次世代のモノ作りに挑戦 第13回
株式会社玉名サンモード 代表取締役 林田 享氏
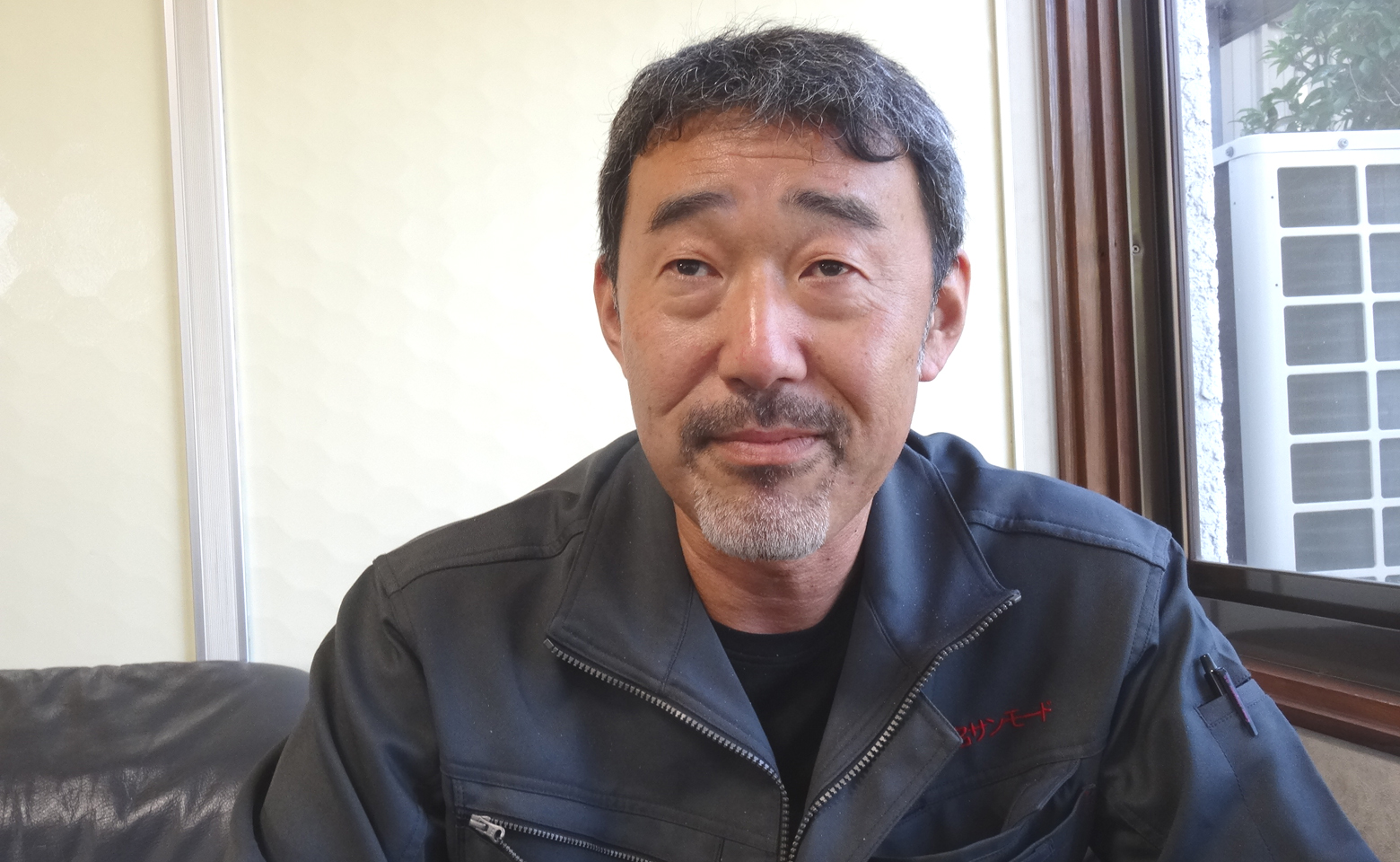
品質とスピードが強みの婦人服工場大
大河ドラマ「いだてん」の主人公である金栗四三のふるさととして話題になっている熊本県玉名市。ここにある玉名サンモード(玉名市伊倉北方2720、電話0968-74-1040)はジャケット、コートなど婦人重衣料をメインに生産しています。縫製現場は50人余りの1ラインで、この縫製力を生かして「品質と納期対応のスピード」を実現、取引先から高い信頼を得ています。JUKIの"デジタルミシン"ダイレクトドライブ高速本縫い自動糸切りソーイングシステム「DDL-9000C」シリーズも発売間もなくから導入を始め、現在は21台が稼働中。縫い始めの上糸残りを減少するなど効率化につなげ、同社のモノ作りをサポートしています。
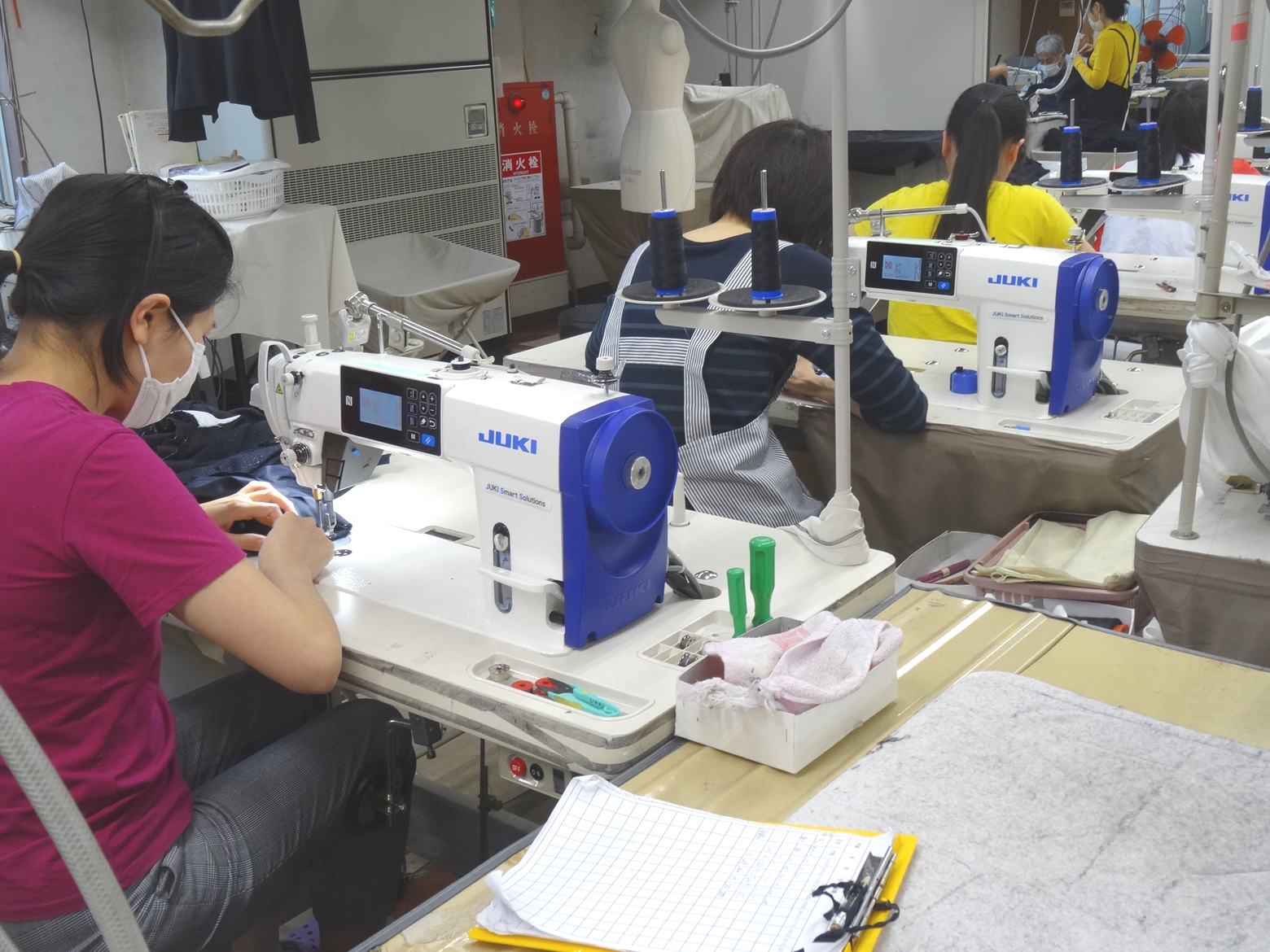
ジャケット、コートなど婦人重衣料をメインに生産する玉名サンモード
50人で1ラインの縫製力を生かして
―沿革からお聞かせください。
1976(昭和51)年9月にサンモードの玉名工場として設立したのがスタートです。サンモードは祖父が創業し、一時期は福岡に2工場と、熊本、大分の計4工場ありました。今は我々と久留米の2社で、それぞれ経営は別です。玉名サンモードとして独立したのは82(昭和57)年2月。