生産現場に『JUKI』を探る Vol.17
アパレル生産現場第16回
矢部プロカッティング
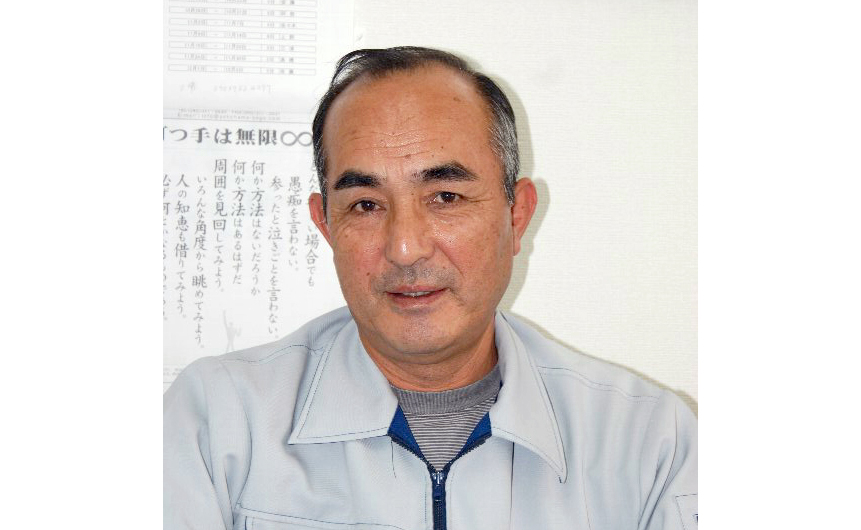
矢部プロカッティング 工場長 三浦 功 氏
「シーガル」ブランドの幼稚園園児服、学校制服で知られる矢部プロカッティング(本社横浜市、矢部秀久社長)。1972年(昭和47年)に操業開始した自社工場の仙台工場は、午前中に注文があれば翌日には届けることのできる『コンビニ感覚』を標榜する工場である。「帽子、靴下、靴を除き、カバンも含めてミシンで縫うものは全て作っている」(三浦功工場長)ため、あらゆる種類のミシンを揃えているほか、刺しゅうやプリーツ、マーク付けなども内製化し、クイックの注文に応える。国内の工場でしか出来ない仕組みを作り上げている。
「コンビニ感覚」の一貫工場
前日に受注し、翌日に納品も
JR仙台駅から仙石線に乗り、「東矢本」で降りると、一面に田園風景が広がり、正面前方に矢部プロカッティング仙台工場の社屋が見える。およそ十分歩いて工場に辿り着くが、農道とは言え県道と見紛うばかりの道路が反対方向から工場の脇まで伸びている。工場と同一敷地内にある物流センターからは毎日、この道路を使って全国に配送される。地方工場でありながら、営業の前線から送られてくる情報とリアルタイムで繋がる「都市型工場」である。
矢部プロカッティングは幼稚園だけで1,700を超す納入先を持つ。スクール・幼稚園ユニフォームは耐久性・機能性に加えて、最近の流行を取り入れたデザイン性など常に新しいものを供給することが求められる。さらに、「今のお母さんたちはコンビニ感覚で、欲しいときにすぐないといけない。午前中に注文があれば、翌日の午前中には幼稚園に届けるのが基本。明日の卒園式に間に合わせたいと、その日のうちに出荷することもある」と三浦工場長。
こうした要求に対応するためには、受注・在庫・仕掛かり・出荷管理など全社的なネットワークとともに、工場として安定したものを供給するための生産のシステム化が必要だ。特に裁断がネックだったため、約20年前にCAD、それから5年後にCAMを導入して前工程を整備。現在考えられるほぼ完璧なシステムを構築した。
従業員は現在、約80人だが、縫製人員は35人。他は裁断11人(CAD5人、CAM6人)をはじめ、刺しゅう、プリーツ加工、品質表示(プリント)など、いわゆる間接人員が多い。1991年(平成3年)に出来た稚内工場(20人)の分まで裁断、プレスまで行う。
