生産現場に『JUKI』を探る Vol.11
アパレル生産現場第10回
尾崎商事株式会社 米子工場
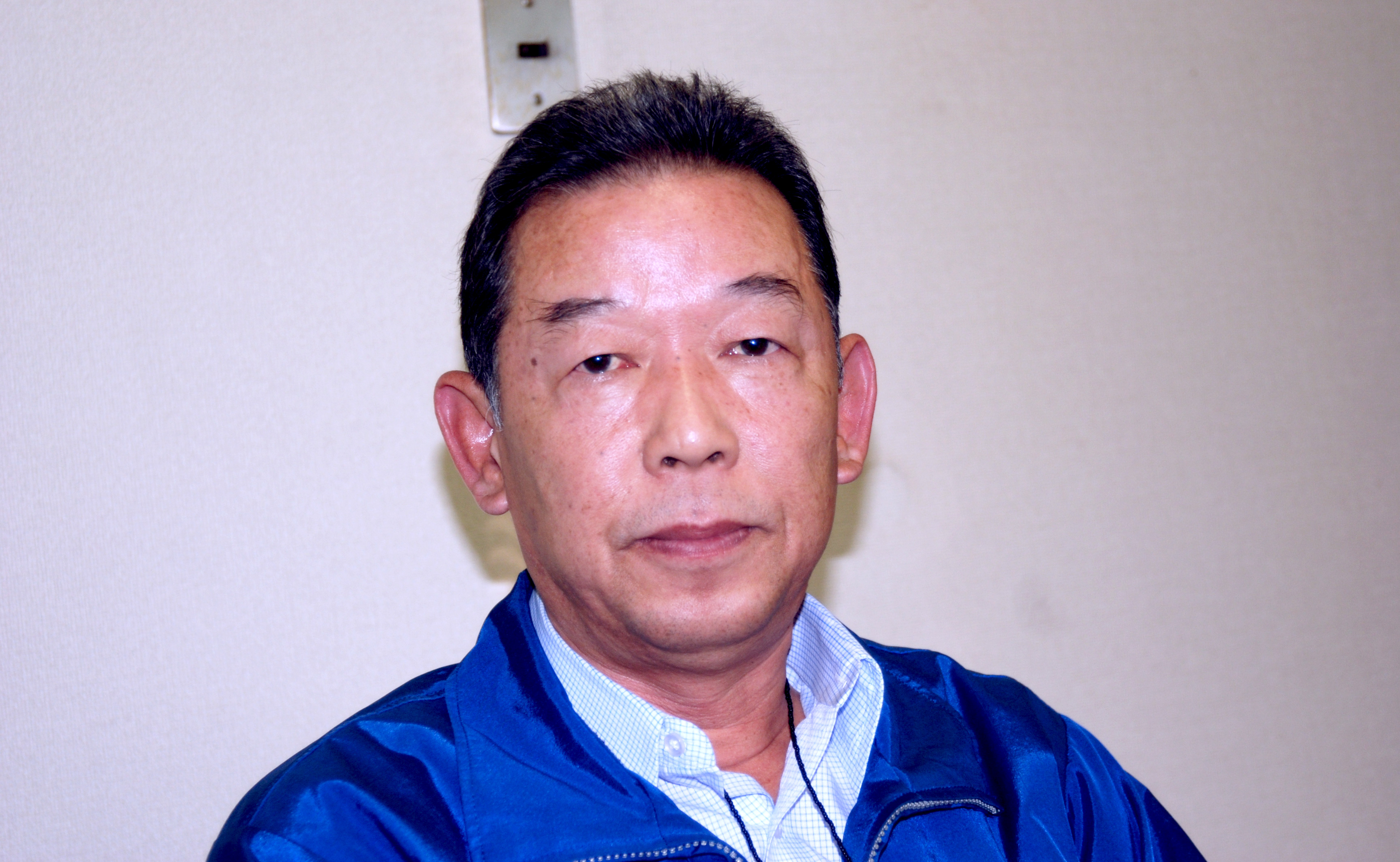
尾崎商事 米子工場工場長 宮脇敏博 氏
創業が1854年(安政元年)、スクール衣料最大手の尾崎商事は、伝統あるブランド力と高い企画力、地域に密着した販売力を支える強力な生産ネットワークを構築している。国内に本社工場(岡山県)、米子工場(鳥取県)、都城工場(宮崎県)、志布志工場(鹿児島県)の4つの基幹工場を持ち、さらに4基幹工場を軸に周辺に子会社の衛星工場を配するという体制は国内最大規模を誇る。今回は、その中で県外第1号工場として1964年(昭和39年)に操業開始した米子工場を訪問した。
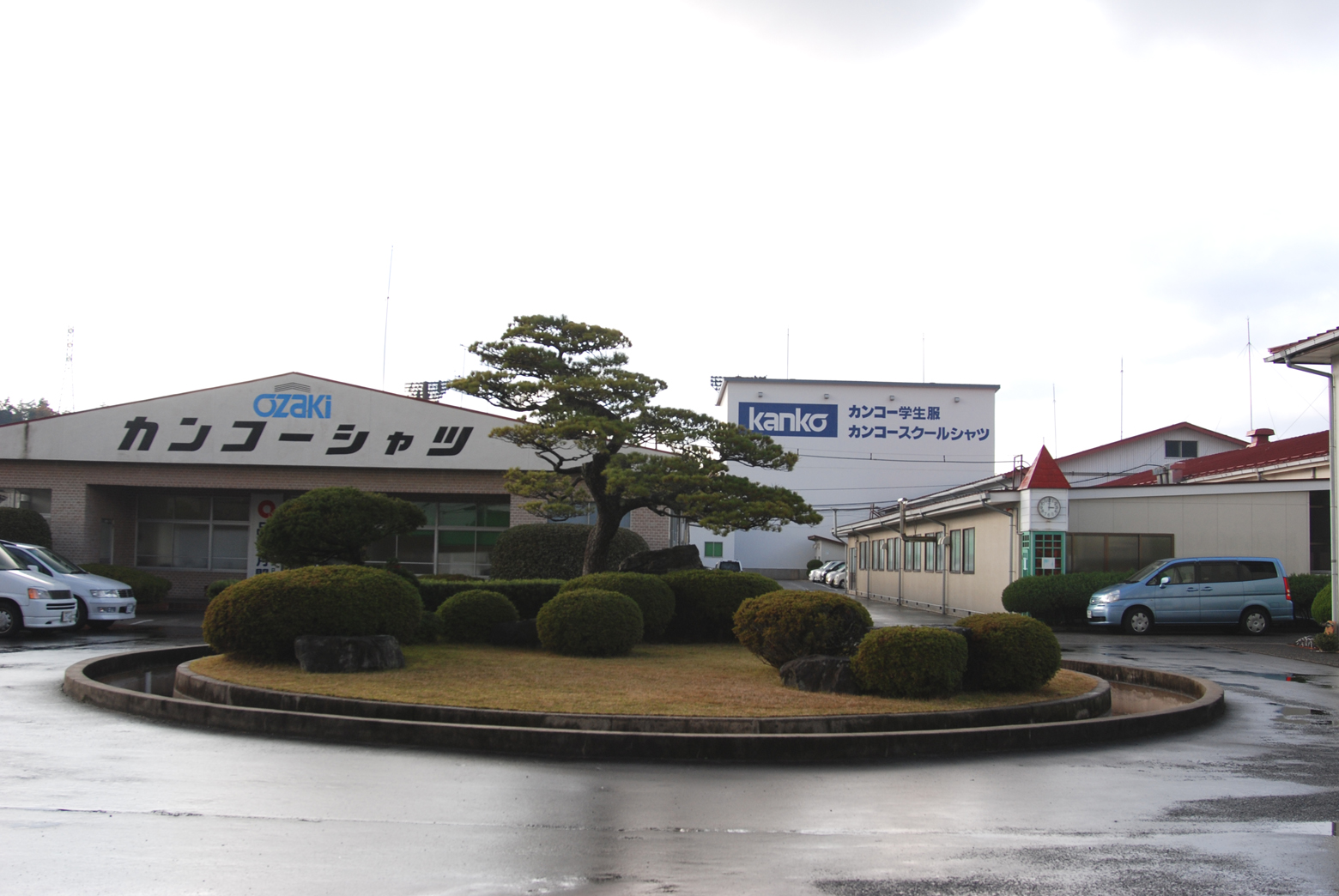
尾崎商事の基幹工場の1つである米子工場
国内最大のシャツ工場
尾崎商事米子工場は布帛シャツ・ブラウスを年間約50万枚生産しており、尾崎生産グループでは唯一の布帛工場である。一方、基幹工場である米子工場のグループとして、40人~60人規模の6つの衛星工場(大山工場、伯太工場、島根工場第1工場、島根工場第2工場、大田工場第1工場、大田工場第2工場)がある。衛星工場では主に白物のニット体育衣料を年間約220万枚生産している。従業員数は米子工場が230人、衛星工場が合わせて280人で、米子工場グループでは合計510人にのぼる。
