次世代のモノ作りに挑戦 第4回
有限会社サッシュ弘前 代表取締役 長尾 次仁氏
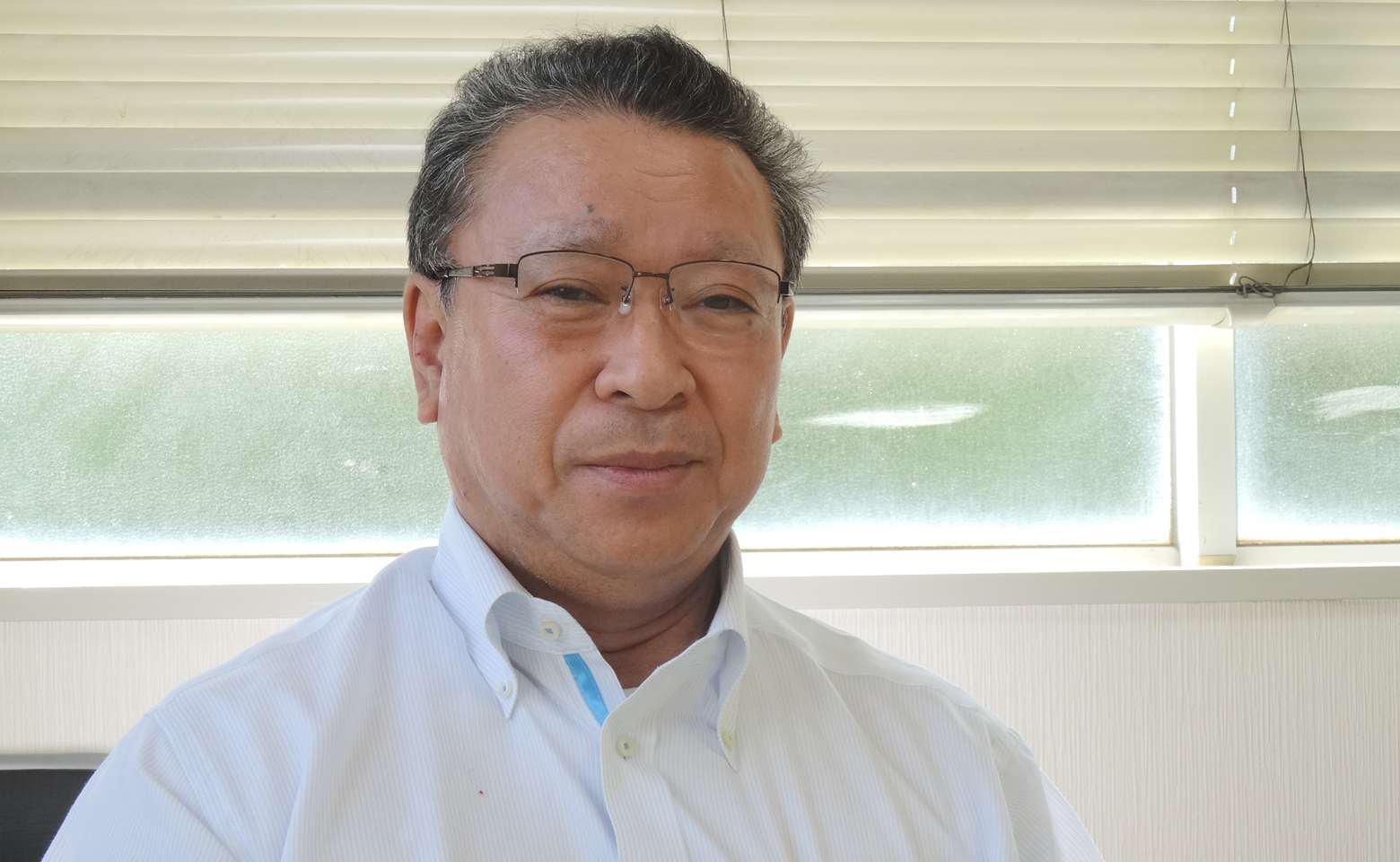
サッシュ弘前(青森県弘前市神田4丁目6番地2)は、レディスのパンツ・スカートを生産するボトム専門工場。人手不足が深刻化する中、「女性が働きやすい工場」を目指して独自の労働条件を取り入れ、若手を増やしてきました。次代を見据え、3、4年前から工場環境の改善や設備更新などを進め、JUKIのフルデジタル仕様・ダイレクトドライブ高速本縫い自動糸切りソーイングシステム「DDL-9000CFMS」も3台導入されています。長尾次仁社長に現状や今後について、古川(こがわ)正樹工場長にDDL-9000CFMSの効果などをお聞きしました。
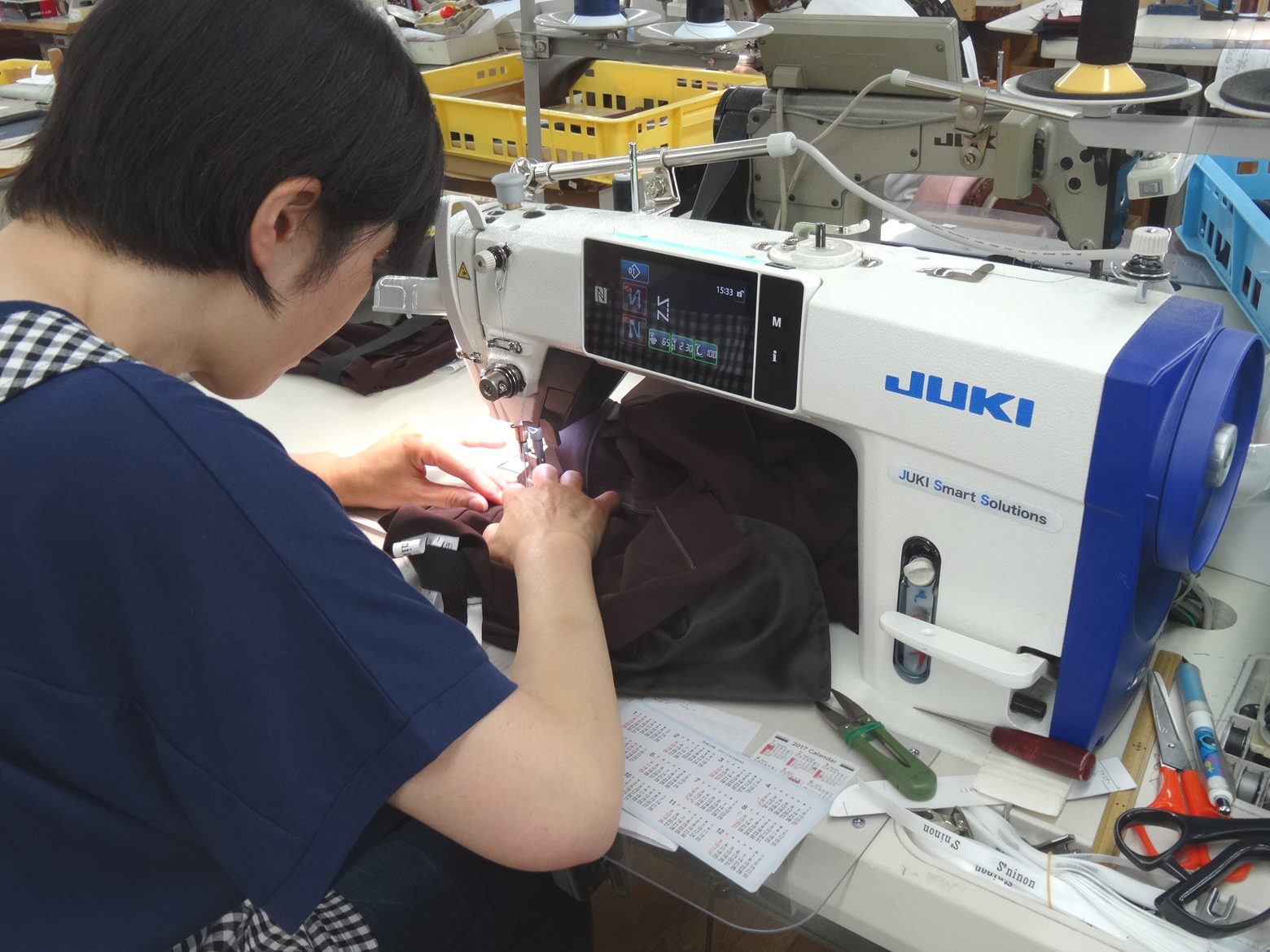
昨年11月に3台のフルデジタル本縫いミシンを導入
女性が働きやすい環境作りを目指す
ーはじめに現状をお聞かせください。
当社の前身はアンデス縫製が1987年に設けたアルファーソーイングで、2005年3月に同社の業務を引き継いでサッシュ弘前がスタート、私は2009年4月に社長に就きました。現在、サッシュ弘前が約140人で、企画・設計や仕上げプレスなどのグループ会社を含めて全体で約170人。このうちパートの短時間労働者が40~50人います。また外国人実習生を27人受け入れています。