「何でも縫わなければならない。また、生産性を優先する時期と、納期を優先する時期があり、その使い分けをする。それによって素材、機械を用意する。機械も時期によっては何カ月も全く使わないが、それでも持っていなければならない」(同)。裁断に続く縫製・各種加工のための機械設備は、同社の扱いアイテムと受注形態から来る特有のものである。
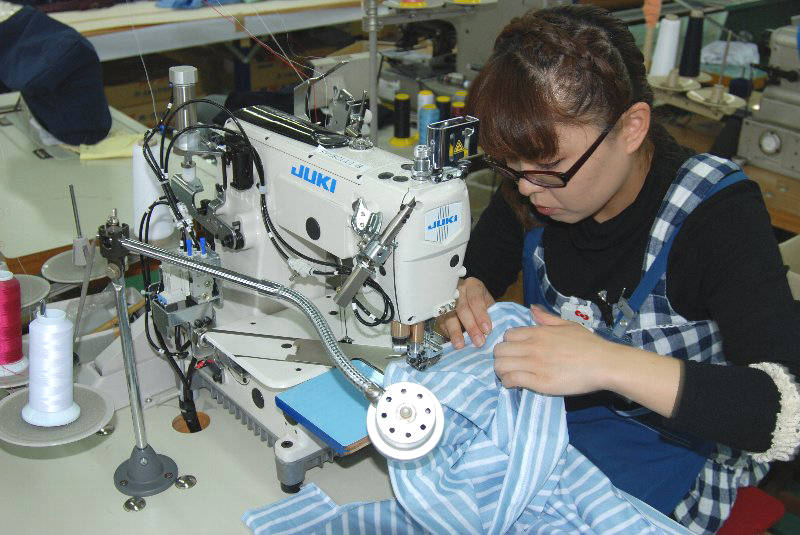
ドライは製品の油汚れだけでなく職場環境にも貢献(導入を会社に上申し、喜々として「MF」を操作する高橋恵美さん)
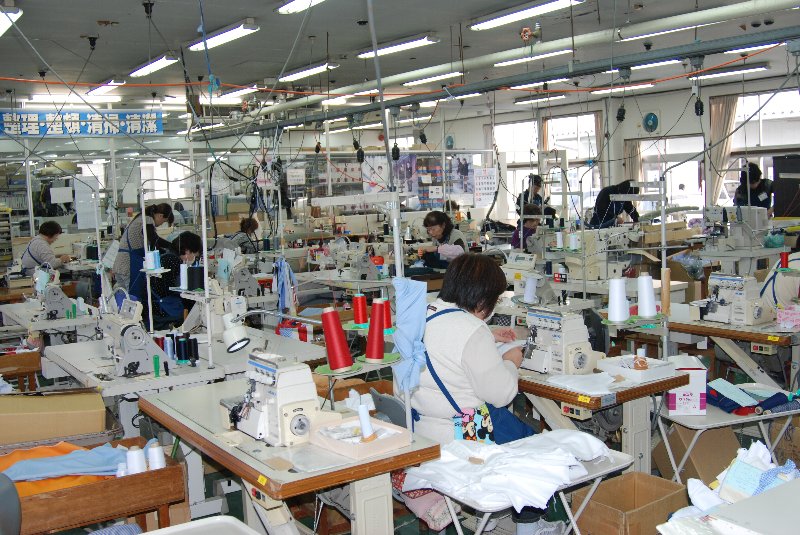
あらゆるミシンを揃え、多様な受注に対応
「ドライ」が職場環境に最適
ミシン台数は90台。そのうち60台はJUKIのミシンで、台数の多い本縫いは約20年前に入れた「5570」タイプがまだ現役で活躍している。しかし、さすがに更新の時期にきており、ここへ来て「ドライ」のミシンへの入れ替えを進めている。今年、DDL-9000A-SSダイレクトドライブ高速本縫自動糸切りミシンを五台とMF-7823D-U10-B64セミドライヘッド・シリンダーベッド両面飾り偏平縫ミシンを1台入れた。設備投資は今年、600万円と例年より減ったが、これまでは毎年、1,000万円から1,500万円の設備投資をしてきた。
ドライについては、製品の油汚れはもちろん、女性が働く職場環境の観点からも積極的な評価をする。「特に今の女性は汚れを嫌うし、油をいやがる。油汚れを気にしないで縫えるということが大事。入れて数カ月になるけど、ミシンがいつもキレイ。今後は5台位ずつのペースでドライの本縫いを入れていく」(同)考えだ。今年6月に開かれた東北ミシンショー。同社はバスを仕立てて社員が見学したが、飾りのドライのミシンから離れなかったのが若い班長の高橋恵美さんだった。彼女の要望を入れて前記のMFを入れたという。今は2本針で見本や試作に使っているが、「先を見越していろんな商品に対する対応を考えている」(同)ところである。
刺しゅうは以前、刺しゅう屋さんに頼んでいたが、今は社内だ。「襟のラインを入れたらすぐに入れたいとか、縫製している最中に入れたい箇所がある。最初に入れると、ラインを入れる時にずれてくることがあるので、セーラーなどはラインを入れた後に、下まで通さないで入れたい。刺繍は中間で入れられるのがベストだ。縫製に合わせた刺繍が入れることによって生産の効率、納期的なものも管理が出来る。プリーツも同じことが言える」と三浦工場長。マーク入れ(ミシンと高周波)、品質表示関係も全て社内で行っている。品質表示は一枚からでき、在庫の負担も解消した。内製化を進め、「全て工場の中で1つのものが出来るようなシステム化。ここまで来るのに15年くらいかかった」という。
