次世代のモノ作りに挑戦 第14回
加茂繊維株式会社 代表取締役 角野 充俊氏
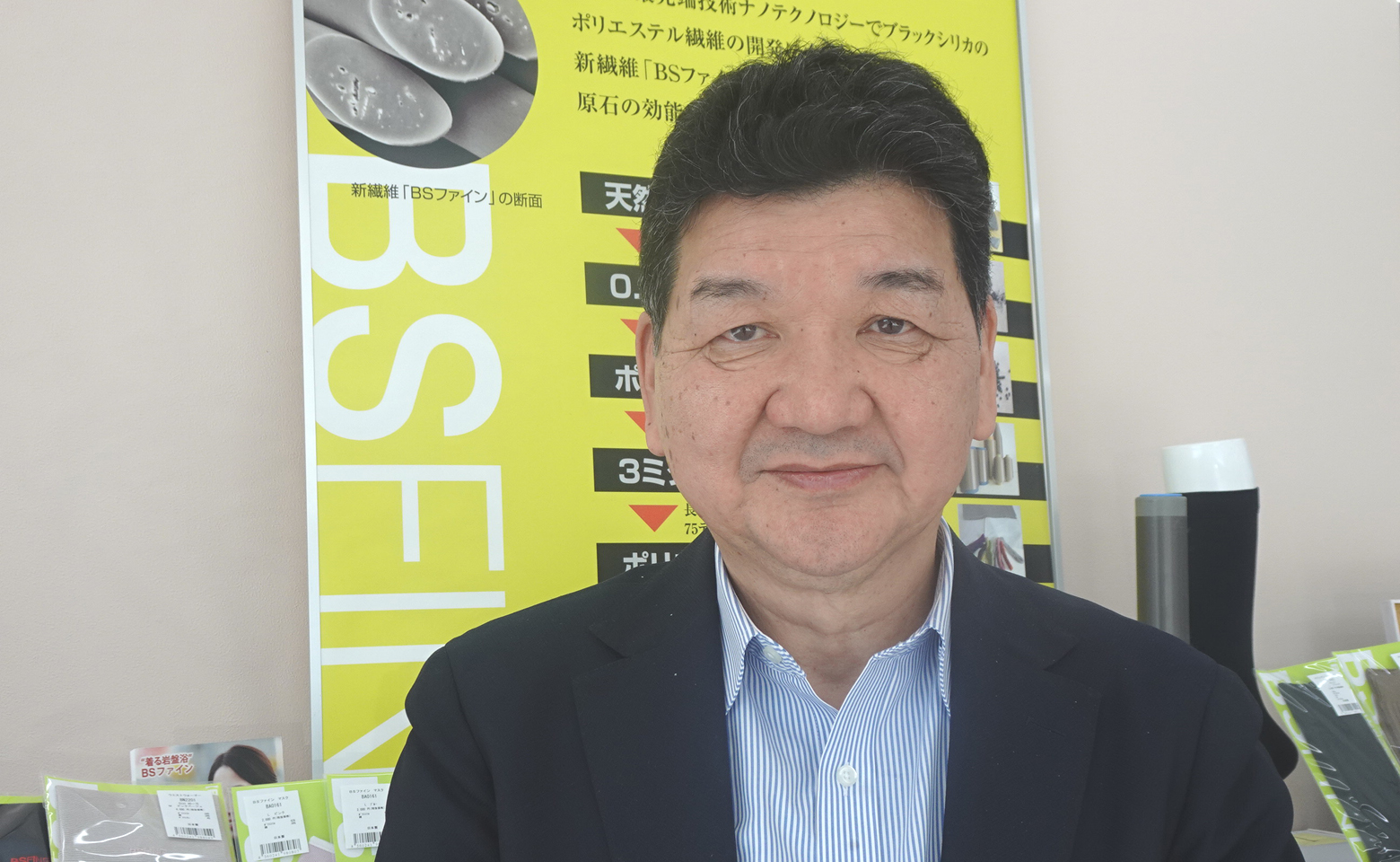
独自素材「BSファイン」の商品を展開
岡山県の県北、津山市にある加茂繊維は高機能繊維によるインナーや健康グッズなどのブランド「BSファイン」で注目を集めています。もともとはグンゼの協力工場ですが、高い縫製技術をベースに自立化を目指し、大手繊維メーカーとタイアップして天然鉱石「ブラックシリカ」を使った新たな繊維を開発、「着る岩盤浴"BSファイン"」をキャッチフレーズに掲げた製品の企画、製造、販売を軌道に乗せています。昨年3月に完成した新本社社屋の生産現場にはJUKIのフルデジタル仕様ダイレクトドライブ高速本縫い自動糸切りソーイングシステム「DDL-9000CFMS」で鳥の巣防止装置を搭載したミシンも活躍しています。角野充俊社長にお話を伺いました。
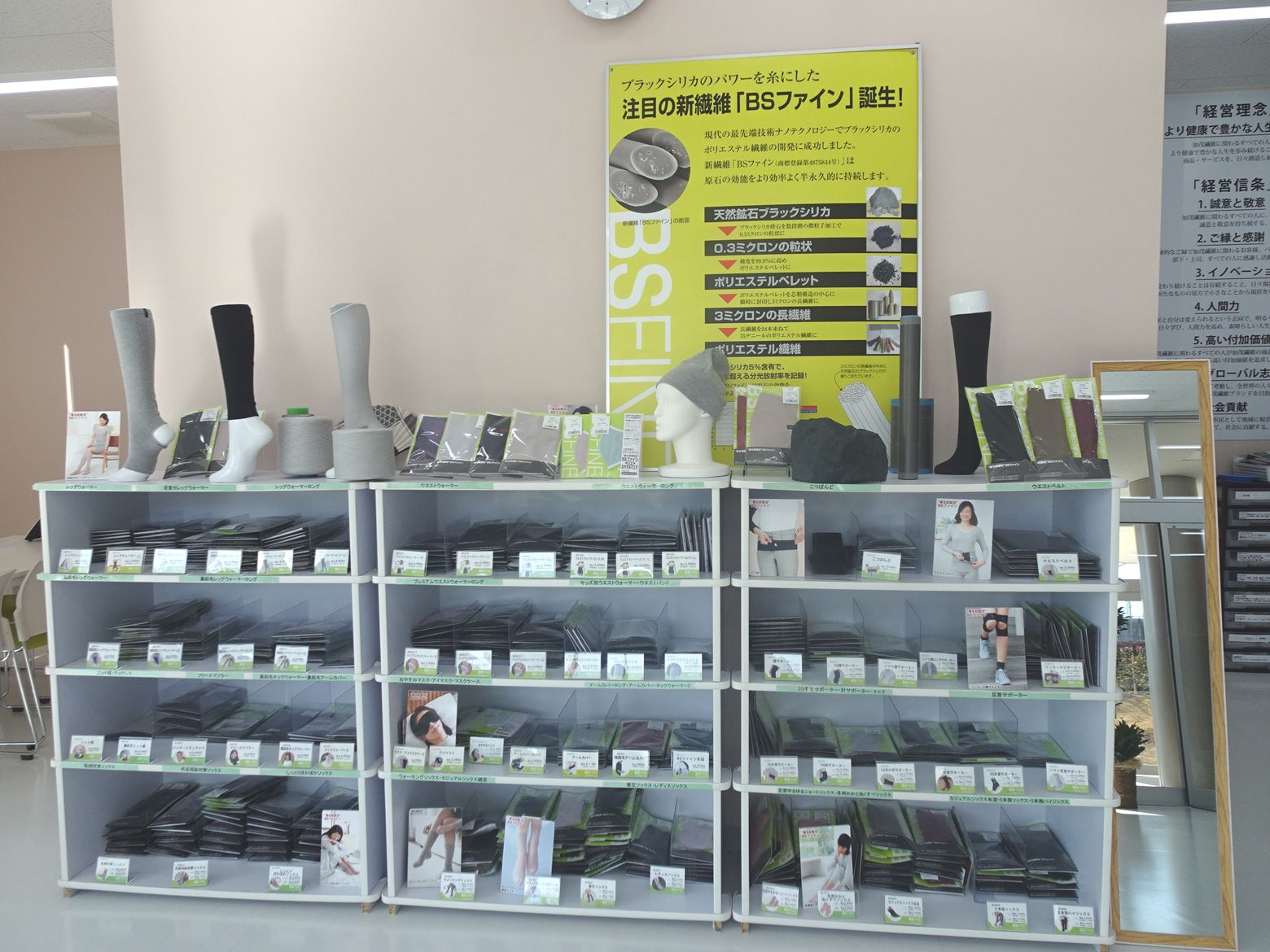
「BSファイン」の商品はすでに約300アイテムを開発し、通信販売で展開
高い縫製技術を使い得意分野で勝負
ーBSファインの事業がメインになっているそうですが。
ほぼ100%ですね。今6月期の売り上げは28億円の見込みで、グンゼさんの仕事もまだやっているんですけど0.1%くらい。現在社内の生産現場は約30人で、BSファインのレッグウォーマーやウエストウォーマーなどを中心に月間約2千アイテムを生産していますし、ソックスやマスクなどはパートナー工場に依頼しています。
ー自社商品に乗り出したきっかけは。
私は2代目で、大学を出て京都で建築設計をやっていたのですが、25歳の時、父が会社を止めると言うので受け継ぐことになったわけです。その時、工場は82人で、グンゼさんオンリーでブリーフと長ズボン下を1日1万枚生産していた。帰って5年目に第2創業期と位置づけて工場革新活動に取り組み、モノ作りを全部変えてグンゼさんの国内工場でもトップテンに入りました。しかし、海外生産へのシフトや、インナーなどの実用衣料は低価格化し、生き残るには自立化が不可欠でした。わが社はインナーウエアの縫製加工技術では日本でもトップクラスと自負していて、薄い生地も厚い生地も、伸びる生地も伸びない生地も同じミシンで縫える。そういう技術を持って、ファッションブランドも立ち上げましたが、結局はダメ。資本も知名度もない中で自立化を目指すには独自化しない限り勝負にならないと思いました。