生産現場に『JUKI』を探る Vol.20
アパレル生産現場第19回
高山CHOYAソーイング「信州工場」
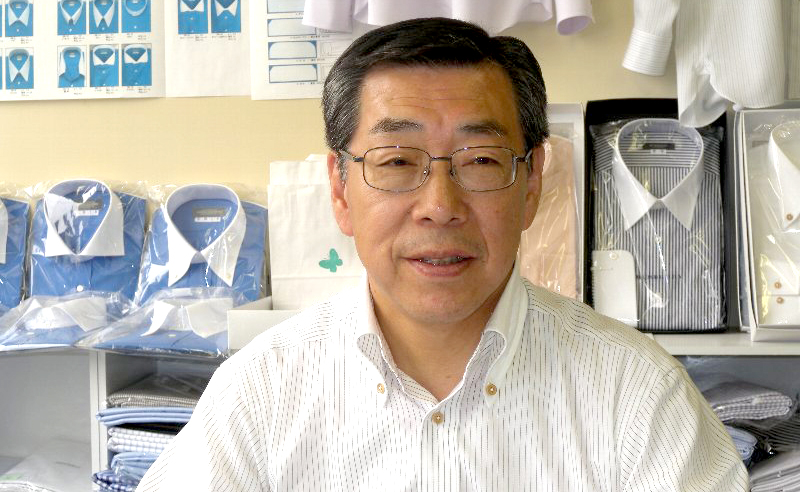
取締役社長 坂本 英信氏
メンズシャツはいち早く海外生産シフトが進んだアイテムだが、CHOYAの生産子会社である高山(こうやま)CHOYAソーイングの「信州工場」は、既製品からフルオーダーシャツに転換することによって国内での生き残りを図った。再生後4年目の昨年から黒字化を達成、新体制が軌道にのったという。今年4月にはJUKIのダイレクトドライブ高速本縫い自動糸切りミシン「DDL-9000B」を5台導入し、設備更新などによって〝ジャパン・クオリティ〟の更なる基盤強化を進めている。
フルオーダーシャツで再生
長野県佐久市にある信州工場は、老舗シャツメーカーCHOYAの自社工場として50年以上の歴史を持ち、業界でも知られた存在だった。一方、高山CHOYAソーイングは1990年4月に鹿児島県肝属郡高山町(現・肝付町)にCHOYAの生産子会社として設立、同年10月から稼働してきた。CHOYAは2004年3月に日清紡が親会社になり、生産体制も見直される中、信州工場は05年2月にCHOYAから高山CHOYAソーイングに業務移管され、同社の信州工場として再出発した。
「既製品シャツが海外生産に移行し、高級品を手掛けていた信州工場も雇用を守っていくのが大変になっていた。しかし、半世紀を越す信州工場の技術は認知されていたし、お金では買えない資産であり、何とか生かす道を探ろうということがきっかけで高山の傘下となり、フルオーダーシャツの工場に全面的に切り替えた」。高山CHOYAソーイングの阪本英信社長はこう経緯を説明してくれた。
もともとCHOYAではオーダーシャツを協力工場主体に作ってきていた。しかし、零細だったり高齢化が進んでいたため、「オーダーのしっかりした生産拠点を構築しモノ作りをしていこう」(阪本社長)という狙いから、信州工場が高山傘下になったのを機に本格的にオーダーシャツ工場としてスタートしたわけだ。その後、国内の既製品の生産拠点であった高山工場も受注が減少し、07年10月から既製品に加え、オーダーシャツ生産に乗り出す。
人員は中国人研修生を含め、信州工場が124人、高山工場が160人である。現在、CHOYAのシャツの年間販売数量は約200万枚。このうち約35万枚がオーダーシャツで、20万枚を2工場で手掛けており、信州工場が11万枚、高山工場が9万枚を生産、残り15万枚を協力工場に依頼している。
信州工場が生産するオーダーシャツは東日本の百貨店が販売した商品で、上代は1万5千~2万円。CHOYAのブランドや百貨店のプライベートブランドがあり、扱うのは10数ブランドにのぼり、素材も1千種類以上。フルオーダーシャツに切り替えて最も難しかったのは、「オーダーは1着ずつお客様の承り伝票にすべての情報が入っている。それを読み切って全員に徹底させ、お客様に満足して頂ける商品を作ることで、その経験が必要なため軌道に乗るまでに4年掛かった」と阪本社長は明かす。