11年前に現在顧問の父(林田幸雄氏)から経営を受け継ぎ、私が営業を担当、現場を弟(林田直樹代表取締役専務)が見るという体制でやってきました。この玉名・荒尾地区には33社が加入していた工場の集まりがありましたが、現在は6社が残っているだけです。
―現状は。
玉名サンモードグループは全体で73、4人。日本人は募集してもまったく反応がなく、以前は中国から受け入れていましたが、4年前からはベトナム人の実習生を受け入れています。実習生の中には4年生が4人おり、12月にはもう2人戻ってきます。取引先はワールドさんがメインで、またロットはそれほど大きくありませんが、いろいろな縁があってデザイナー系や個性派ブランドの商品にも取り組んでいます。日産は220~230着です。ワールドさんは「リフレクト」や「アンタイトル」などのブランドが中心で、今でもジャケットで7、8千着、コートで1千着、1千500着のロットが入ります。中でもリフレクトの「匠ジャケット」は今秋冬向けで19代目になりますが、初代から手掛けてきました。大きなロットがあって受注に恵まれていることはありますが、その代わり要求されるのは納期で、どんなことがあっても店頭の販売に間に合わせるようにしています。匠ジャケットは「J∞QUALITY」認証商品で、当社も「J∞QUALITY」企業認証を取得しています。
―玉名サンモードのウリは何でしょうか。
