次世代のモノ作りに挑戦 第5回
株式会社サンシャインチトセ 会長 真武 和雄氏
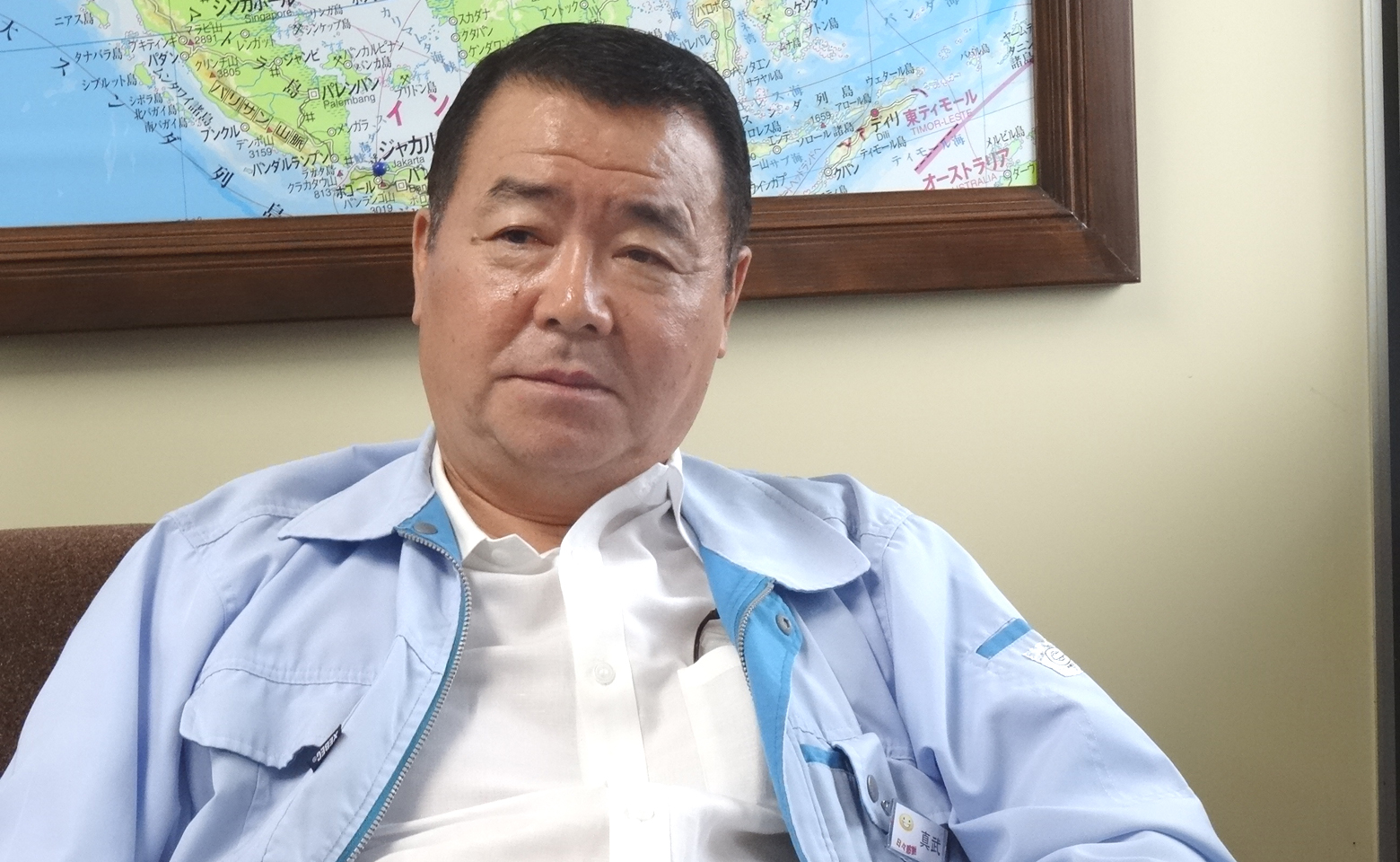
サンシャインチトセ(福岡県鞍手郡鞍手町木月3147番地の2)は航空会社、銀行、化粧品メーカー、通信会社などのレディスユニフォームを手掛けている工場です。ベトナムの提携工場を主力とした海外生産が軸ですが、国内の自社工場で多品種小ロット、別寸商品などをこなしているのが特色です。自社工場では今、技術継承のため若手の採用に力を入れるとともに、積極的に設備投資しています。その一環でJUKIのフルデジタル仕様・ダイレクトドライブ高速本縫い自動糸切りソーイングシステム「DDL-9000CFMS」を今年20台導入されました。真武和雄会長にお話をうかがいました。
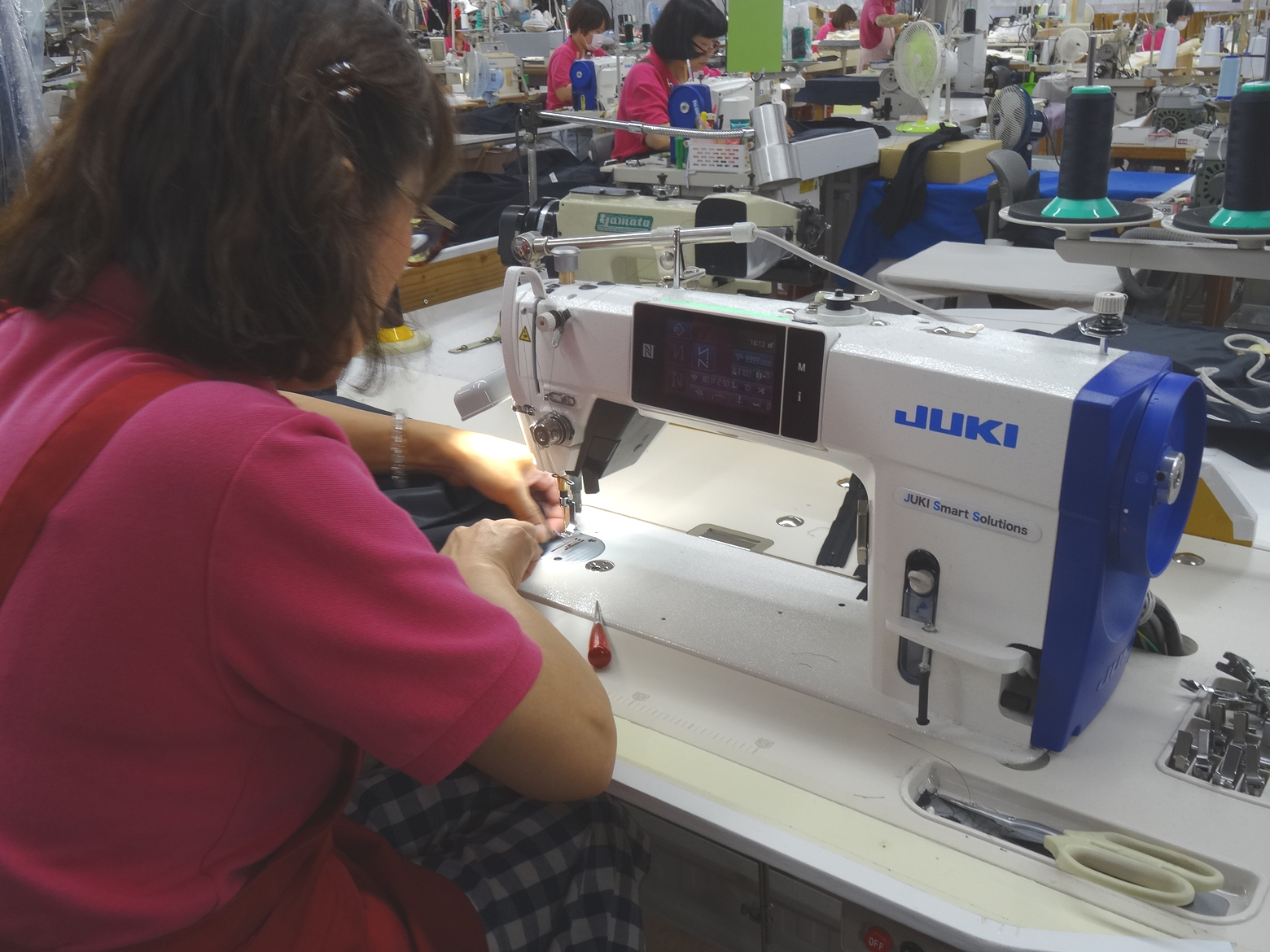
今年4月、5月に各10台ずつ導入したフルデジタルミシンが活躍
海外生産を軸に、国内で小ロット対応
ーはじめに沿革からお聞かせください。
隣の中間市に不動産開発を中心に病院や老人福祉施設などを手掛けている「ヒヤムタグループ」があり、当時のオーナーと東レのトップが懇意にしていて、1981年に東レの指定縫製工場としてレンタルユニフォームを生産するために設立したのがこの会社です。その後、一般ユニフォームの生産に取り組んできました。その中でいろいろな商社さんと取引し、これからは海外生産がメインになるので手伝って欲しいという依頼を受けたわけです。それで1995年から5年間に渡って中国、インドネシア、ベトナムにある国営、民間工場の生産指導・品質管理業務を受託、私が海外を回ってきました。ジャカルタの山の中でブラウス工場を立ち上げたこともあります。