従業員は全員が地元の人たち。グループ縫製で1人が多工程を持ち。流れるものが1日おきならぬ何分おきに変わることもある。1人ひとりの自主性が求められるし、そうでなければ回って行かないだろうと実感させる生産現場。かなり大変なことを、当たり前のようにこなしているのが印象に残る工場であった。
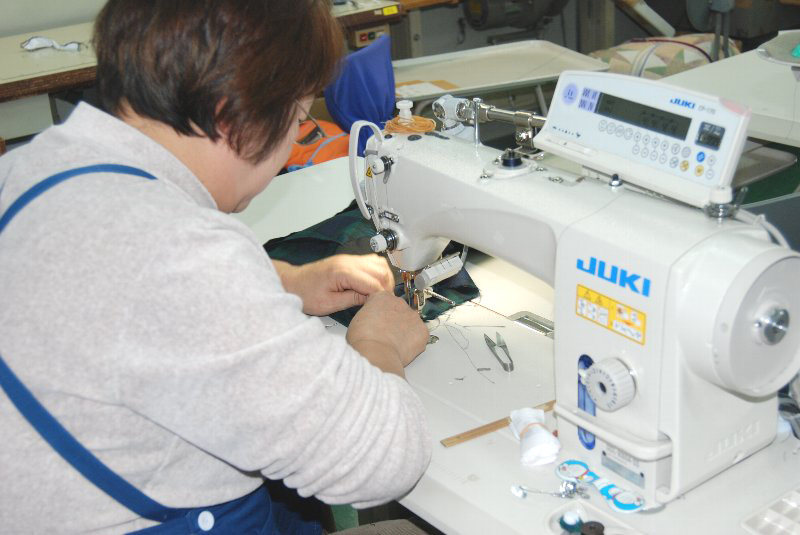
5台単位で本縫いミシンもドライに切り替え(写真は今年入れたDDL-9000A-SS)
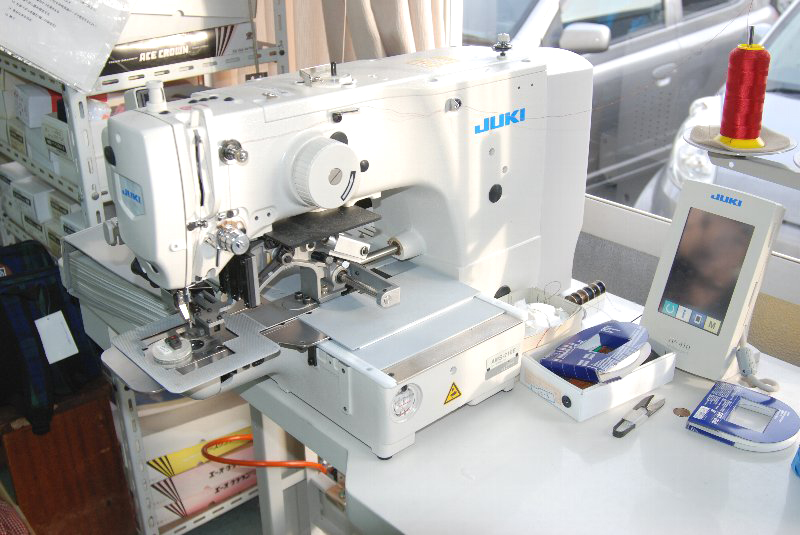
入力機能付き電子サイクルマシンAMS-210EHL
JUKIから「この一台」
セミドライヘッド・フラットベッド/シリンダーベッド両面飾り偏平縫ミシン
MF-7700D、MF-7800Dシリーズ
飾り縫いでドライ技術を展開
飾り縫いミシンを主に使われるニット業界では、消費者まで届き不良返品となった商品の実に4分の1は油汚れと言われ、最も重要な改善項目に挙げられています。
JUKIでは、これまで本縫いミシンや特殊ミシンで培って来た最先端のドライ技術があり、世界で初めて飾り縫いミシンにドライ技術を展開したのが、このMF7700D、7800Dシリーズです。
優れた縫い品質と生産性で定評のある、MF7700D、7800Dシリーズをベースに、油の飛散の要因となる面部機構に限定しドライ化を実施することでコストを抑え、実用的なセミドライ飾り縫いミシンとして製品化しました。
構造的には、油の飛散が発生しやすい針棒機構が入っている面部を無給油化するために主要駆動部への表面処理の採用や、潤滑方式の最適化を図り、高速性を維持しつつ、耐久性に優れ、長期間安心してご使用頂ける飾り縫いミシンを完成させました。
従いまして、油汚れによるシミ抜き作業や、縫い直し作業が低減し、生産性の向上につながる上、環境問題に関しましても、油の飛散が無いことや、埃の混入による潤滑油の汚れも少なくなるので、交換頻度も減少し、潤滑油自体の使用量の削減に貢献します。またシミ抜き剤使用量も削減でき、環境にやさしいミシンといえます。
またJUKIオリジナルのインナーウエア用のソフトな縫い目とアウターウエア用のハードな縫い目を切替える機能もそのまま継承し、サブクラスに関してもトレーナーなどのカバーリング工程に使われる仕様、肌着などのテープ取りに使われる仕様、Tシャツ、ポロシャツなどの裾ヘム縫いに使われる仕様などお客様の製品にあった商品もラインアップしております。
【コメント】工業用ミシン事業部商品企画部