やはり品質とスピードです。最近は匠ジャケットでもジャージー素材が増え、ほとんど最初にスポンジングを掛け、CAMで粗裁ち、芯張りしてから全パーツをもう一度精密裁断します。手間が掛かりますが、素材対応は品質の要です。ほかでも手がいい工場はあるでしょうが、店頭や消費者の方々に満足して頂けるレベルに達していると考えています。また縫製現場は全体で約50人の1ラインで流しています。一般の工場は小ロットに対応するため、少人数のラインに分けています。しかし、1ラインにしていることによって1人の工程数が少なくなり、日本人も実習生も技術的に成長が早いのがメリットです。それと1ラインの強みとして、例えば来週1千着欲しいと言われても間に合わせられます。そういう対応力は西日本ではトップクラスと思っています。
―デザイナーブランドや小ロットの仕事はどういう対応をしているのですか。
お付き合いしているデザイナーブランドは本当にこれが服なのか、どこから縫っていけばいいのかと考えてしまうような仕事があります。面白いと言えばそうでしょうが、それでもちゃんと服になっているんです。こうした仕事や20~30着の小ロットはちょっと全体で流すのはムリだと判断したときは、2、3人とか5人の手のいい人たちで別ラインを設けます。ただ、その人数があまり増えると本流の方が歯抜け状態になるので、年間であまりありませんが、本流は休んで別ラインだけで仕事をするケースがあります。そういうフットワークの軽さというか、割り切って対応しています。とは言え、このところ小ロットの仕事がだんだん増えていますし、これまでのように大きなロットだけを受けるわけにはいかなくなってきています。ちょうど実習生も4年生や5年生が増えてくるので、今まで断らざるを得なかったような小ロットのジャケットでも常に対応できるラインを設けていくことにしています。