そんな経験から海外生産に対する自分なりのマニュアルが出来上がり、自分たちでも海外生産に乗り出そうとした時、北九州市と姉妹都市だった大連市の縫製関係者が当社を訪問することになり、その縁で大連の工場と取り組みを始めたのが99年でした。私が作ったマニュアルは、海外に自社の工場を建設するのではなく、自分たちが育てた現地の技術者を使って向こうの工場を管理するというやり方です。大連で17年間やりましたが、チャイナ・プラスワンの時代が来て、以前取り組んだベトナムへの進出を計画したところ、当時のメンバーがもう一度一緒に仕事をしたいと集まってくれて、12年11月からベトナム生産を開始、13年にホーチミン事務所を開設しました。
ー海外生産の現状は。
今、海外でブラウス、ベスト、スカート、パンツ、ジャケットなど約70万点生産しています。大連は昔から付き合いのある工場1社だけ。ベトナムはほぼ100%当社の仕事をしている2社を含めて6社と提携、生産規模で約1千人、ホーチミン事務所に技術スタッフが20人います。私どもは取引先のオーダーに基づいて生地や付属を手配し船に乗せて輸出、現地に着いたら事務所スタッフが張り付いて品質管理し、日本に送り出します。海外生産は日本側の思いが通じない部分があってミスが起こりがちです。そのために全品番必ず生地や付属などを貼り付けた「スワッチ」を作成する。ジャケットなどは芯地やテープの種類が多いので、使用箇所も写真入りで載せている。各工場に張り付いている現地スタッフがこのスワッチを持って現場を走り回っている。それでも向こうは許容範囲が分からないので、問題があるとすぐアイフォンで写真を送ってもらって指示します。私と阿部(康信)社長がそれぞれ年間約80日、若手社員1人が約50日現地に行く。国内工場は中西(隆幸)常務が守ってくれている。我々はモノ作りに徹し、自分のリスクで技術者も派遣しているので提携工場も安心できて成長します。ベトナムの主力2社は3倍、4倍の規模になって喜んで頂いています。
ー海外生産が軸ですが、国内生産も維持していますね。
