めることによってホウレンソウ(報告・連絡・相談)が活発になり、待ちの姿勢から前へ前へとみんなが考え出す。ポイントは修理を出さない、企画ミスを起こさないこと。うちはグループ単位で小集団活動を毎月1回昼12時半から30分間くらいやっている。そこで話し合われたテーマがプロジェクト5の月1回のリーダーたちの会議に乗ってくる。そんなシステムになっている。こうした中で今、中間管理者が育って来つつあり、ボトムアップ体制が出来てきたので、経営を若手に継承していこうと考えています。従来型ではなく新しい形のチームプレーでやって行くため、この5年から10年以内に今の30代にバトンタッチしようと計画しているんです。だから幹部たちには若手に対して押さえつけは絶対にしないようにしようと話している。一方、社内では5、6月の閑散期に「着縫い勉強会」を開き、希望者が自分のジャケットを作っている。出来ない人は教えてもらいながらやっているが、毎回20人あまりが挑戦している。こういうことも含めて技術部長には徹底的に若手に技術の伝承をやってもらっています。
"オール内製化"へ技術開発
ーこれからの課題は。
オール内製化です。手内職が現実に日本の国内に少なくなっているんです。遅くとも10年後、早ければ5年以内にはもう残っていないかもしれません。そうすると今からモノ作りを変えないといけない。それがオール内製化の技術開発です。レディスとかカジュアルだったらオール内製化は可能でしょう。しかし毛芯仕立てはしつけ取りとか手まつりが絶対に残るので、それも含めてオール内製化は難しい課題です。今はしつけを打って、縫って、まとめに出せば良いという感覚が管理者にあるが、もうそれを捨ててくださいと言っている。自分たちで全部やらないといけないとしたら、どう縫い始末をしていくか。それを今少しずつやり始めた。これも考える集団になるための1つです。オール内製化は2、3年前から考えていましたが、本格的に取り組もうと決めたのは今年から。JUKIのミシンを導入して進めているのもその一環であり、まとめの勉強会も今年から立ち上げました。勉強会は昼間の12時半から20分間と、あとは夜の週2回くらいで、10数人が参加しています。オリジナルな内製化をやっていきたいと考えています。