―そのほかの特色としては。
地元のミシン販売店さんから本当にバックアップしてもらっています。熊本市にあるにっこりミシンさんですが、こんな素材だったらどうしたらいいとか、どのミシンを使ったらいい、どの針がいいとか、あるいはアタッチメントや自動化の相談でもすぐ対応してくれます。たぶんほかの工場とミシン販売店の関係よりも強いつながりで、もう身内みたいなお付き合いをさせてもらっていますね。社内全体も頼りにしている感じで、実習生も直接相談するような関係なんです。
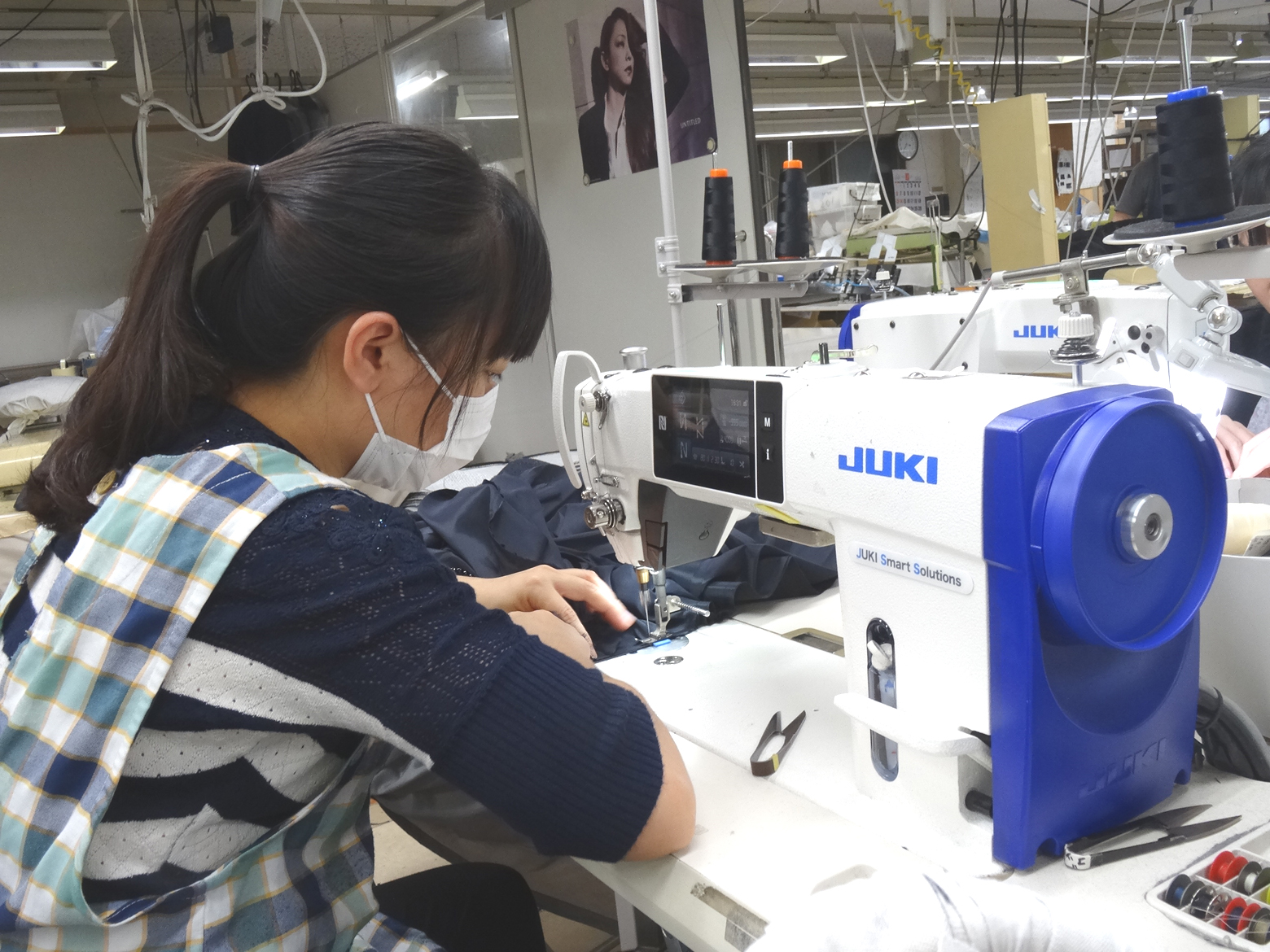
フルデジタル仕様の「9000CFMS」も1台導入
デジタルミシン21台導入し縫い始めの糸切り作業解消
―JUKIのデジタルミシンも21台が稼働しています。
発売後すぐに入れ始め、今、9000Cシリーズのデジタル仕様を20台、フルデジタル仕様を1台導入しています。デジタルミシンを採用する前は、裏なしジャケットの時に糸切り作業に多くの人数を掛けていました。縫い始めの上糸が場合によっては2、3cmも残り、納期ぎりぎりのケースでは10人余りが2間ほど掛けて処理していたんです。それが9000Cを活用することによって糸切り処理が不要になり効率化を図ることができました。それと当社は油汚れを防ぐため、以前から完全ドライのミシンを使っています。油が裏地に付けばもう取り替えしかありませんからね。