また、オーダーは繁閑差が大きいことも大型工場では難しかった理由の一つ。信州工場ではそのために操業度を最低75%、最高125%の変更が出来る体制にした。これまでの受注統計から設定したもので、具体的にはこんな対応を取る。
年間でオーダーシャツのピークは1月と5月で、この2カ月は定時を1時間延長して1日の労働時間は8時間45分、土曜日休日もゼロ。逆に閑散期の2月と9月は労働時間を6時間45分とし、午後4時に退社。各週とも土日は休日で、うち1週は3連休。これ以上に閑散期が出るとさらに休日を増やし、忙しい場合に振り替える。同社の労働組合とも合意した労働条件という。オーダーシャツの条件の第一に納期厳守を挙げる阪本社長は、「働く人は大変だが、オーダーで生き残っていくにはこういう仕組みを作らないとコストも下がらないし納期対応も出来ない」と語る。
フルオーダーシャツに取り組んだ最初の3年間は大幅な赤字だったが、こうした体制作りが実を結び、4年目に黒字転換し、「昨年からは新しい仕組みが見事にはまって年間フル操業」になったという。
設備更新へ、まず「9000B」
良いミシンでジャパン・クオリティ
信州工場は国内のシャツ工場として先端を走り、かつて既製品を生産していた時期は国内外の大型自動機がずらりと揃っていた。しかし、オーダーシャツ工場に切り替わった今では前工程でCAD/CAMを駆使しているものの、縫製現場では自動機はほとんど見当たらず、本縫い、穴かがり、ボタン付けのミシンを重視する。
5年前に80人で再スタートを切った同工場は、フルオーダーシャツが本格化するにつれて40人増員し現体制になった。当初はCHOYAグループの閉鎖した工場の設備を有効活用してきたが、それも限度があり、オーダーシャツが軌道に乗ってきたのを機に、設備更新をすることになった。もともとミシンは「JUKIオンリー」というほどの信頼関係があったが、購入に当たってはオペレーターが使いやすい、品質が安定している、メンテナンスがしやすい--を機種選定の基準とし、9000Bはまさにそれにマッチしたミシンということから一気に5台を設備した。
阪本社長は1973年にCHOYAに入社以来、ずっと生産畑を歩き、04年4月から高山CHOYAソーイング社長を務めている。9000Bも取材前日に自分で試してみたそうで、「軽くて良い感触だった。うたい文句の糸切りも早い」との感想。「良い設備を使ってジャパン・クオリティを作り出し、お客様に良い商品を提供するというのが私の基本的な考え方で、良いミシンがあれば積極的に導入していきたい」とし、今後も計画的に設備更新していく予定で、次は穴かがりミシンを検討中。
信州工場ではこの間のリストラで高齢化が進んだこともあって、あらためて若手社員や高校新卒者の採用に取り組みだしており、中国人研修生を活用しながら全体のパワーを維持していく方針。同時に技術継承やレベルアップのためにシャツ縫製の技能検定にも積極的に挑戦していく。現在、同工場では一級2人、二級24人がいるが、来年は一級に2人、二級に8人が受験することになっている。