全体では60人ですが、そのうち10人が海外事業部、50人が国内の生産部人員で、国内で年間5万枚生産しています。受注のためには特色が必要で、自社工場で小ロット生産や別寸対応などを行っている。ユニフォームは同じものを何年も着用され、突然数枚必要とされます。それに対応しないといけない。国内でこのフォローをするので取引先からも安心して頂けます。だから自社工場はオールアイテムを生産していますし、年間の70%が20枚以下の受注。2枚や5枚のオーダーで、多い時には1ラインで1日10品番くらい入ります。
ーどのような仕組みで多品種小ロットをこなしているのでしょうか。
これを語れば10年になりますよ(笑い)。それは苦労しました。最初は大きなロットの間に小ロットをやっていましたが、10年ほど前から年間ずっと小ロットになってしまい、それを平均的に生産できるようになったのは5年くらい経ってから。縫製は2ラインあり、A班は11人でブラウス、スカート、パンツ、B班が16人でジャケット、ベスト、ワンピースを流していますが、要は裁断次第。例えばジャケットは表生地、裏地、芯地の裁断があり、表生地は粗裁ちして芯地を張ってもう一度正確裁断する。柄合わせになったらもっと増える。色違いを含めるともうとんでもない時間が掛かる。だからCADもCAMも増設して2台ずつ導入していますし、出来るだけ前もって材料を送ってもらっています。裁断するとバンドルで縫製ラインに流しますが、ブラウス1枚は縛れないのでクリアファイルに挟んでいる。目まぐるしく品番が変わるから、ミシンのレイアウトも出来ない。だから必要なミシンを並べて、人が商品を持って回っている。工場が広いからそれが可能でしたし、人員の割にミシンも多いんです。
調整がとても楽に
20台のフルデジタルミシンが稼働
ー頻繁に品番が変わればミシン調整も大変ですが、導入されているデジタルミシンは調整の手間が楽になります。
