わが社のモノ作り戦略 第6回
光和衣料 代表取締役社長 伴 英一郎氏
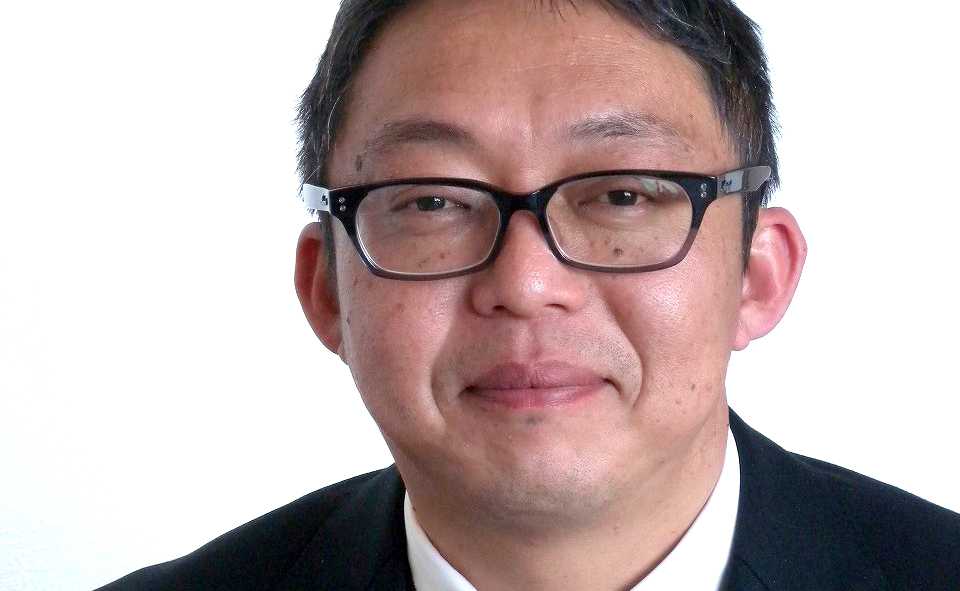
意欲的なトップによる工場改革で成果を上げている企業がある。埼玉県久喜市に本社を置く光和衣料だ。同社はセーラー服をメーンにした女子制服「スクールパール」や男子制服の「スクールロード」のブランドを製造販売しているメーカーで、5年前から伴英一郎社長が先頭に立って5S活動をはじめ、業務改革や現場改善に取り組んできた。それにより取引先からの問い合わせに素早く対応できるシステム構築や、リードタイムを30日から10日に短縮した。同社はメーカーとしての存在感を高めるため工場改革の勢いをさらに強めている。
意欲的に業務・工場改革を実行
ー会社の沿革をお聞かせ下さい。
昭和14(1939)年に祖父が東京の御徒町で創業し、空襲によって埼玉県の菖蒲町に疎開しました。設立は昭和28年で、昭和51年に今の久喜菖蒲工業団地に本社社屋を建設し現在に至っています。創業時は婦人子供服の製造販売でしたが、取引先だった蝶理からの話を受け昭和37、8年に学生服メーカーとしてスタートしました。まだ制服があまり広まっていない時期で、当時社長だった祖父は学校や地元業者の方を集めて説明会を開き、制服を決めていったそうです。私は3代目で、5年前の平成18年9月に父から社長を引き継ぎました。
ー現在の販売については。