米子工場は布帛シャツの工場ということで、かつては自動機の導入、工場独自の半自動機の開発を積極的に進めてきた。人員もピーク時には650人に及んでいた。しかし、その後、商品の多様化、小ロット化、多頻度化、短納期化が進み、自動機の使用が減っていった。現在、自動機はポケットセッター、ボタン穴かがりインデキサー、ボタン付け、カフス地縫い自動機ぐらいである。
以前の量産型に代わって、生産工程にはTSS(トヨタ生産方式)を採り入れ、立ち作業・小編成・多能工化で、現在はカッターシャツ5ライン、ブラウス2ライン、計7ラインが部品~組立~仕上げまで、縦割り一貫生産ラインとして稼働している。従来の1人が1工程を受け持つ作業から、1人が3工程を受け持ち、1工程を3人が出来るという「多能工化・3×3」の目標に挑戦し、実現を図ってきた。
その基礎になっているのが、長年にわたる社員教育、とりわけ技能教育と小集団活動(QCサークル)である。先月、厚生労働大臣が国内の卓越した技能者を表彰する「現代の名工」(卓越技能者)に、同社の吉良美子生産課長が選ばれたが、これこそ米子工場の技能レベルの高さを象徴するものだった。
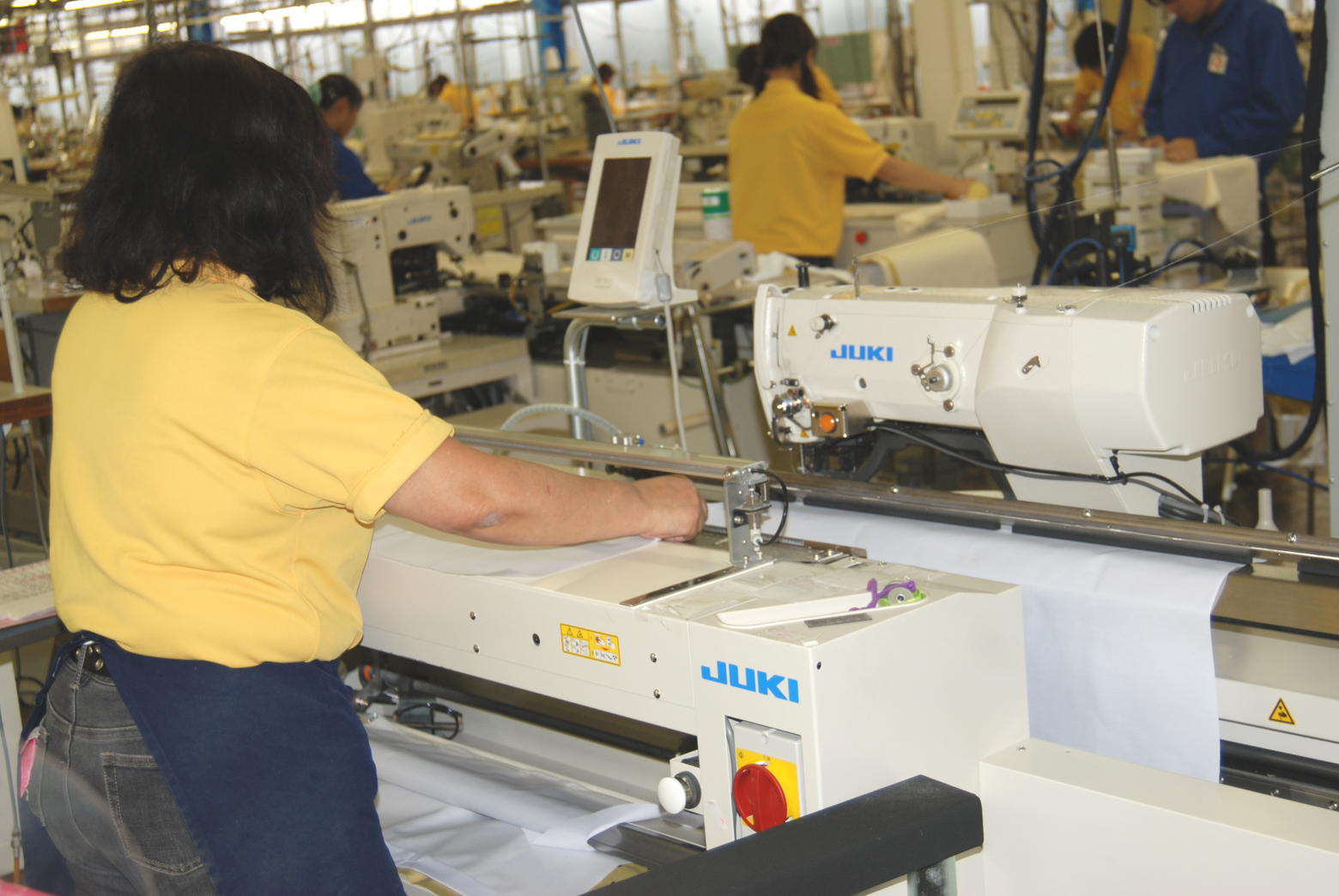
最近導入したボタン穴かがりインデキサー