そんな時にたまたま北海道の天然鉱石ブラックシリカを親戚から紹介してもらい、これで新しい繊維素材を開発しようとしたら、周りからはけんもほろろ。諦めきれずにいたら、大手繊維メーカーの研究員の方が取り組んでくれることになり、ポリエステルのBSファインが完成したわけです。それで最初はインナーウエアを作りましたが、まったく売れない。ところが知り合いや関係者に配ったら、みんなほかのインナーが着れなくなったという。ちょうど健康食品が通信販売で伸びており、我々も通信販売を立ち上げてやったのですが、それでも低空飛行。当時まだ社内では約35人でグンゼさんの仕事をしており、会社がつぶれるか、BSファインが成功するかという瀬戸際で、徹底して通信販売を研究しました。
ー軌道に乗ったきっかけは何だったのでしょう。
少しづつ販売が形になりかけた頃に大手SPAの保温性下着が発売され、機能肌着のマーケットができたんです。加えて、我々の事業を後押ししてくれる制度がありました。最初は2003年度の岡山県の「夢づくり・オンリーワン企業育成支援事業」、2004年と05年度は2年連続で「中小繊維製造事業者自立事業」に採択され、2006年度は中国経済産業局の「地域産業資源活用事業計画」の認定を受けました。そこからもう一度きちっとしたスキームを作った。この3年間は150%成長を続けています。
ーBSファインの特長は。
私どものインナーウエアは1年中同じものを着用できるんです。夏でも体が冷えない。着ている方が汗をかきません。足下商品を付けていると足も疲れません。それが暖かいだけの商品との違いで、お客様が実感され、口コミでどんどん広がった。もう一つ大きなことは素材開発を継続しています。この素材は応用範囲が広く、昨年はBSファインを使ったイスを発表しました。アパレルだけではなくして、これからBtoB(企業間取引)の様々な分野を開拓していくというのがマスタープランです。また、ネット販売、海外展開にも取り組んでいく計画で、5年後にトータルで100億円の売り上げを計画しています。
ー生産現場はセル生産方式を導入されています。
だいたい1人で数台のミシンをぐると回って1つの商品を作っています。数量がたくさんあるものだったら2人で流す。ミシンも標準的なものではなく、全部自社で切り刻んで改造しています。例えばペダルは最初から要らない。立ち作業だからボタンの方が労働負荷がなくなる。押さえも送りも全部改造しているので、わが社のルーパータイプのミシンは1日2千枚縫って、目飛びは月に2、3個だからほぼゼロです。