女子制服は「スクールパール」ブランドでセーラー服、スカート、スーツ、ボレロ、イートンなど、男子制服は「スクールロード」ブランドでブレザー、パンツなどを販売しています。販売構成は中学校80%、高校20%で女子制服が85%、男子制服が15%の比率、アイテムではセーラー服とスーツがそれぞれ約35%を占め、次がイートン。中でもスクールパールのセーラー服は歴史があって定評を頂いている主力商品です。また、サンリオと提携して「ハローキティ」のセーラー服、イートン、ブレザー、ジャンバースカートを昨年から本格販売しました。織りネームや裏地などにハローキティのブランド名、マークが入った商品で、今春から採用されます。今後はシャツやセーターも計画しています。
ー自社工場をお持ちですが。
本社が営業、工場を含めて90人、それに福島県郡山市に約20人の工場があります。郡山工場は縫製だけで、本社で裁断、仕上げしています。自社生産比率は70%で、100%国内生産です。メーカーとして重視しているのがスピードです。スピードが価格にも反映されるし、学生服で一番大事な納期にも関わってきます。それと技術面では着心地。また、お客様に対しては便利ということがポイントになると思います。便利というのは、例えば価格への対応、問い合わせにすぐに応えられるきめ細かさなど総合的なサービスです。我々は自社工場を持ってモノ作りしている会社ですから、そういった便利さを追求していかなければならないと考えています。
ーそのために社長就任後から業務改革に取り組んでこられたわけですね。