また、受注の安定化のために工場提案にも力を入れている。その一つとしてハンドステッチが出来るように新しい設備も取り入れた。このほか高山CHOYAソーイングではエコオーダーシャツを自社開発して販売しているが、高山グループとしてこのほかにもレディス向けのオーダーブラウス、ヤング向けのスリムなシルエットのシャツなども拡大していくことにしている。海外生産の移転が進んだ中で、国内工場のあり方を示す一例と言えよう。
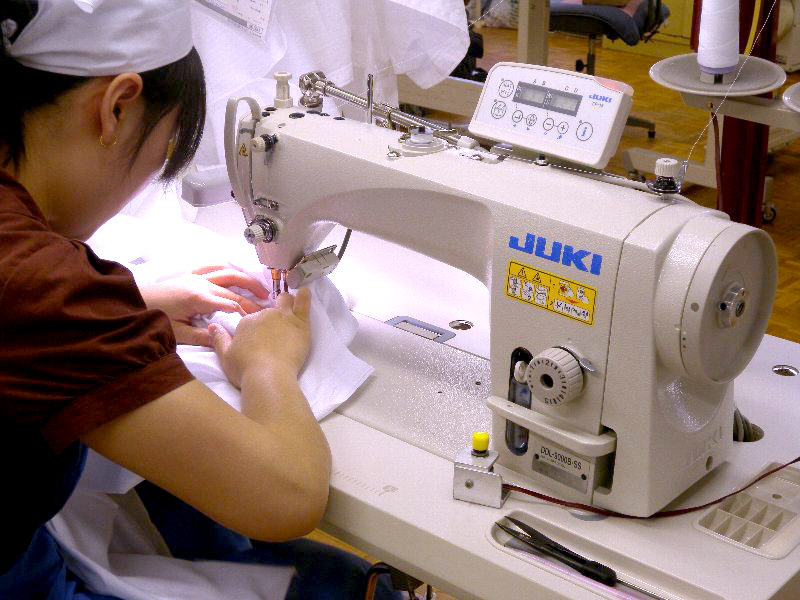
4月に設備した「DDL-9000B」5台はオペレーターからも好評
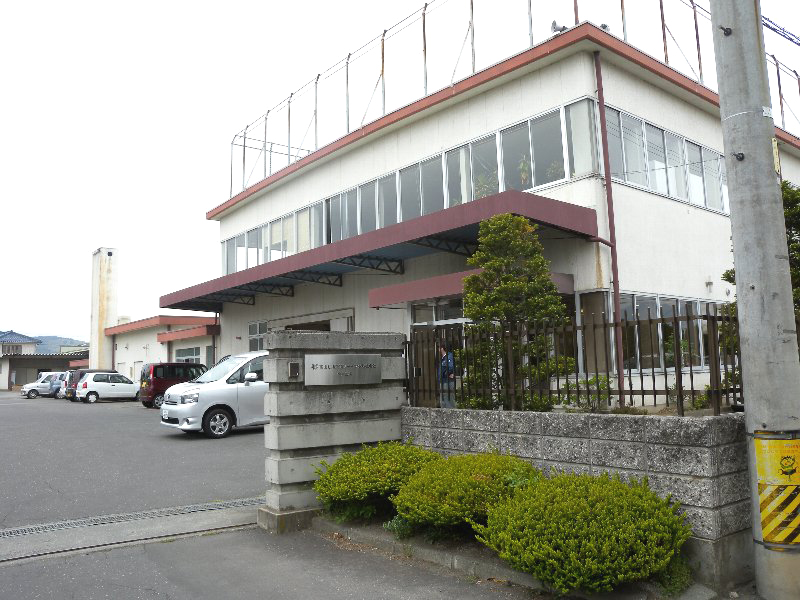
フルオーダーシャツの生産が軌道に乗った信州工場
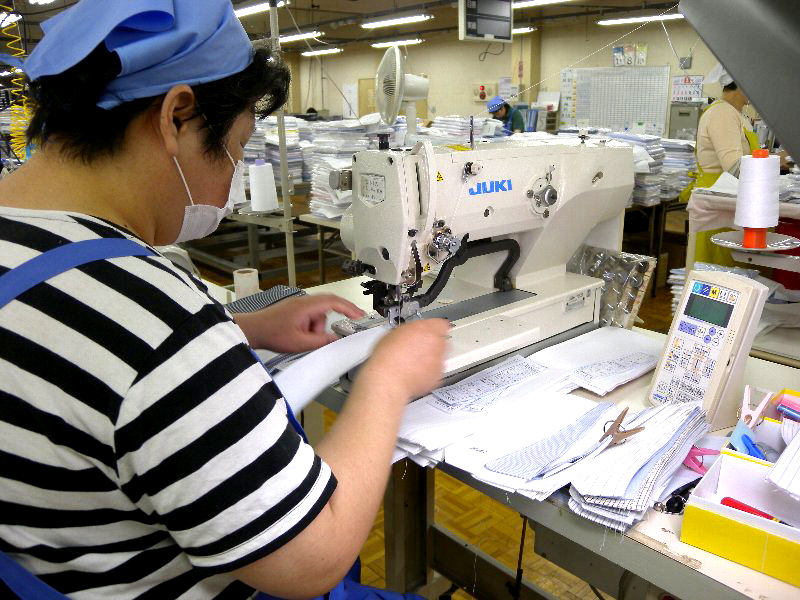
カフスラインで活躍している高速電子眠り穴かがりミシン「LBH-1790S」
JUKIから「この一台」
ダイレクトドライブ高速本縫い自動糸切りミシン
「DDL-9000B」
「お客様の声」を仕様に反映
DDL-9000シリーズはJUKIの一本針本縫いミシンの最高峰モデルです。視認性の良い小さくスリムな面部と、縫製品の取り回しが容易なハイロングデザインで、優れた縫い品質と共に、使い勝手の良さが特徴です。
新製品のDDL-9000Bは、この使い勝手の良さに加えて、糸切り高速化によるレスポンス向上によって作業のストレスフリーをはかりました。これは作業のリズムが生産性に影響するというお客様の声から生まれた仕様です。さらに各機構を徹底的に見直しし、低騒音、低振動、低発熱を実現、オペレーターに優しいミシンに仕上がっています。
操作パネルは、必要最小限の機能を持つCP-18とより多くの機能を持つCP-180を設定し、生産支援機能など新たな機能も搭載しました。より幅広くお客様のニーズにお応えできる仕様となっています。
また、新開発のサーボモーターや効率化設計によって業界ナンバー・1の省エネを実現すると共に、部品点数削減・製品質量削減などによってよりいっそう環境に優しいミシンになりました。効率化設計や部品点数削減は、信頼性や製品寿命の向上につながり、従来機以上に末永く安心してお使いいただけると確信しています。
DDL-9000Bは早期の市場導入を目指し、特別プロジェクトを組んで開発しました。短期開発の中、目指す目標が高く、何度となく辛い局面もありました。しかし、全社一丸となって取り組みすべての課題を克服し、お客様の元にお届けすることが出来ました。
発売以来、多くのお客様にご購入いただき、非常にうれしい思いとともに、今後もお客様の声をたくさんお聞きし、さらにお客様の求める製品に近づけるべく取り組んでいきます。
【コメント】DDL-9000Bプロダクトマネージメントチーム(PMT)