次世代のモノ作りに挑戦 第7回
秋田丸善繊維株式会社 代表取締役社長 竹村 周夫氏
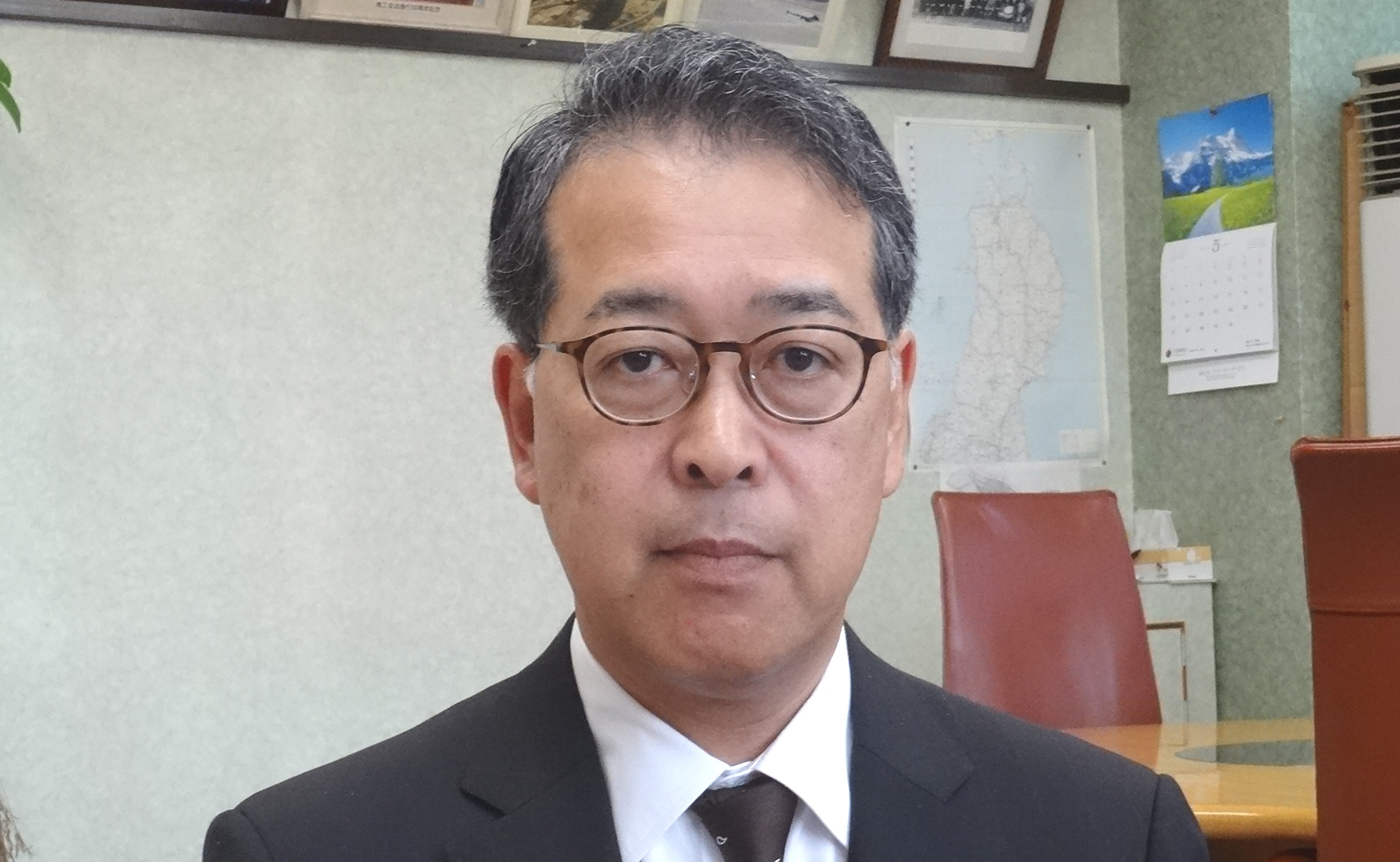
ザギトワ選手効果で脚光を浴びている"秋田犬"のふるさとと言われる秋田県大館市にある秋田丸善繊維(竹村周夫社長)。「旬のものづくり」を掲げる大手婦人服工場で、「サンプル対応の充実」「多品種少量短サイクル生産」「多彩な特殊ミシン」「自社海外工場(大連丸善時装有限公司)の活用」によって、お客さまが欲しい時に欲しい製品を売り場に供給することを目指しています。そのため自社開発の1着流しをはじめ、システムやアタッチメントなどの開発・改善にも積極的に取り組み、今年2月からJUKIのフルデジタル仕様・ダイレクトドライブ高速本縫い自動糸切りソーイングシステム「DDL-9000C-FMS」10台も稼働しています。竹村社長に現状と今後の方向をお聞きしました。
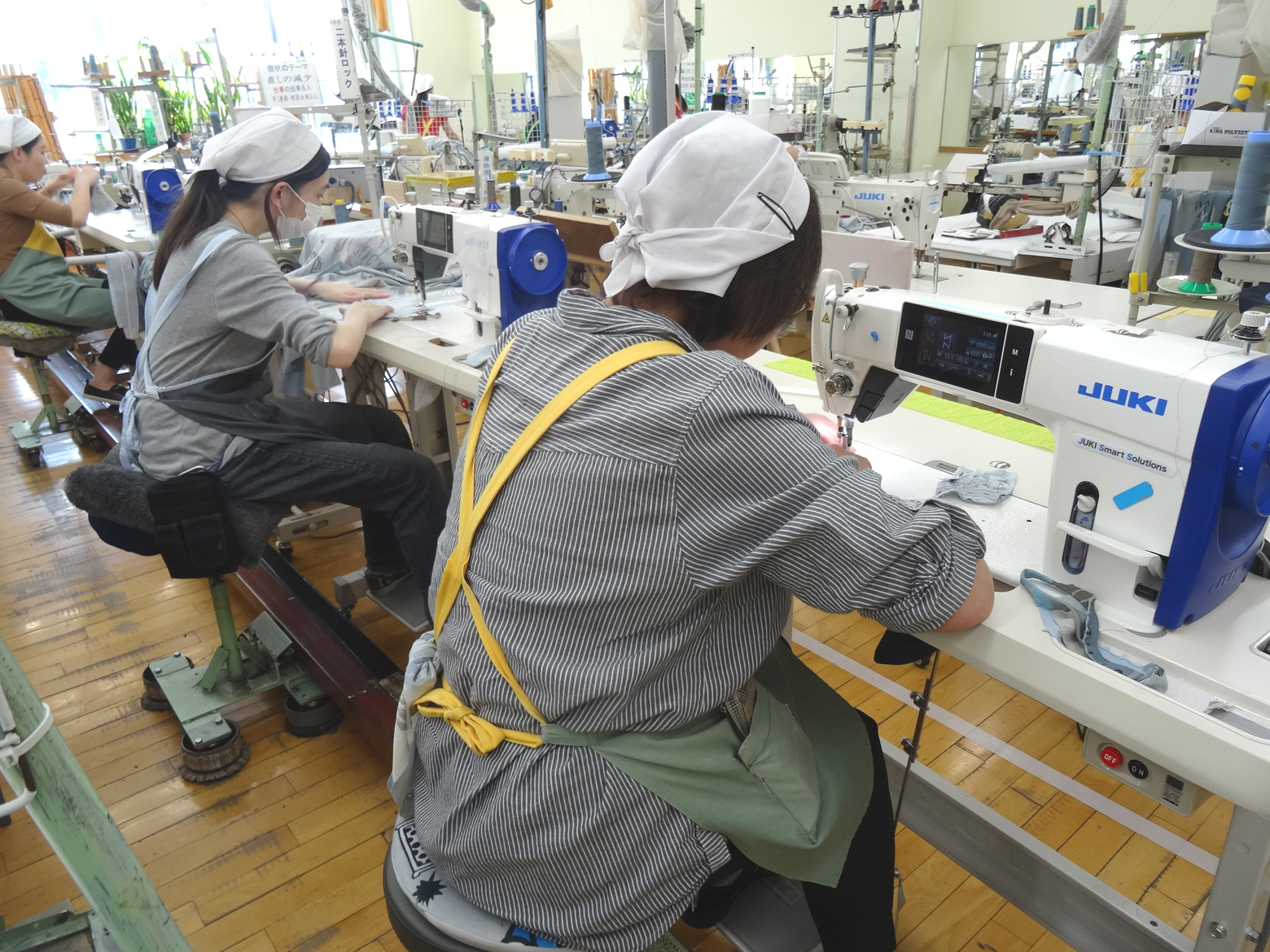
今年2月から10台の「DDL-9000C-FMS」が稼働
デジタルミシン使い「旬のものづくり」
ー現状はいかがですか。
本社が87人で、県内に15人と10人の子会社2工場があります。オペレーターはもともと厳しいんですが、以前は事務や生産管理、検査などは募集するとすぐ応募があったが、もうそちらも全然反応がない。