まず改善活動の基本である5S(整理・整頓・清潔・清掃・躾)から始め、次にコンピューター化に取り組みました。その頃は営業が手書きで注文伝票を作成していて、帰社後に書くため対応が後手になってしまうという問題があり、伝票を誰でも起こせるようにしようというのがきっかけでした。そのためパソコンを導入し、市販のパッケージソフトを採用した。このソフトで在庫管理も始め、生産管理にも使うということでどんどんカスタマイズしていったんです。それまで受注した商品がどこまで進行しているかは各部署に問い合わせていたのですが、コンピューターで現在位置を把握し、予定も分かるようになった。このシステム化が一番大きいですね。
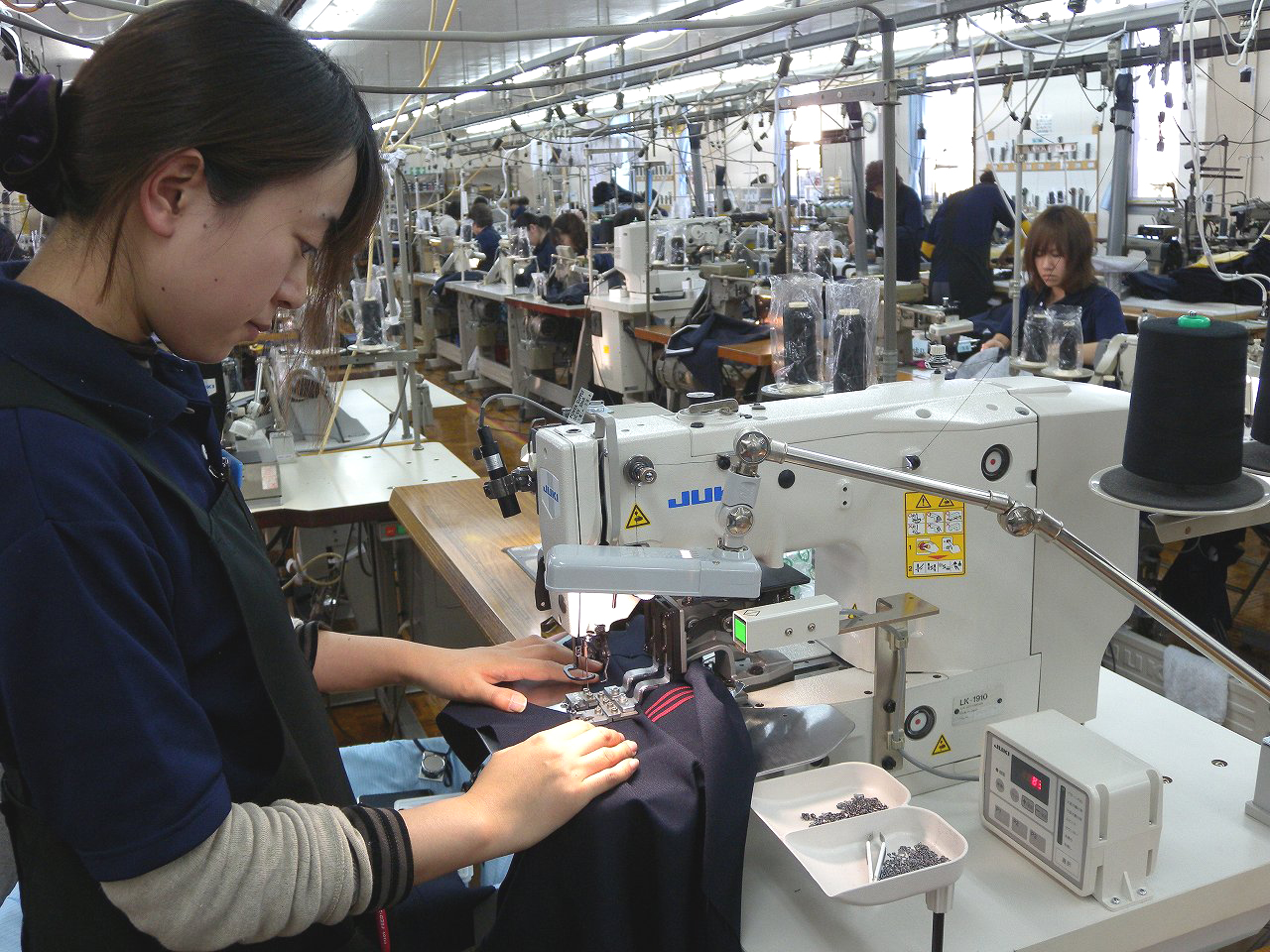
前カン・スナップ付け仕様の高速電子模様閂止めミシン「LK-1910」などを取り入れて内製化を実現
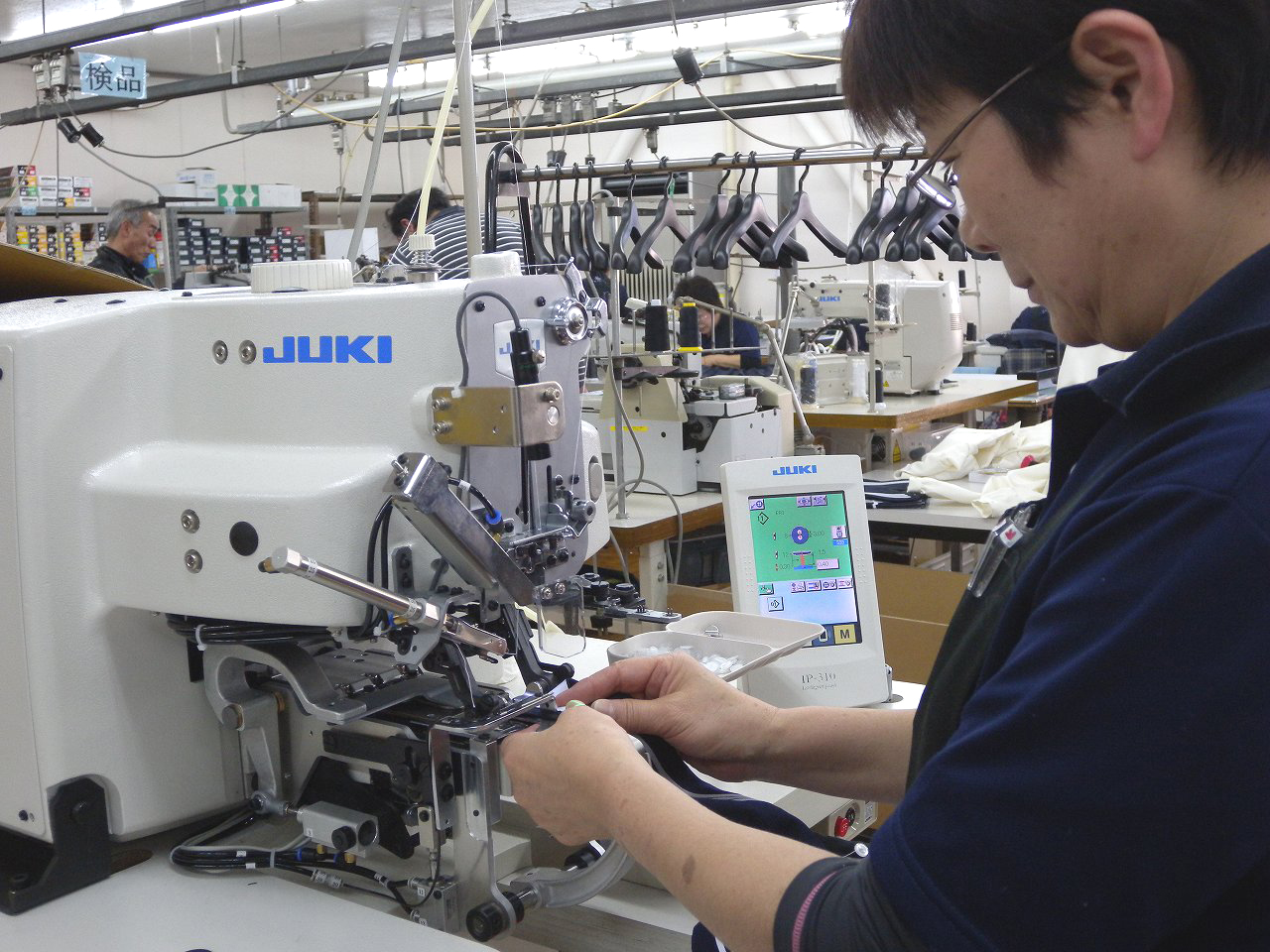
高速電子単糸環縫い根巻きボタン付けミシン「AMB-289」が稼働
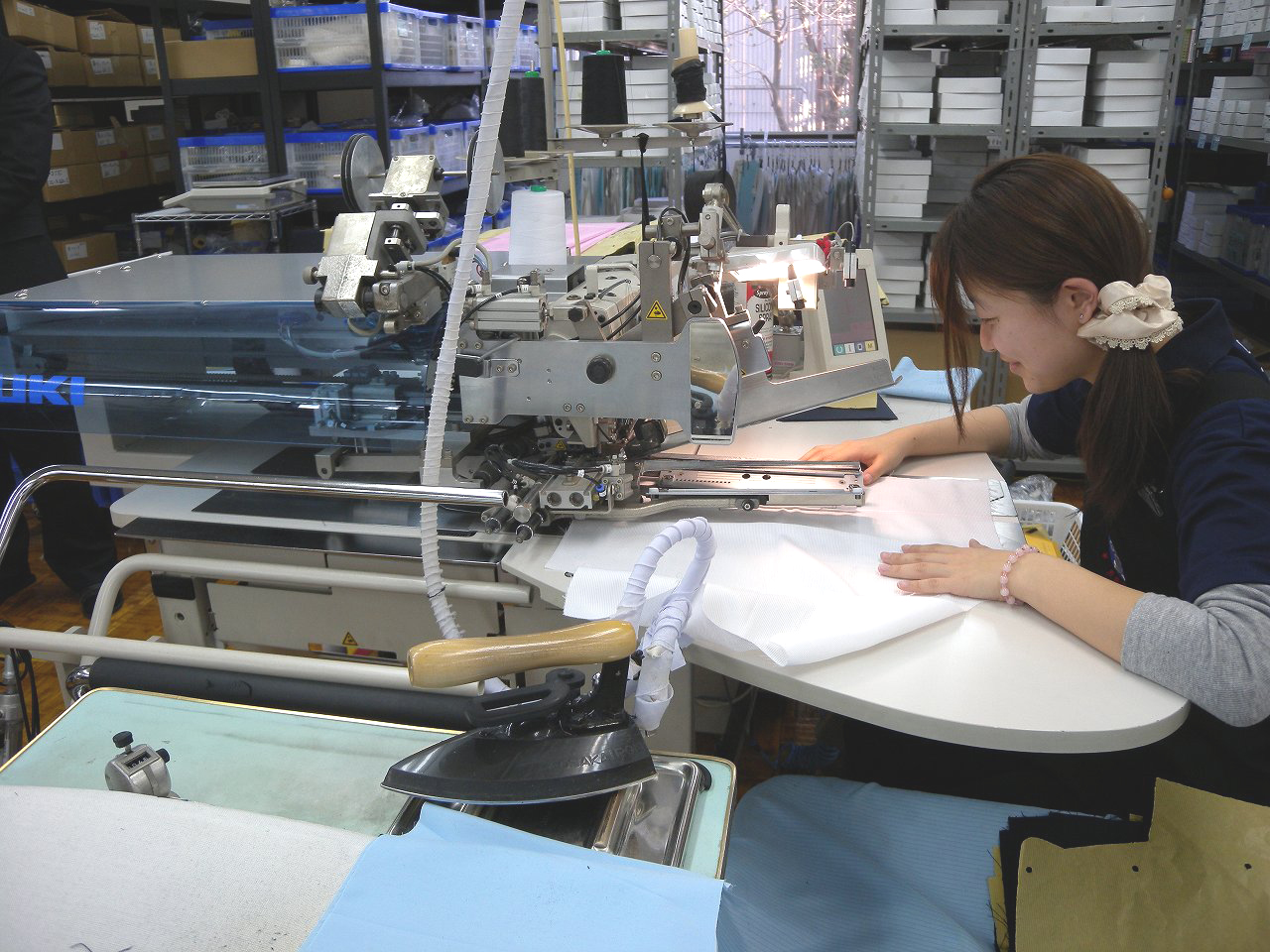
スーツラインに導入している本縫い自動玉縁縫い機「APW-895」
リードタイム短縮を最重点に
ー工場の現場改革も2年前から着手されています。