ネーム付けに鳥の巣防止仕様「9000CF」を活用

鳥の巣防止仕様のフルデジタル「DDL‐9000CFMS」を使ってネーム付け
ーJUKIとの関係も長いそうですね。
JUKIさんは中四国エリアの担当者の方ともう20年以上のお付き合いがあります。我々の生産の仕組みに対応できるように開発がらみのことをやって頂き、できなさそうなことも実現してもらいました。
ーネーム付けに鳥の巣防止装置付きの9000CFMSを活用されています。
タテ・ヨコ3cmの7mmのネーム付けに活用しています。縫っている時間より、縫製後の糸始末に時間が掛かっては大きなムダになりますが、それが解消されました。わが社のミシンは全部改造していますが、デジタルミシンはそれも不要で応用範囲が広い。今までの縫製はオペレーターのカンと経験でやっていましたが、デジタル化が進んでいけばもっと安定したモノ作りが期待できます。
ー今後については。
BSファインは自分たちだけでやっても市場はしれています。例えばソックスメーカーも現在4社と取引し、各メーカーしかできないものを作っているんですね。毛布も和歌山の織物メーカーさんと組んでいます。日本国内には優秀な技術を持っている中小企業さんがたくさんあり、そういう方々とパートナーシップを組み、お互いにこの素材を生かして自立化できる事業を広げていく。それによってみんなで日本にモノ作りを残していけたら一番いいと考えています。

高速電子閂止めソーイングシステム「LK-1900BN」も稼働
この導入事例に出てきた製品・サービス
DDL-9000CFシリーズ [プレミアムデジタル]
ダイレクトドライブ高速本縫自動糸切りソーイングシステム
<p>「縫い」の創造。<br />
「縫い」へのこだわりは、次世代ソーイングシステムで変わります。<br />
これまで勘や経験に頼ってきたミシンの調整をデジタル化。<br />
素材に最適な縫いをいつでも再現できるのが、デジタルソーイングシステム、DDL-9000Cです。</p>
詳細を見る
LK-1900BNB(鳥の巣防止/残短仕様)
LK-1900BN(標準仕様)高速電子閂止めソーイングシステム
<p>縫い調整の「常識」が「感動」に変わる。ミシンの歴史を変える次世代ソーイングシステム。 生産に携わる全ての人に、デジタルソーイングシステムがスマートで新しい価値を提案します。</p>
詳細を見る