全国的でしょうが、秋田でも縫製に限らず弱電、建築などどこも人が足りない状況です。ですから実習生を受け入れています。本社は帰国して大連工場に入って欲しいので大連で集めた中国人が主体ですが、グループ全体では中国、ベトナムから29人入れています。生産アイテムはドレス、ワンピース、ジャケット、コート、ブラウス、スカートなどと幅広く、だいたい月産7千着。今秋冬物ではオーダーが増える計画の取引先があり、受注状況は昨年に比べると少しましな感じです。
ー中国の大連市にある自社工場にも日本のモノ作りを定着させてこられました。
2006年からスタートした大連工場は、市内のほか郊外に分工場を設け、2カ所で約80人ですが、中国も縫製工が減少し平均年齢は37、8歳です。秋田に実習生として来日、帰国したメンバーが工場長や幹部、社員になり、日本と同等な品質レベルを目指してきました。その意味では外国人実習生受け入れ制度をちゃんと活用していますね(笑い)。リバー仕立て、手刺繍、ビーズ刺繍など大連でしかできないものがあり、中国の人件費が上がったとはいえ、手の込んだものはまだまだ向こうでやれます。秋田と中国はリードタイム、コスト、工数のバランスですみ分けする体制ができたと思います。中国でもこれから小ロットや難素材に対応する必要があると考え、昨年暮れにCAMを取り入れ、秋田で開発した柄合わせ延反・裁断システムを導入しました。大連は現在技術顧問の嶋田(興次郎)が専務時代に手掛けた工場で、今でも技術指導や進捗状況を担当しています。