縫製現場は2ラインあり、一つが30人のスカートとパンツの混合ラインで日本人だけで構成、もう一つが60人のパンツ専門ラインで実習生が入っています。主力のお客様は4社で月間生産量は1万8千本、スカートがこのうち1千~2千枚です。アルファーソーイング時代からパンツに特化してきたことにより品質や納期管理などで積み上げてきたスキル、ノウハウがあり、取引先から高い信頼を得ていることが国内に残ってこられた一番の要因と考えています。
ーアンデス縫製と言えばインセンティブ方式の工場として知られていました。
インセンティブ方式が生き残れた要因ではありません。インセンティブ方式は工場の中に時間概念を取り入れることであり、つまり時間管理をする。この商品、この工程が何分とか工場長が標準時間を設定し、それを基準にして社員が自分で自分の状態が分かる。一生懸命やっている、頑張っているというような言葉ではなく、数字に裏打ちされているわけです。何の仕事をやって何%達成したかということを管理職が見ているし、私も見ています。それが評価基準の一つになり、3カ月に1回の手当にもはね返るようにしています。
ー労働条件にも独自のやり方を取り入れているそうですね。
今、当社では年間288日稼働し、土曜日休みはありません。ただし、子供が家にいる日曜、祝日は絶対休む。社員は8時10分から16時10分の7時間労働で3カ月ごとの変形労働、パートの短時間労働者は9時10分から15時までの5時間労働なんです。