歴史が長い会社のため、今までこれでやってきたんだというのが最初にありきで、変化への抵抗もあったと思います。モノ作りに対しても手作りの良さ、要するにこだわりが非常に強かったので、機械を導入しながら変えていくのが大変でした。全体的にはリードタイムの短縮を最重点に置いてきました。当時は在庫が現在の倍以上ありましたが、リードタイムが短くなれば在庫が軽減され、資金繰りも楽になりいい回転になる。そのため隣町にあった物流センターを本社に移動した。また、仕掛品も在庫のため、工程内の仕掛りをなくすことが重要です。現場では個々で頑張って生産してきましたが、逆に工程内の仕掛品が増え、手空きのムダが生じる事態も招いていた。そういうムダ取りなど本格的な縫製現場の改革を考えていた時、埼玉県から県の技術アドバイザーに登録されていた、当時JUKI縫製研究所にいた山田昭氏を紹介して頂き、昨年1月から「工場診断」のサポートを受けてきました。
ー「工場診断」を取り入れて改善活動がさらに進んだわけですね。
改善活動としてまず情報を全員が共有化できるようにコンピューターの社内LAN(ローカル・エリア・ネットワーク)も自分たちで引きました。伝票にバーコードが付いているので、作業が終わってバーコードをスキャンするとどこの場所からでも進行状況が分かります。あとは目で見る管理。パソコンを見ることが出来ない人もいますので、今の段取り状況などを早く現場に浸透させるため、目で見て分かる管理ボードを作成したりグラフ化した。また、現場ではそれまでモノが行ったり来たりしていましたが、滞留を起きなくするため流れを一本化した。工場の1階にあった仕上げや梱包を縫製現場のある2階に上げ、副資材も整理して2階に配置した。