多能工化で多機能ライン
「現代の名工」生む技能者集団
「現代の名工」吉良美子生産課長を頂点とする同工場の技能者の層は厚い。1つの指標である技能検定の国家試験(布帛縫製技能検定・ワイシャツ製造作業)合格者は、これまでの累計で2級155人、1級42人。現在、約90人の合格者が在籍しており、そのうち20人が1級合格者だ。受験に備えて1年前から計画し、時間外に係長、リーダークラスがそれぞれの工程をマンツーマンで指導する。吉良課長は、「現場では工程の役割分担が決まっているが、技能検定の試験では全ての工程を知る必要がある。それぞれの関連工程を知ることによって、『次の工程はお客様』ということが理解できる」と技能検定試験の効用を説く。
多能工化への取り組みは日々の作業の中で行われるが、これも計画的。生産課長が7月までに多能化計画表を作成。その計画に基づき係長やリーダーが、付きっきりで指導していく。ビデオで上手い人の映像を見せたりするが、「経験や勘、コツといったものを伝えるのは現実には難しい」と吉良課長。そこで登場したのが、勘やコツを必要とする工程の手順書を図解入りで説明した吉良課長による『マイスター・ニュース』。生産現場の入口の大きなボードに貼られており、いつでも見られるようになっている。吉良課長は今回の「現代の名工」受彰に先立ち、2002年に卓越した技能者に与えられる「とっとりマイスター(鳥取県高度熟練技能者)」、2004年に社内の「OZAKIマイスター」に認定された押しも押されぬマイスター。吉良課長は「会社や先輩、上司をはじめ回りの人たちの協力で受彰できた。これからはお返しするつもりで後輩の皆さんに持っているものを伝えたい。その方たちの能力や技術力に応じて時代に合った縫い方の指導をしていきたい」と話す。
こうした努力の結果、「1人3工程。1工程を3人が出来る」という目標を掲げた多能工化は着実に進んでいる。宮脇敏博工場長は、「このように多能化がどんどん進んでいくと、少ない人数でもラインが編成できる」と話す。定番は海外へシフトされ、いわゆる学校別注が国内に残っている現状。デザインや素材の多様化による少量多品種、多頻度、短納期。ロットは今や最大で300枚。シーズンになると、1枚からになることもある。小ライン化による生産性アップは大きな課題だ。
こうなってくると、機械の選択や使い方も当然変わってくる。「ブラウスのように工程数が倍近くに増えただけではなく、難しい素材が多く、今は腕というか技術だけではなく、設備調整の技術力もないとやっていけない」と吉良課長。しかし、自動機の使用は減ったが、新たな視点で自動機を見直す動きもある。その点でミシンメーカーへの期待は高い。最近、米子工場はJUKIボタン付けインデキサーの2台目を入れた。生産現場のミシン台数は合計350台。