ー「旬のものづくり」を企業スローガンとして打ち出しています。
適時適品適量というトヨタの考えがありますが、我々も同様に春夏は薄物、秋冬は厚物と幅を広げようという発想です。かつてワンアイテムの時期があり、閑散期をなくそうという狙いでフルアイテム生産の体制を作り上げてきました。ミシンも薄物、厚物の2種類を揃え、よくミシンが余っていると言われます。それでも閑散期が起きるので頭が痛いんです(笑い)。悩みはいろいろありますが、基本的にはいいものをしっかり作ろうと。あくまでも高付加価値の製品を工業的に生産するという軸は変えないようにしていきたいと思っています。東南アジアに進出した工場の方々も適地生産を進めていますが、あまり量を追い求めなければ、海外生産と国内の多品種小ロット短納期は物理的にすみ分けできると考えています。
ーそのためにいろいろな仕組みを作ってこられました。
企画・技術スタッフに6人、サンプル作成に2~4人配置し、ブランドごとにパターンチェック、工業用パターンとサンプルを作成。このスタッフが担当ブランドの製品を量産ラインに投入する時はオペレーターを集めてチェックポイントを指示し、技術的な問題が発生すると現場に行って解決します。プレスの指導も行い、品質的な部分をすべて担当しています。縫製現場は売れ筋を逃さない一着流しで、作業者の負担を軽減するためフロアにUの字のレールを敷き、その上をイスに座ったまま移動できる自社開発の「Mライン」を採用しています。レーザーマーカーを使った柄合わせ延反・CAM裁断のような自社開発も手掛けてきましたし、QC発表会も継続しています。現場ではチャコペンなどを使った印付けをしていませんが、それもQC手法で改善した一例。消えるマーカーが再発色して問題になり、今は紙ゲージを使っています。
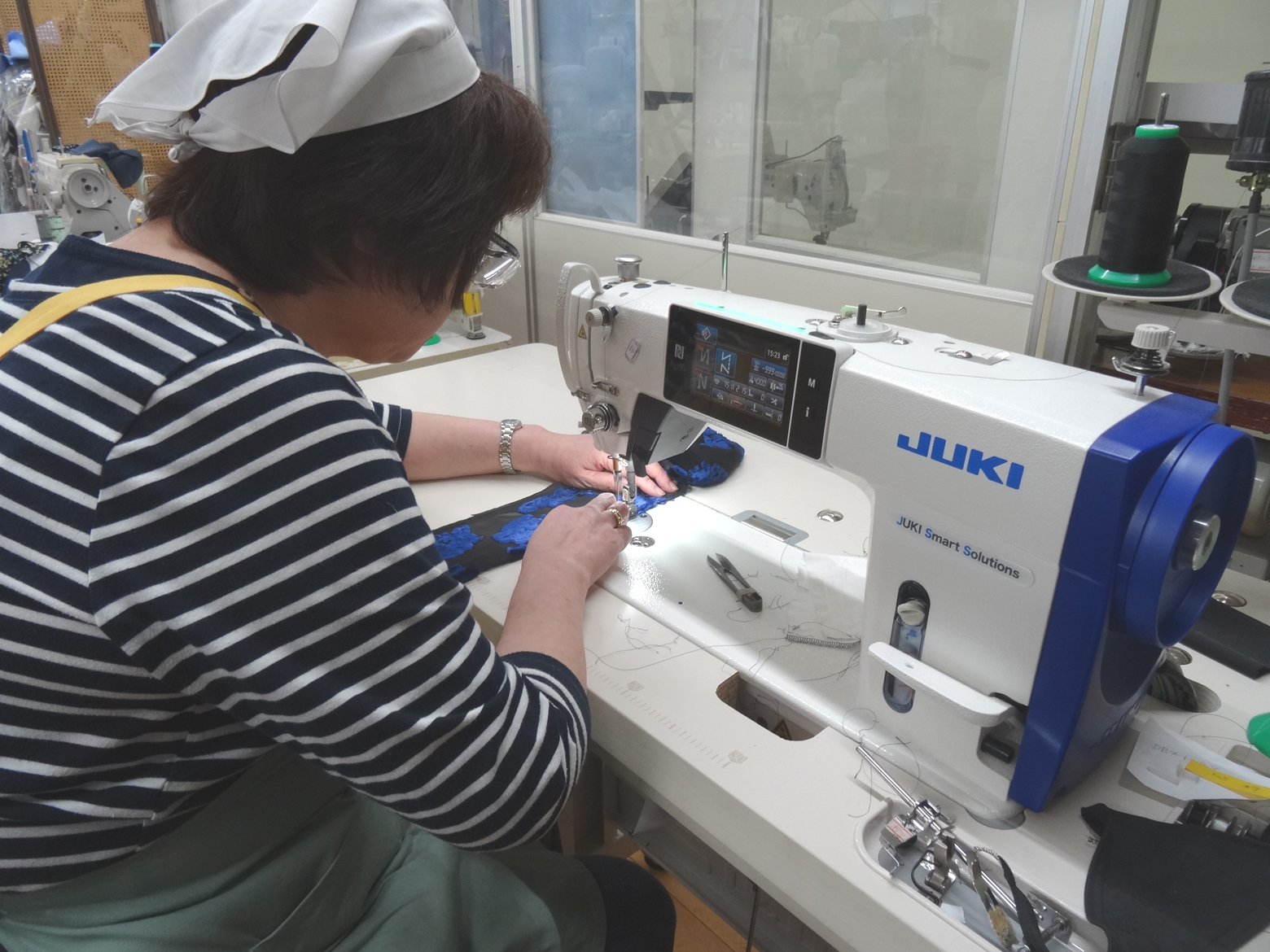
サンプル担当のスタッフが作った縫いデータを量産ラインに移行する
人手不足対策、小ロット対応に生かす
ーデジタルミシンを導入された目的は。
デジタルミシンも1人1台は変わらないんですが、人手不足が深刻化する中、新人を早く戦力化しなければいけない。特にミシンの調整はカンと経験だったので、これを数字に置き換えようというのが一つの狙いです。もう一つはベテランの方も現役年齢を延ばしてもらわざるを得なくなっています。縫製工程すべてを自動化するのは難しいんですが、置き換わる機械があれば活用していこうということです。
ーどういう使い方をされていますか。