1階はCAD、裁断、出荷で、2階を縫製から仕上げ、梱包までワンフロアで流す仕組みにし、ライン内仕掛かりも1人3着に減少させています。学生服生産は合格発表から4月の入学式までが"シーズン"と呼ばれる最大の繁忙期ですが、改善効果もあって今は販売日までに納品できる態勢になりました。
ーリードタイム短縮のため内製化も積極的に進めたと聞いています。
手作業でなくては出来ないと思っていた仕事がたくさんありましたが、それを機械化に切り替えました。例えばセーラー服のカギホック付け、袖口のスナップ付け、ボタン付けです。スナップも表に出てはいけない場所がありますが、それは縫製する前に付けてしまえば良いわけです。本来出来るはずが、手作りの良さにこだわり、やってなかった。夏物のセーラーでは襟取り外しというのがあり、我々の中ではかなり多い作業なんです。これも家庭内職を頼っていたので、すべて機械で付けてしまうことにした。いずれも縫製後の手作業でしたから、最後の工程にならないように縫製方法を変え、JUKIのミシンを取り入れ機械化したわけです。まだ1年半くらいですが、ほとんどマトメ工程がなくなってリードタイムが短縮し、家庭内職を回る担当も不要になりました。
ー意欲的な工場改革ですね。