社員は出来る時は16時から1時間残業をするので収入が増える。定時が16時10分だから自分の用事がある時は明るいうちに帰れるのが利点です。実習生も18時10分までの2時間しか残業させません。うちの特徴は、休みが少ない代わりに社員はもちろんパートも有給があり、必要なら有休を消化して休みます。皆さん有給をばんばん消化しており、休みやすい会社にしています。ですから、十数人休んでもそれほど休んでいる気がしません。
ーどうしてそんな仕組みにしているのですか。
かつてうちも他社と同様に年間稼働日数を260日まで落とした結果、売り上げが減少しました。縫製工場のビジネスは縫っていくらですから、縫っている時間が少ないと儲かるわけがない。そのために稼働日数を増やして売り上げを確保する方策を考えました。もちろん労務士と相談し、法律は100%遵守しています。我々の産業は女性が働きやすくしないといけないので、それを徹底しているんです。お腹の大きな人や小さい子供を持つ女性はほかの会社は雇わないが、うちは雇います。だからよそで働けない人が来てくれる入りやすい会社にしています。今も6人が産休に入っているし、20代、30代の人たちが40人近くいます。この人たちが休むことを前提に仕事をしていますから、人数が多くいないとできませんので人を増やしてきました。休むといってもずっと休むのではなく、月に何日とか、子供が病気で休むとかですから、ほかの日に働いてくれればいいんですよ。働く場所を探している彼女たちのニーズはそこにあるんです。そのニーズに応えようと4、5年前からこのやり方に切り替えました。