「半自動機をバラして、単体の本縫いなどにシフトしていたために、全体としてのミシン台数は減ってはいない」(小笹彰副工場長)。本縫いミシンはほとんどがJUKI。今年からDDL-9000Aを入れ始めている。白物が多いため油汚れが問題で、ドライタイプへの関心は高い。
今後の工場の課題として宮脇工場長は、「国内で生きていくためには、シャツだけに固執するのではなくて、違う服種も米子工場の中に流せるようにしていく。そのためには、吉良さんに続くような人材を育てていかないといけない」と話す。より次元の高い多能工が求められている。
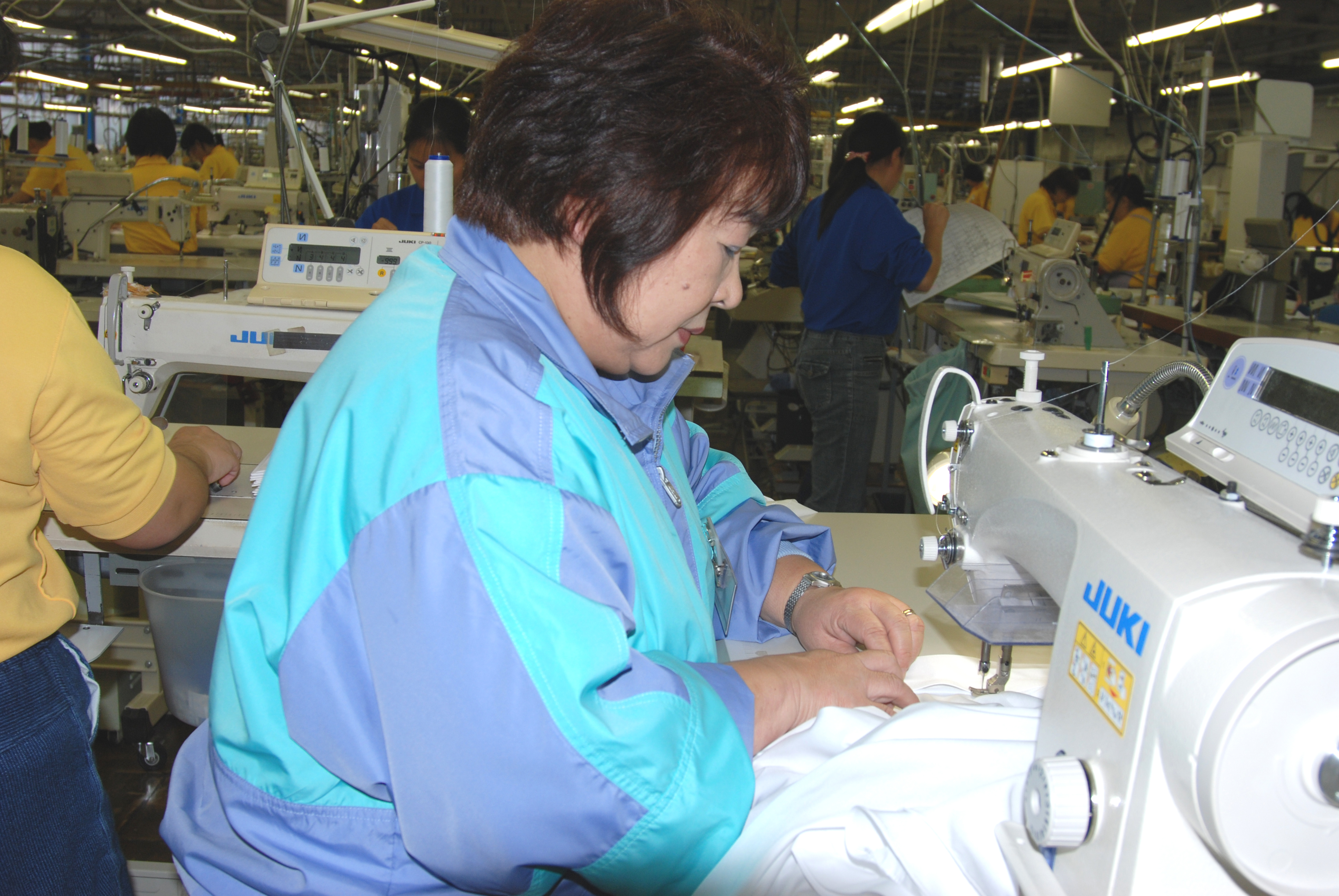
JUKIのDDL-9000A-SSを操作する「現代の名工」吉良美子生産課長
JUKIから「この一台」
ダイレクトドライブ高速本縫自動糸切りミシンDDL-9000Aシリーズ
2008年度のグッドデザイン賞(Gマーク)を受賞
DDL-9000Aは、縫製作業の動作分析からスイッチの大きさ、調整つまみなどの扱いやすさや見やすさ、縫製作業者の動作を改善した大きなふところ…など、人間工学の視点から機能を見直しデザインされたDDL-9000のフォルムを受け継ぎ、さらに高い次元へと進化させたモデルです。いま一度原点に立ち返り、迅速で快適な作業を実感できる送り力の向上や素材変化への対応力(可縫範囲)の強化など機能アップも達成しています。