変わってないと企業はダメで、変わってないと何か取り残された感じです。これまでの現場改善には失敗も多いんですが、やってみないと分からないので、とりあえず出来ることはすぐに着手しています。今はICチップを使った生産管理の実験を始めています。これは縫製の一人ひとりの受け持ち時間をICチップで計測し、バランス状況をリアルタイムで把握する。それでネック工程があればすぐ応援させたり工程編成を変え、出来るだけ平準化した流れを作るのが目的です。主力のセーラー服ラインの組み立て工程で開始したばかりですが、成功すればかなり社員の負荷が軽減し生産性が上がると見ています。工場の改善は効果が大きく、楽しいですね。業務改善で計画しているのはお客様からの電話による問い合わせ対応で、システムと連動して電話のお客様の受注内容をすぐ画面に表示できるようにしようと考えています。問い合わせに素早く応えることがお客様満足度の向上に繋がります。
学生服メーカーの存在感発揮
ー今後の学生服業界の見通しは。
よく言われるように少子化による生徒数の減少、お下がり着用など厳しい環境にありますが、見方を変えると子供はいなくなりませんし、一般アパレルに比べて制服はリピート率が高い業界です。しかも国内でしかできない業態で、我々が生き残るチャンスが存在します。国内縫製は減少の一途ですが、学校や生徒さんたちは皆さんオリジナルの制服を作りたいという要望を強く持たれています。ですからお客様と話し合いの出来る身近なメーカーとして、便利に使って頂ける会社を目指していきたいと思っています。
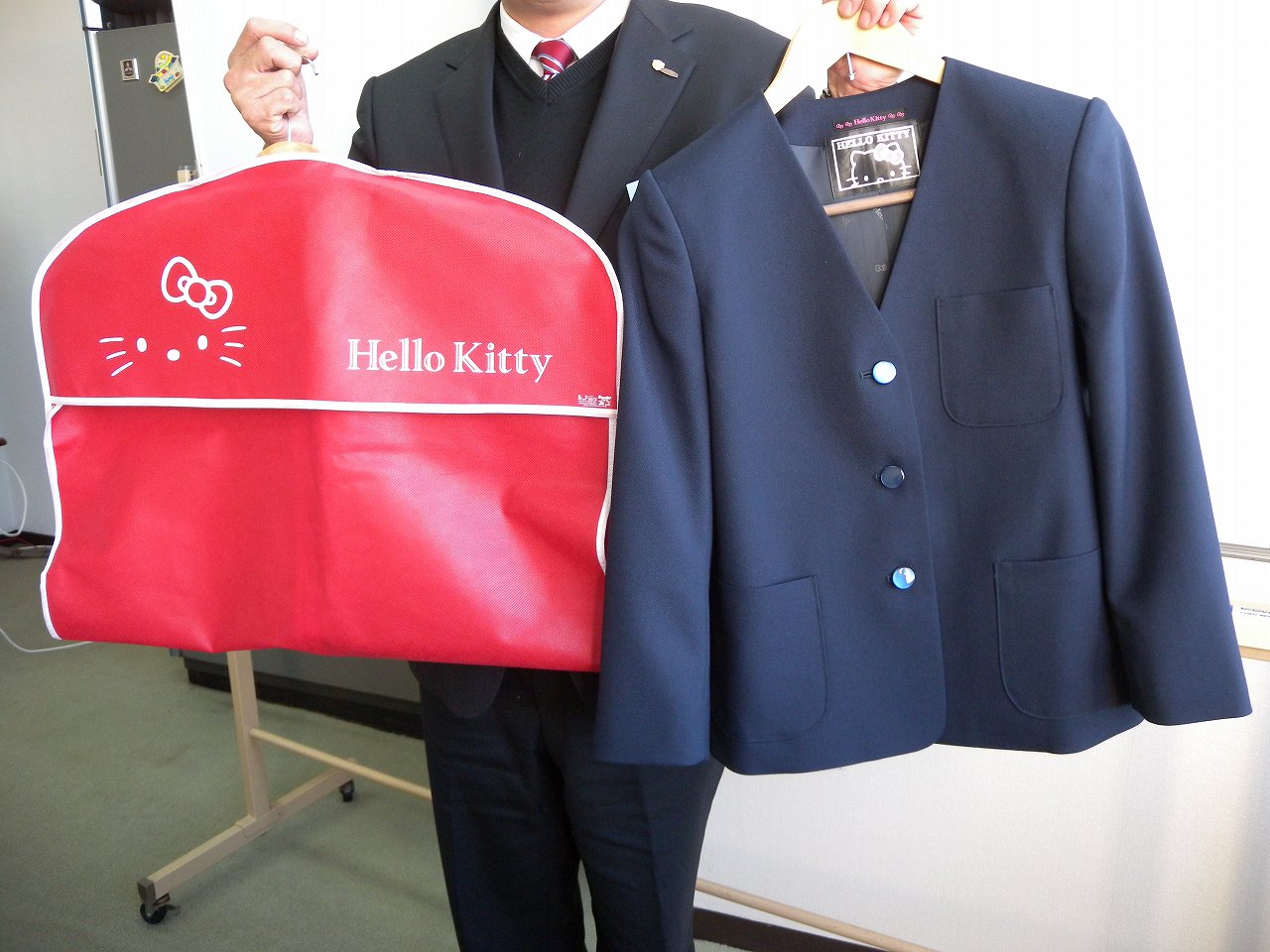
「ハローキティ」の女子制服