ー国内工場としての今後の見通しは。
当社の生産キャパは国内生産全体から見ればほんの一部。だから仕事がなくなるのは環境のせいではないと社内では話しています。国内生産も見直されています。先進国のアメリカでも国内に縫製工場があるし、服を作る産業はなくなりません。しっかり考えて経営をしないと難しい時代ですが、この弘前の地で200人規模で生き残っていける環境作りだけはしておきたいと思っています。
フルデジタルをサンプル作成に導入
ーそのために工場環境や設備更新にも取り組んできたそうですが。
会社は次代につなげていかないといけないんです。しかも若い人たちが入ってくるようになりました。それなのに建物は汚いままで、設備投資もしなければその人たちが安心して働けません。この工場は建設して約30年になり老朽化していたので、4、5年掛けてきれいに改装しました。設備もCAD/CAM、延反機、スポンジングを入れ替えたし、JUKIさんの本縫い自動玉縁縫い機「APW」、電子サイクルミシン「AMS」、高速電子単糸環縫い根巻きボタン付けミシン「AMB」などの自動機も新機種に切り替えました。
ーフルデジタルミシンもその一環で導入されたのですね。
昨年のJIAM(国際アパレル機器&繊維産業見本市)や東北アパレル産業機器展で確認し、11月に3台導入しました。現在、工場長とサンプル担当者が活用しています。工場全体でフルデジタルミシンはまだ必要ありませんが、データも取れるのできれいに縫わなければならない工程は徐々にコンピューター化のこうした多機能ミシンになるんでしょうね。
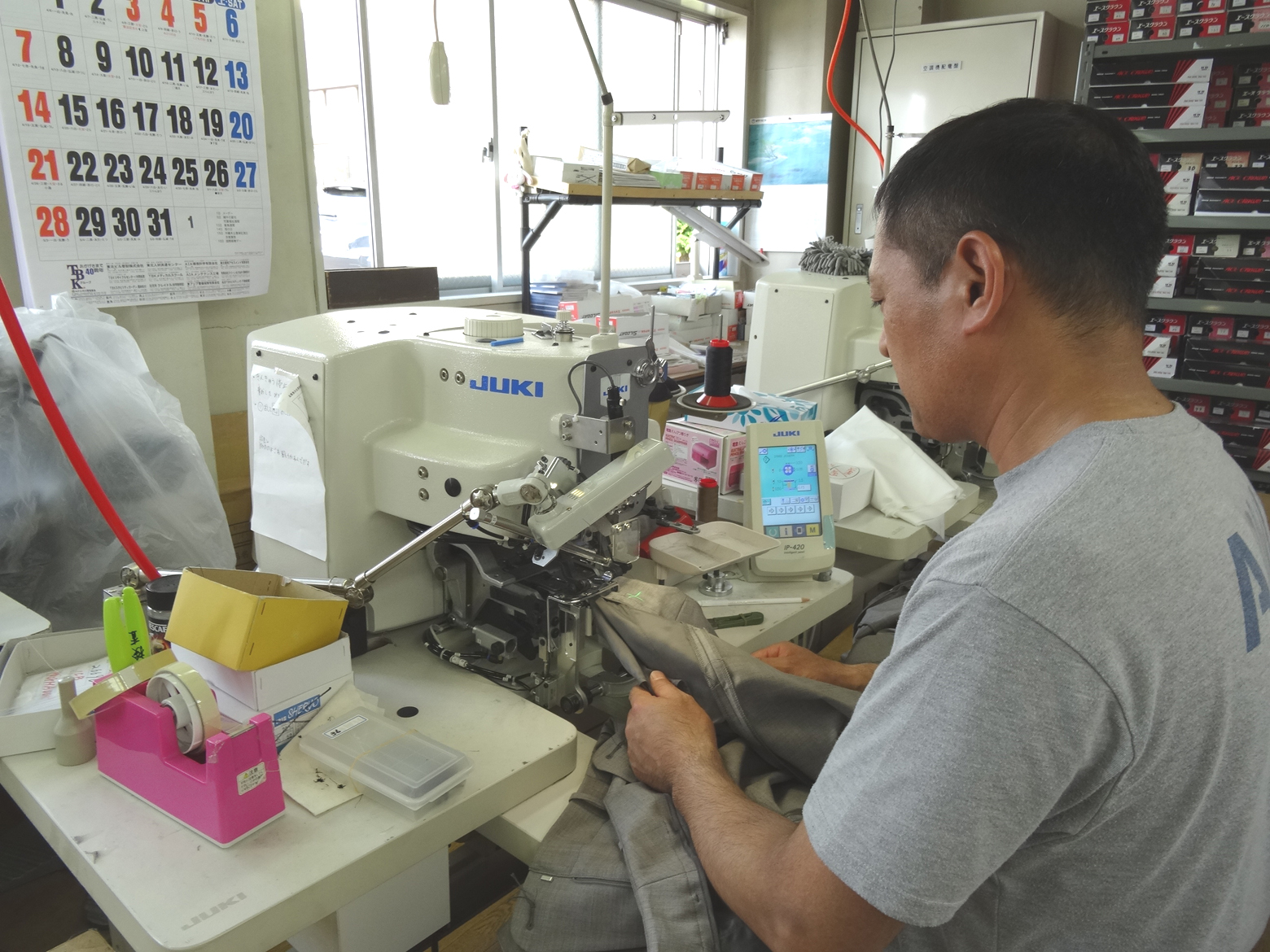
高速電子単糸環縫い根巻きボタン付けミシン「AMB-289」も活躍
段部縫製がきれいに〈古川工場長の話〉
フルデジタルミシンはサンプルメンバーが使っています。送り歯高さや押さえ圧、上糸の張力などがすべて数値化出来るので、この素材の時にはどう対応したかということがメモリーに入れておけます。これまでミシン調整はメンテナンス担当者を呼んで調整してもらっていましたが、もうオペレーターレベルでやれます。今までのミシン調整は一人ひとりがちょっとした加減を感覚的に設定していましたが、それをデジタル化しているので2台目、3台目も同じ設定が可能になります。
当社は百貨店ゾーンの商品を扱っており品質の統一が重要。そのためにミシンも上糸張力、押さえ圧、送り歯の上げ下げの調整が欠かせません。フルデジタルミシンは何と言っても、デジタル制御で押さえ圧をコントロールできるのが利点。段差を乗り越えていく工程を検知し、自動的に押さえ圧を加減するので本当にきれいに縫うことが出来ます。
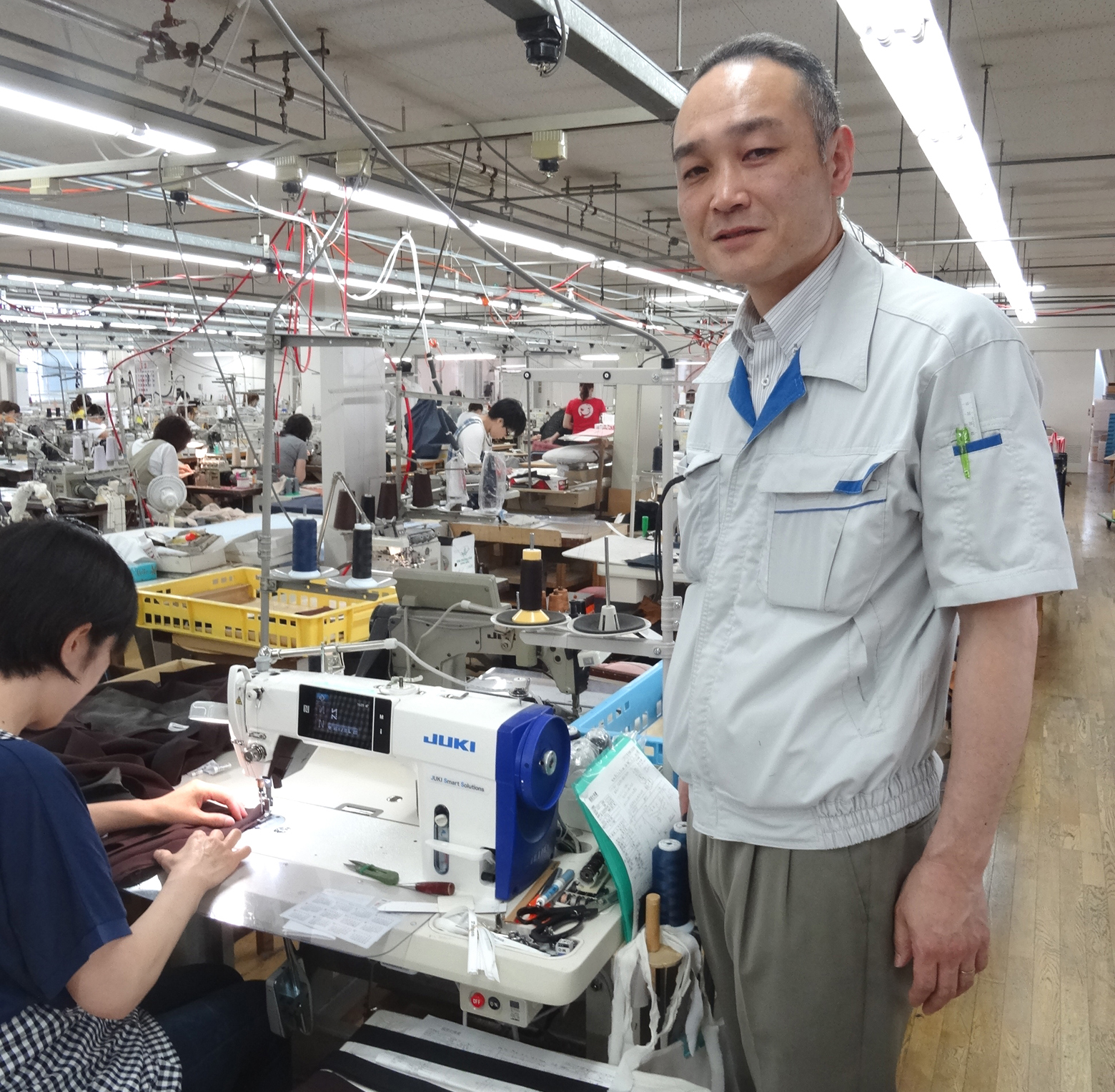
古川工場長