デジタルミシンは今年4月、5月に各10台ずつ導入しました。送り歯高さの調整や糸調子などが非常にやりやすいですね。それと、これまではひざ上げレバーで押さえを上下していたが、女性の中にはその動作で股関節が悪くなる方もいた。新しいミシンはひざ上げレバーがなくなり評判が良い。高齢化しているのでデジタルミシンを理解してもらえるかどうか心配だったが、まったく問題なかった。もう10台は導入する予定です。これからはある程度デジタル化、機械化してモノ作りをしていく必要があります。縫いは出来ても、微妙な糸調子などの技術継承が難しくなってくる。それらはやはり機械でカバーしていくしかないと思いますね。
ー今後の方針としては。
私は社長を10年間務め、16年4月から会長に就きました。その10年間で借金もなくし、引き継ぎに当たって「会社再建から希望へのシナリオ」という今後の会社の方針をまとめましたが、その中の重要な柱として若返りを打ち出しました。会社の平均年齢がその時点で53.7歳に達し、このままでは技術継承が出来ない、2020年に42歳まで持っていこうと。お陰様で地元の高校新卒者を15年に3人、今春4人採用し、来年は6人入る予定です。すでに平均年齢が5歳下がり、22歳までの社員が全体の10人を占めています。海外生産が軸ですが、日本のこの工場は不可欠で、核になる存在です。技術革新もここから発信していく。今の時代は海外生産が主力ですが、将来日本に帰ってくるかも知れない。このビジネスモデルがずっと続いていくわけではない、それを見据えてやっていかないといけないと、社内でもよく話しています。ですから、"希望へのシナリオ"として人に投資するし、機械へも投資しようとデジタルミシンも導入しているわけです。
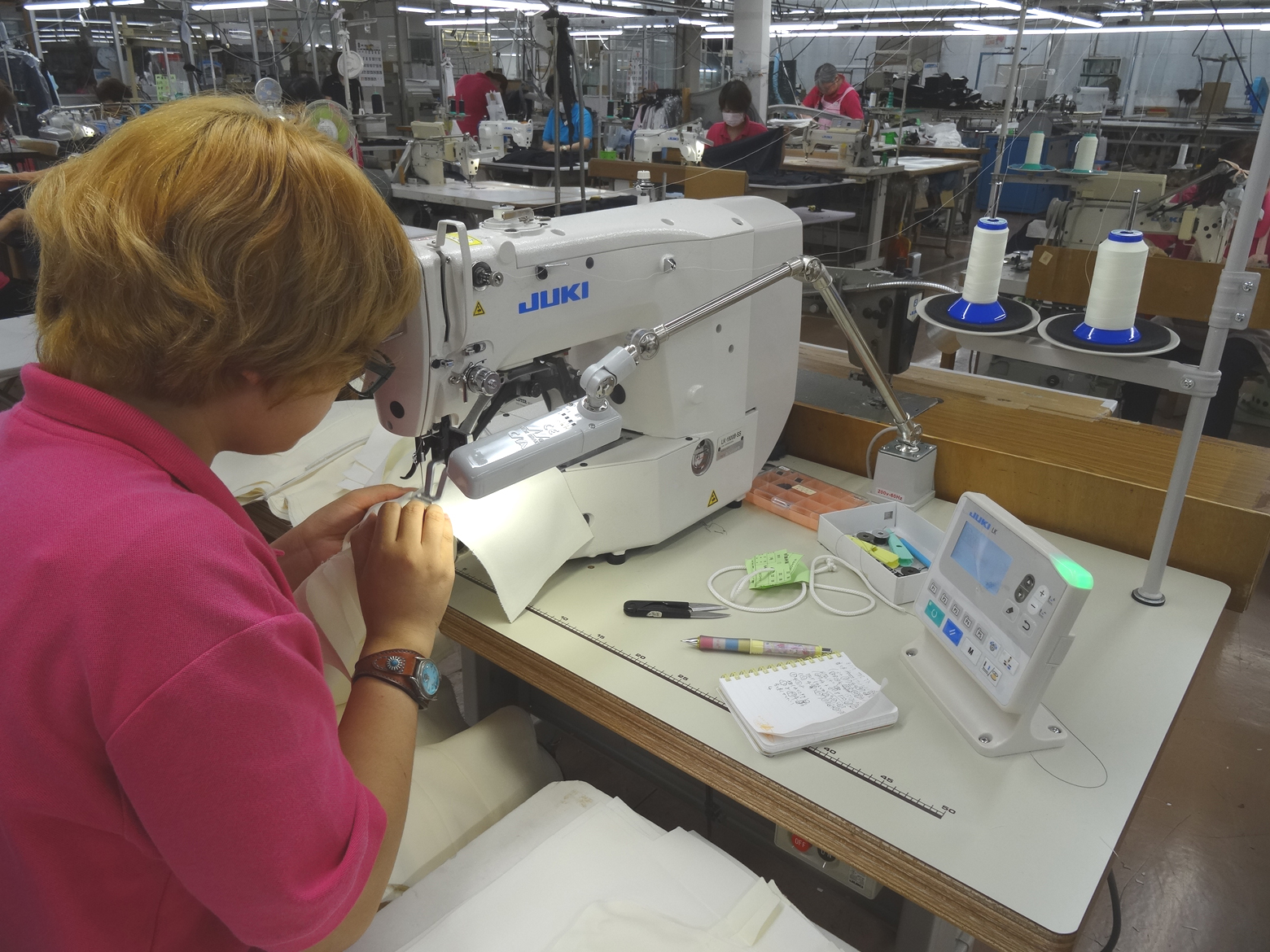
導入したばかりの高速電子閂止めミシン「LK-1900B-SS」