9000Cでもデジタル仕様には完全ドライがないため、にっこりミシンさんと相談して油を止め、無給油釜に交換して完全ドライに改造してもらったミシンを裏地工程や、表地と裏地の組み合わせ工程以降に配置しています。またダーツの処理でインチング縫いするときにも便利な機能を備えているので活用しています。そんなことで徐々に台数を増やしてきたわけです。
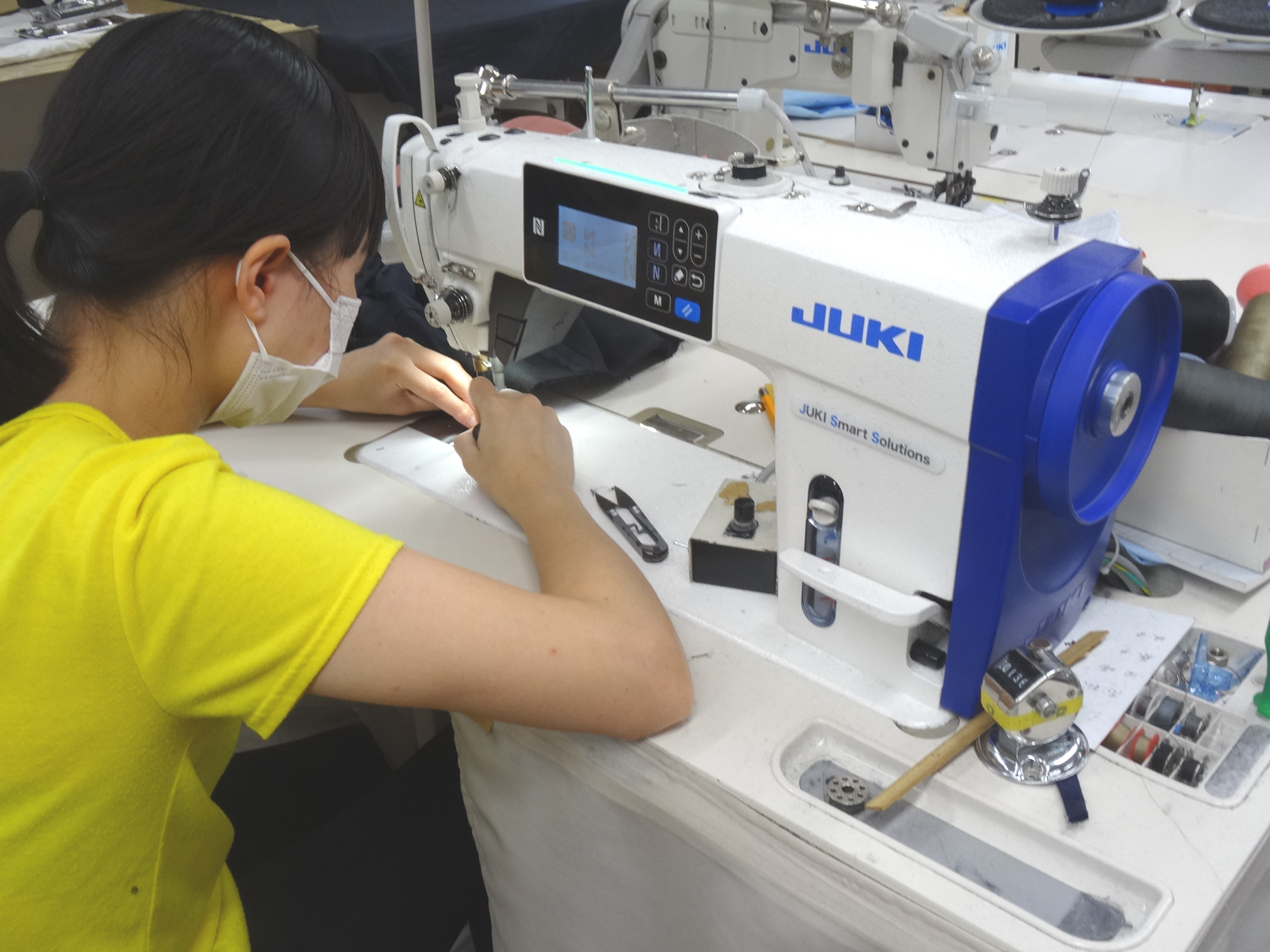
油汚れ対策のため完全ドライに改造した「9000C」シリーズを使用
この導入事例に出てきた製品・サービス
DDL-9000CFシリーズ [プレミアムデジタル]
ダイレクトドライブ高速本縫自動糸切りソーイングシステム
<p>「縫い」の創造。<br />
「縫い」へのこだわりは、次世代ソーイングシステムで変わります。<br />
これまで勘や経験に頼ってきたミシンの調整をデジタル化。<br />
素材に最適な縫いをいつでも再現できるのが、デジタルソーイングシステム、DDL-9000Cです。</p>
詳細を見る
DDL-9000CSシリーズ [デジタル]
ダイレクトドライブ高速本縫自動糸切りソーイングシステム
<p>「縫い」の創造。<br />
「縫い」へのこだわりは、次世代ソーイングシステムで変わります。<br />
これまで勘や経験に頼ってきたミシンの調整をデジタル化。<br />
素材に最適な縫いをいつでも再現できるのが、デジタルソーイングシステム、DDL-9000Cです。</p>
詳細を見る