JUKIは世界のアパレル生産を全力でサポートします
縫製研究所のカスタマーサポート「工場診断」
すでに5,000回以上の実績
JUKIの縫製研究所は、国内外のカスタマサポートとして「工場診断」に取り組んでいます。アパレル生産企業の生産諸問題に的確にご指導していることで高い評価を頂き、すでに5,000回以上のコンサルタント実績を持っています。
お客様からの工場診断依頼には、「管理職の能力を強化したい」「従業員の意欲を高める目標設定がしたい」「生産方式を見直したい」「標準時間を設定したい」「計数管理が出来る体制を作りたい」「仕掛かり期間を短縮したい」などの理由があります。こうしたご要望に対応するため工場診断では「生産管理コンサルティング」と「生産システム導入指導」を柱にしています。
生産管理コンサルティングは、直接工場にお伺いして現状を調査分析し、生産性向上のための適切なアドバイスを行います。お客様のニーズに合わせて対応します。
生産システム導入指導は、企業の要請に基づき、生産条件(生産アイテム、ロット数)に即した最適な生産システムを提案します。最初に現場で一つひとつの工程を調査。アイテムの全工程と時間値の把握、オペレーターの詳細な行動分析、物の流れの指標となるレイアウトなど現状の分析を実施し、問題点発見の足掛りとします。そして現状調査報告及び問題点の指摘や改善の提案を、視覚的にわかりやすく写真や動画を用いて報告します。
工場診断のポイントは次のようなポイントがあります。