開発にあたって、私たちが大切にしなければならないと受け止めたのは、JUKI本縫いミシンが世界標準機として世界中の縫製現場で使用されており、オペレーターの労働環境に大きく関与するということでした。ミシン操作の基本は維持したままで、プロのオペレーターが高品質な縫製物を短時間で効率よく仕上げていくための基本要件である「縫い品質」「針元の見易さ」「布の取り回しやすさ」「ふところの広さ」を追究し、さらなる疲労の低減に寄与するやさしさの実現と生産性向上を目指しました。もちろん工場のメカニックの方が求める「調整・メンテナンス性」も原点に立ち返って徹底的に作り込んでいます。
オペレーターのスムーズな動きを助けるクリーンで力強いフォルム、着座姿勢で楽に調整作業が行えるマシンレイアウト、耐久性・振動・騒音・材料・加工・コストなどの機能的な要求を満たした合理的で美しいデザインは、2008年度グッドデザイン賞を受賞。「世界中のプロが使う最高峰モデルとして、信頼感を感じさせるデザインである」など高い審査員評価をいただきました。
JUKIは、これまでも、これからも、ミシンのデザインが縫製現場のオペレーターの心と身体の労働環境に大きく関与するものであることを踏まえ、工業用ミシンの世界標準機としてお客様に愛され、信頼されるミシン作りを続けてまいります。
【JUKIデザイン室】