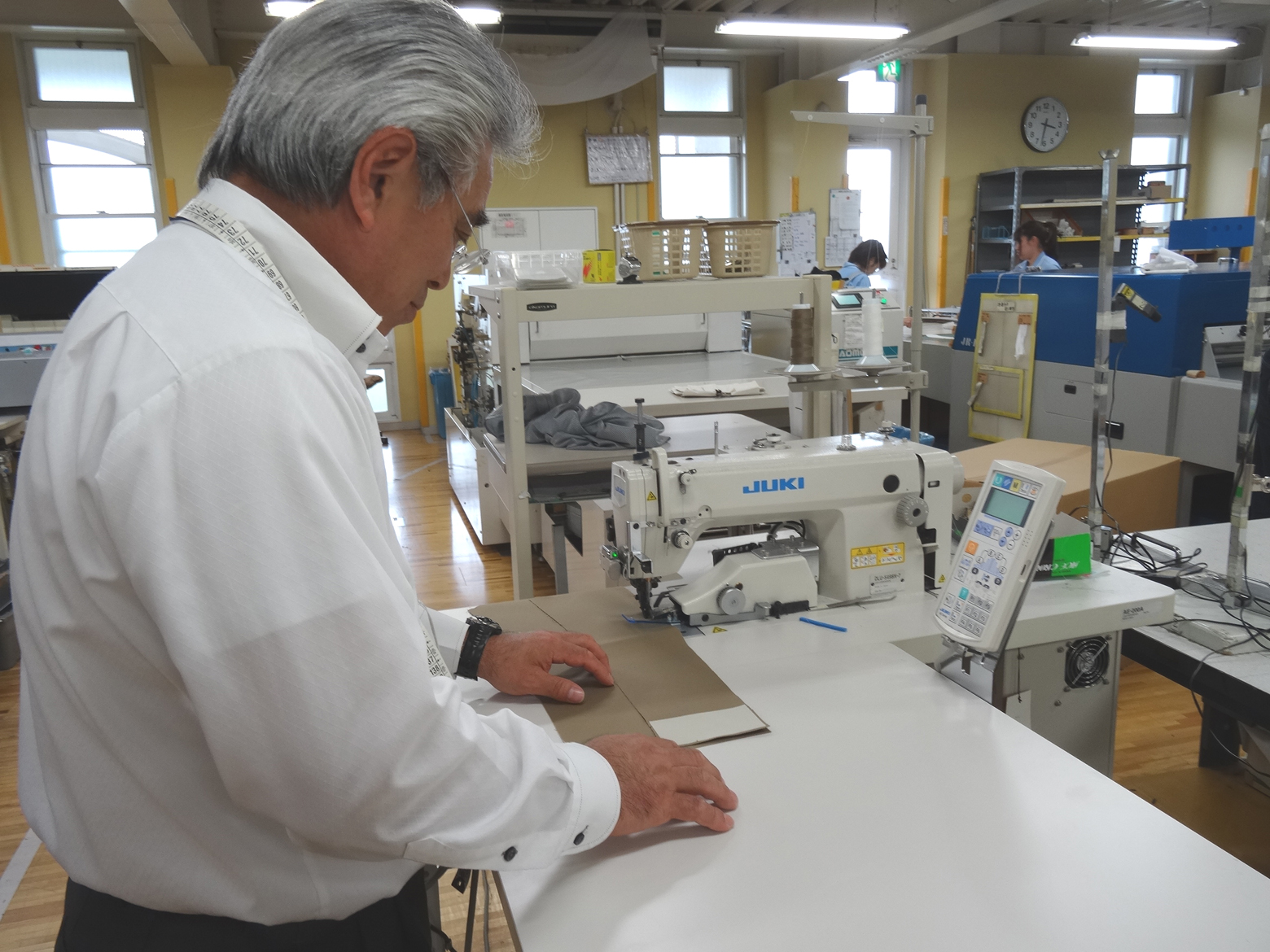
エッジコントロールシーマー「AE-200A」も内製化の目的で導入
JUKIは世界のアパレル生産を全力でサポートします
「AMS」や「エッジコン」などで"オール内製化"をサポート
秋田ファイブワン工業は小ロット多品種の高級ブランド製品を中心に生産されていますが、その縫製現場をJUKIの製品がサポートしています。佐賀社長は設備について「私から勧めることは一度もない。すべて現場の要望を取り入れている」と話します。その中でJUKIを主力にして頂いている理由としては、製品への高い評価と地域に密着した販売スタッフの対応力への信頼がうかがえました。今、同社では「オール内製化」に向けて、新たなモノ作りに取り組んでいますが、そこでもJUKIの製品が活躍しています。