デジタルミシンはサンプル作成に1台、サンプルや小ロットを手掛けるラインに1台、残り8台を素材がよく変わるラインに導入しています。工場長の立石(勇悦)製造部長の下にもう一人若手の保全がいますが、小ロット化しているので切り替えが頻繁に起きる場合、保全のミシン調整が追いつかないケースが出てきます。オペレーターたちも微調整をやっていますが、ベテランはすっすっとやれても新しい人はなかなかそうはいかない。素材もどんどん難しくなり、工程もいろんなところをやらなきゃいけない。デジタルミシンはサンプル作成で作ったデータを生かしてミシン調整ができるのでオペレーターの負担軽減につながり、切り替えロス低減になります。これまでデータをUSBで移していましたが、いちいちやっているのは面倒で、アプリを入れてタブレットで一発でできるようにします。デジタルミシンは送り機構のデジタル化によって素材に合わせた最適な縫いを実現できるし、段部縫製がスムーズにいくなど本縫いミシンとしての機能が高まっているのもメリットですね。
ー今後の導入予定は。
まだ導入して3カ月あまりで、保全がどこまでやって、オペレーターがどこからいじるか試行錯誤しながら使っています。そういうルール作りができた時にまた使い方も一段ギアが入るのかなという感じです。一気にはいきませんが、導入を進めていきます。
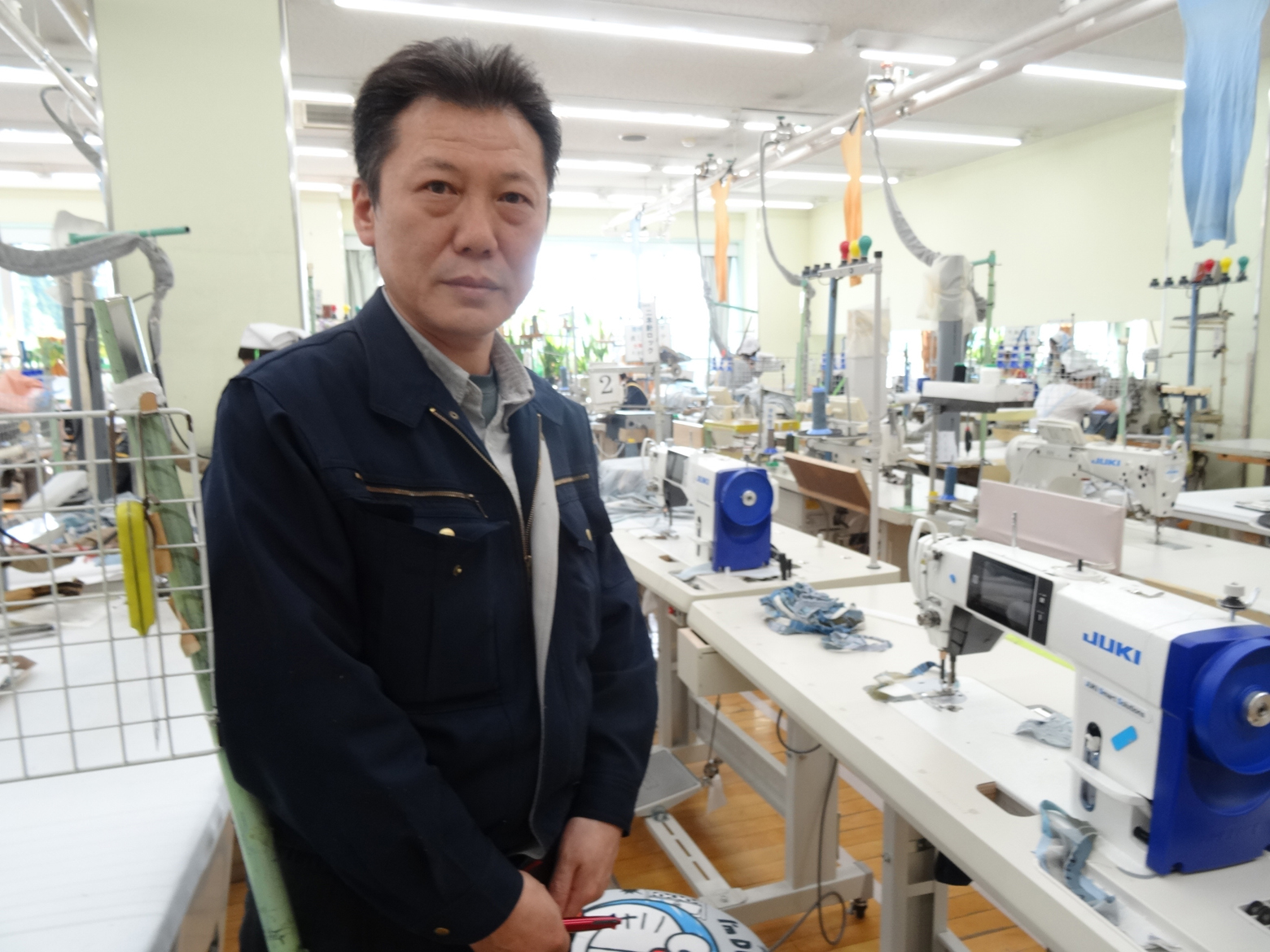
保全も担当する立石工場長は「面倒な素材が多く、調整がやりやすくなりました」と語る