- 稼働分析=一日の仕事の中で、実際に稼働している比率、ミシンが回っている比率、身頃の取り置きの比率など、効率的な生産を行うためのライン体質の改善に向けた調査分析をします。
- 工程分析=服一着をつくる過程で、どのような工程があるか。材料や部品、物作りの流れを合理的に改善できないか。使用する設備、アタッチメントは適切か。工程分析表を作り検討します。
- 動作研究=動作の中にムダはないか、順序は適正か、作業配置は合理的かなどを検討。加工時間の基礎となる"動作"に着目して、生産の合理化を検討します。
- 時間研究=ストップウオッチにより加工時間を測定し、一つの工程時間、要素作業時間を求める事で動作研究の裏付けを行い、標準加工時間の資料とします。時間は各オペレーターの作業配分、目標日産枚数算出などの基礎となります。
- 工程編成=流れ生産のための分業区分について各オペレーターの作業配分を検討します。配分状況は編成効率(ラインバランス効率)として表し、ネック工程、あいろ工程の所在を把握しライン管理します。
- レイアウト=導入生産方式に対する機械配置(ミシンレイアウト)をを検討します。運搬・移動、情報伝達の最短距離を原則とし、レイアウト変更の柔軟性、管理の容易性も検討します。
お客様が工場診断をご希望する場合は、JUKIの支店・営業所を経由してお受けしています。
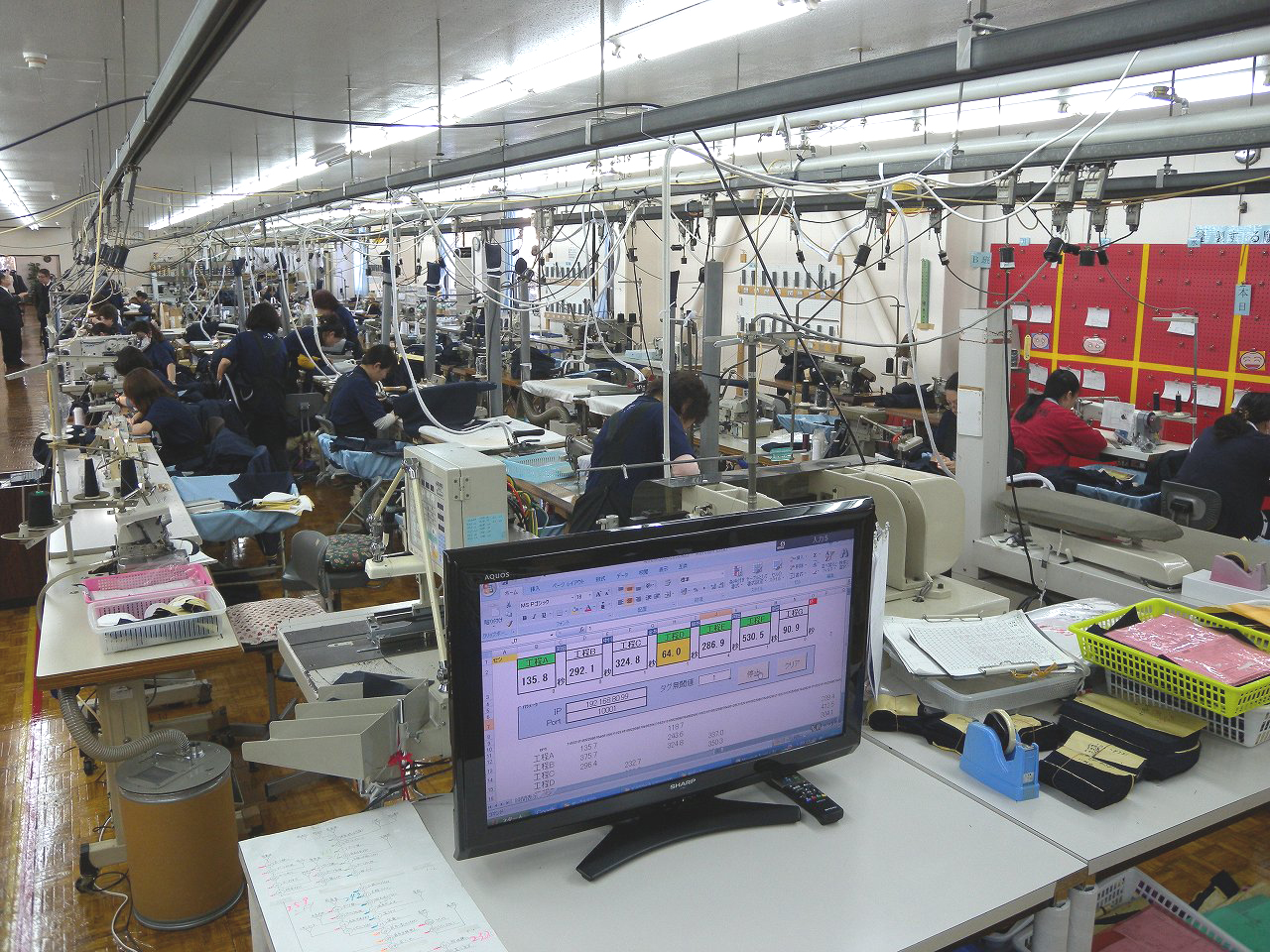
「工場診断」で生産効率も大きく向上した光和衣料