その1つが縫製エリアが横150mm×縦100mmの入力機能付き電子サイクルマシン「AMS-210EN-1510」です。同機は業界トップの縫い速度(毎分2,800針)でサイクルタイムを大幅に短縮するとともに、エンコーダー制御により送りの精度も大幅に向上しました。従来機に比べ大幅に消費電力を削減し、環境にもやさしい設計です。1510タイプは市場の要望に応えて、モーター駆動式の外押さえを新設し、エア設備がなくても使用できます。同社ではホック付けやネーム付けに採用し、パターンも約20種類を社内で製作しています。AMSはさらに増設を計画されています。
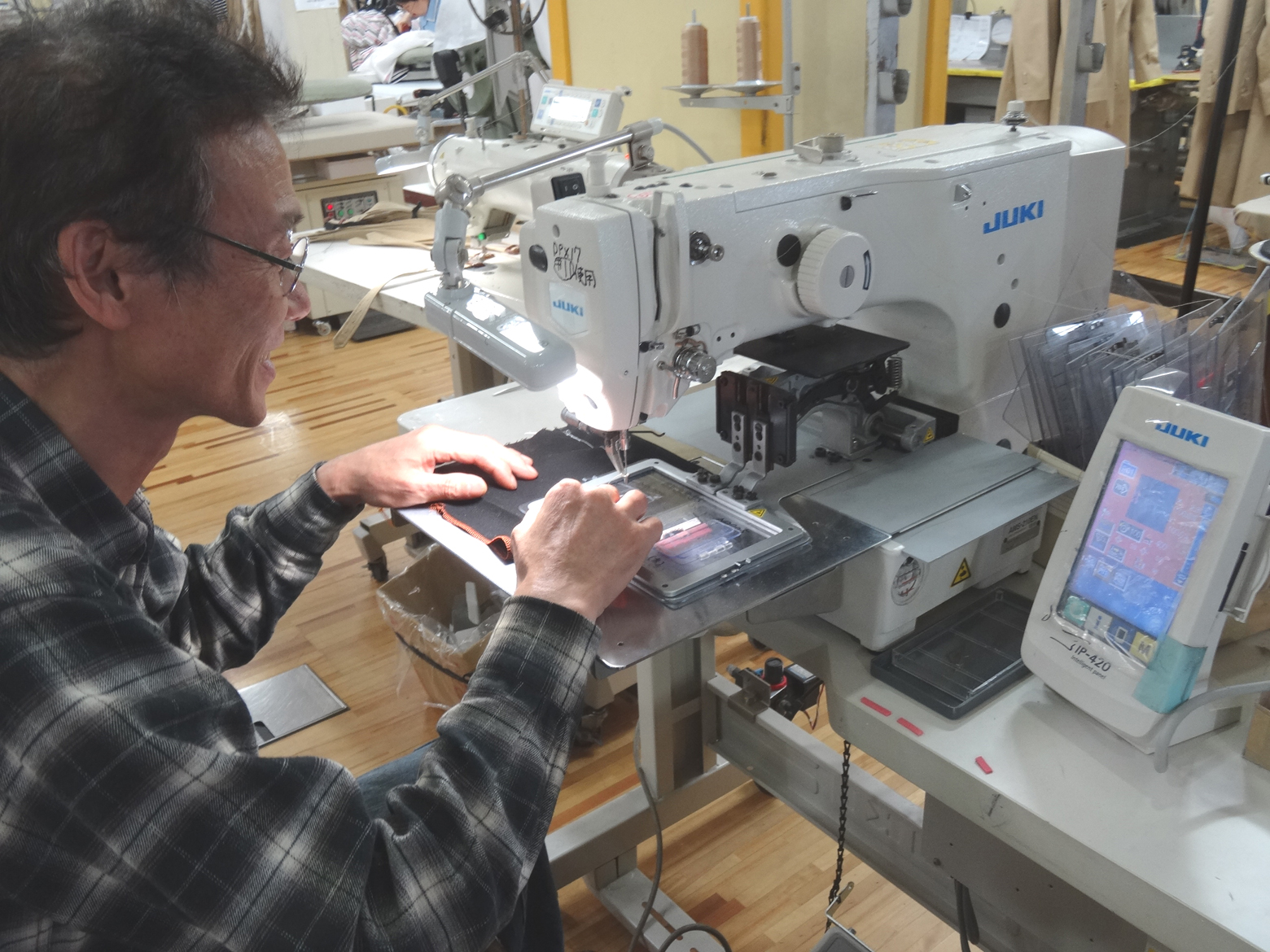
ホック付けやネーム付けに活躍する電子サイクルマシン「AMS-210EN-1510」
現場の要望で設備導入
エッジコントロールシーマー「AE-200A」も内製化の目的で導入されました。同機はJUKI独自のセンサーとマニピュレーター制御により、経験が浅いオペレーターでも熟練オペレーターの"異種曲線生地の合わせ縫い"が実現できる自動機です。多様化するデザインに合わせ、縫製仕様の変更がパネルタッチで正確かつスピーディーに行えますので、多品種・小ロットの縫製でも優美で高品質な合わせ縫いと高い生産性を発揮します。同社では裁断後の表地や裏地を処理するため、熟練者でなくても作業できるAE-200Aを設備しました。豊嶋技術部長は「パーツを早めに準備しておきたいというのが目的。品番の切り替わりの時に少しでも早く仕掛かりが出来るということがあります」と説明してくれました。
一方、今年3月にはダイレクトドライブ高速本縫い自動糸切りミシン「DDL-9000B」を新入社員の採用に合わせて3台増設されました。DDL-9000Bは最高の縫い品質と使いやすさを追求したJUKI本縫いミシンの最高峰モデルで、「新人実技訓練工程」では新入社員の女性が同機でトレーニングをしていました。
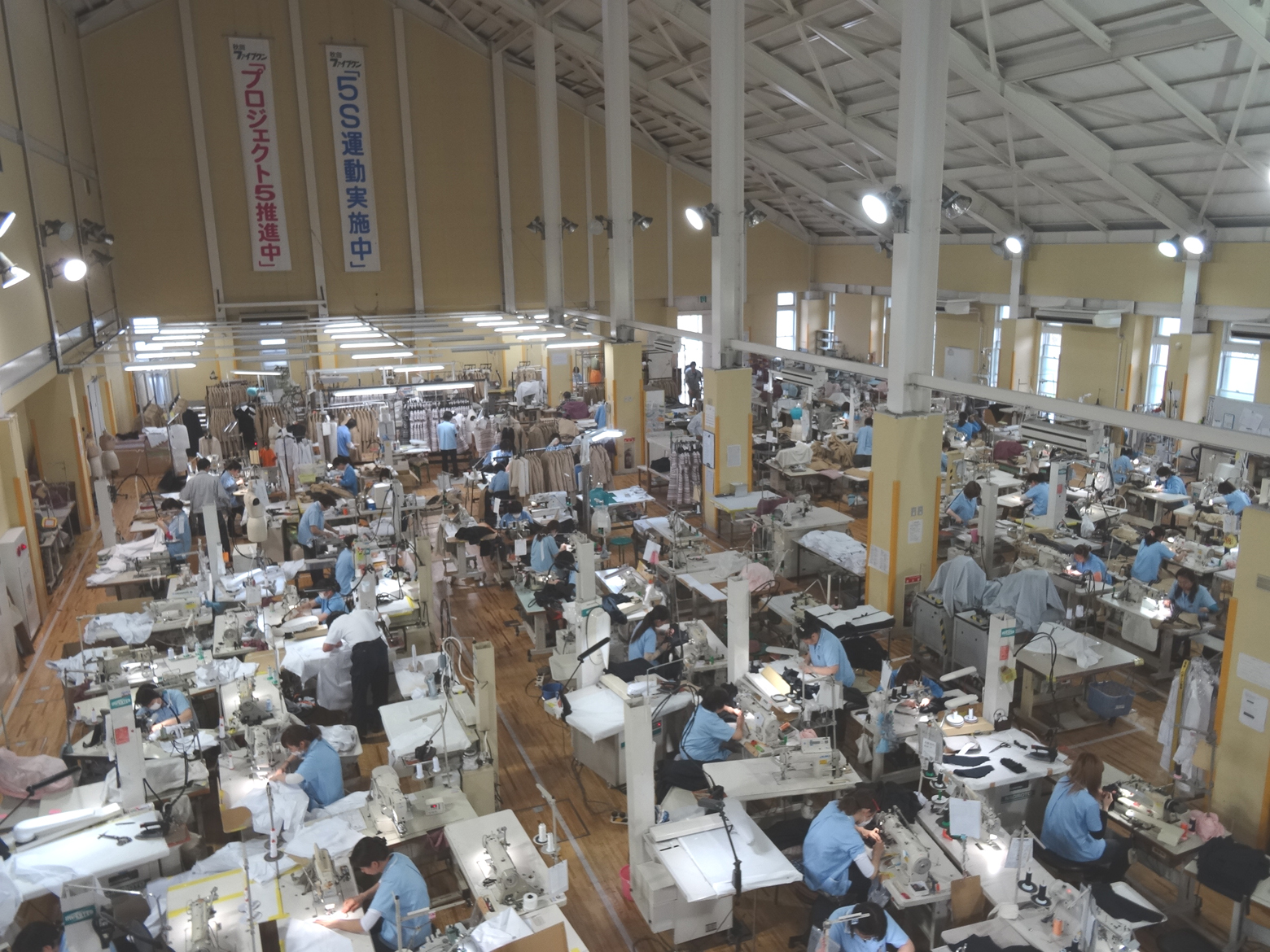
高い技術でメンズ、レディス、カジュアルを手掛ける生産現場
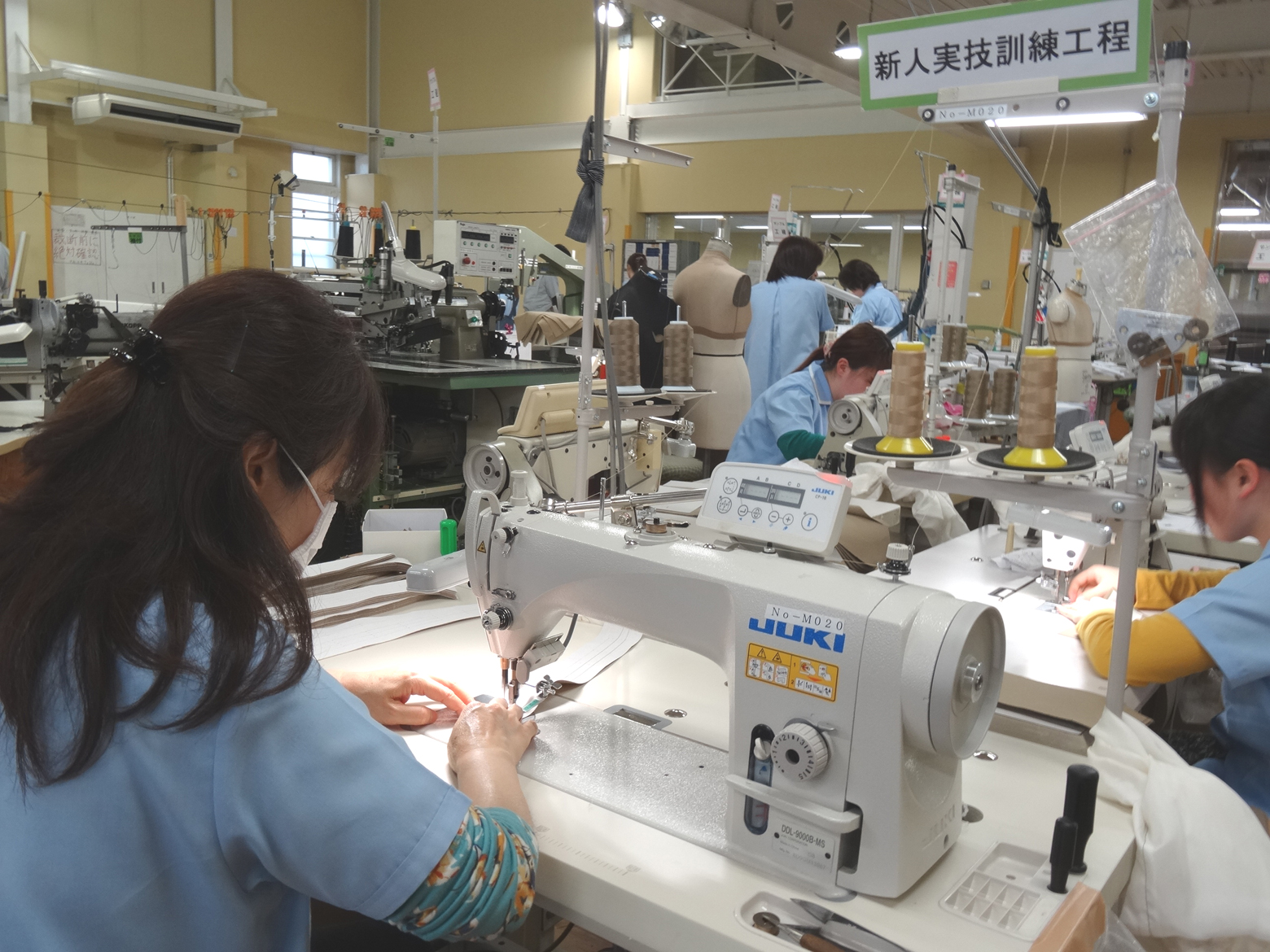
新人実技訓練工程では「DDL-9000B」を使って新入社員がトーレーニング