Initiatives in Production
JUKI has four strengths in production: “an integrated production system covering all phases from welding and processing to assembly within the Group,” “sufficient production engineering capability to create unique production systems focused in areas such as digital production,” “a deeply ingrained commitment to ‘improvement’ sustained by long years of intensive QC Circle activities,” and “coordinating capabilities among domestic and international production bases.” JUKI is harnessing those four strengths in its intensifying efforts to evolve manufacturing through DX (Digital Transformation) and GX (Green Transformation).
Initiatives in make JUKI’s factories smarter
Among its digital production systems, JUKI has introduced an assembly process in which each step of the procedure is instructed on a tablet screen, cell-by-cell. This new process stabilizes production by enabling short-term proficiency in work, preventing mis-assembly, and preventing a decrease in line organization efficiency.
JUKI also accelerates the transformation of factories by boosting their productivity with IT solutions such as robotized frame processing, blow-and-removal of chips, advanced coating processes, and automatic transfer between processes.
Initiatives in make JUKI CORPORATION OHTAWARA PLANT smarter
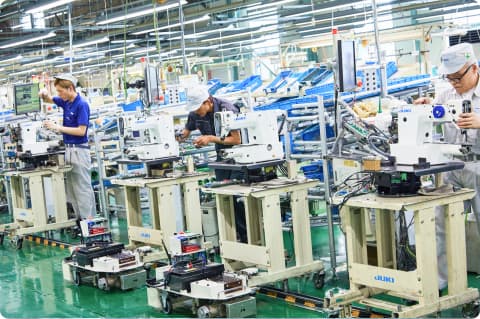
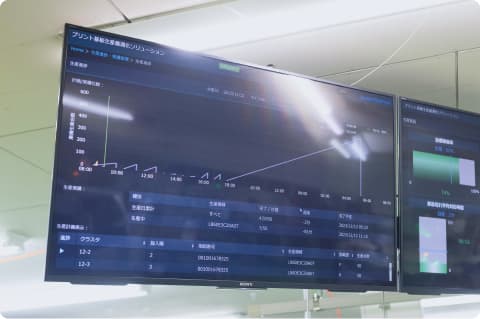
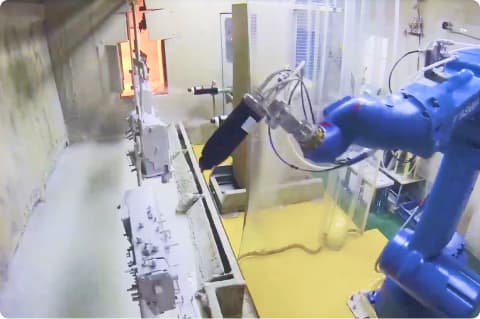
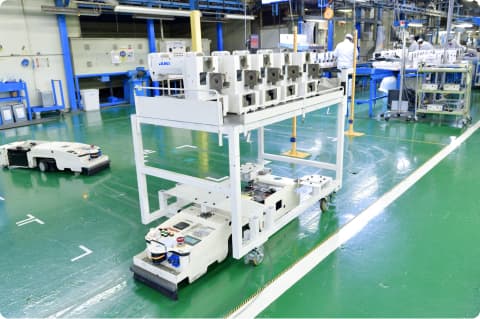
Task-achievement-oriented human resources development
Human resource development forms the basis for manufacturing. JUKI continuously reinforces the core competencies of individuals and organizations as a cultivator of core personnel.
The “skills,” “knowledge,” and “qualifications” required of employees are defined separately for each organization within JUKI. Doing so enables management to visualize the current proficiency levels and to continuously improve employee competence by integrating on-the-job training into daily management, policy management, and committee activities.
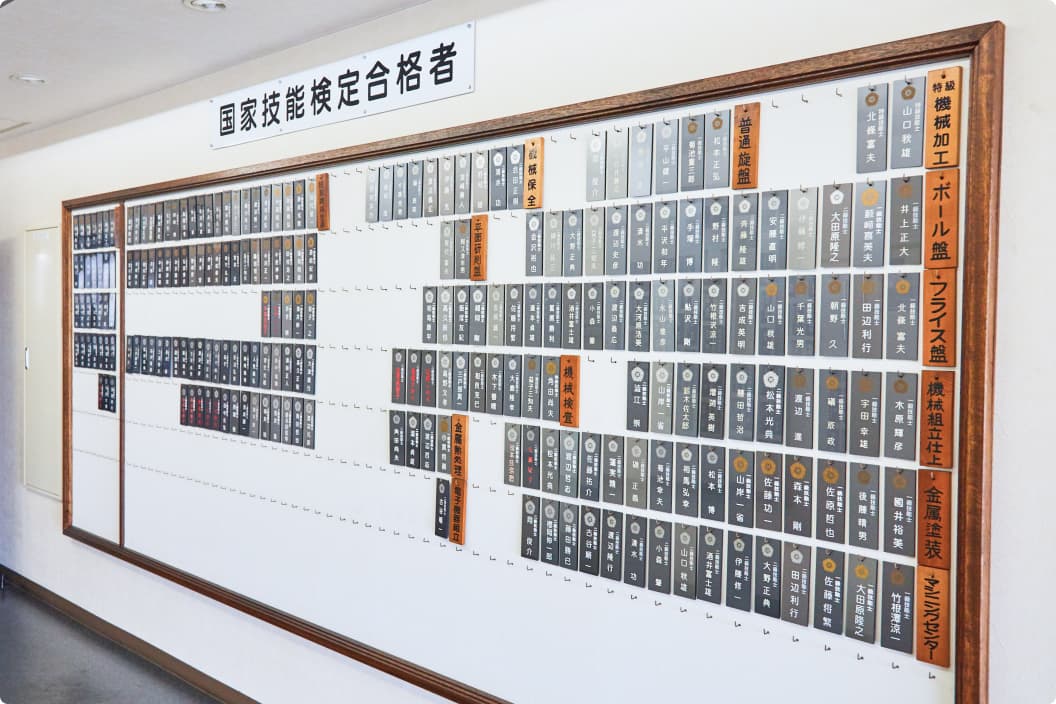
Training of technicians and quality education
JUKI encourages its people to acquire certifications for machine processing, machine drawing, inspection, coating, machinery maintenance, and the like. JUKI also promotes the learning of core techniques essential for product assembly, such as screw-tightening and adhesion and sealing works, by conducting “skill + knowledge” tests twice yearly and granting in-house awards and accreditations.
Meanwhile, the personnel who are expected to one day lead overseas factories receive periodical training. These and other personnel trained in management education support JUKI quality from the ground up.
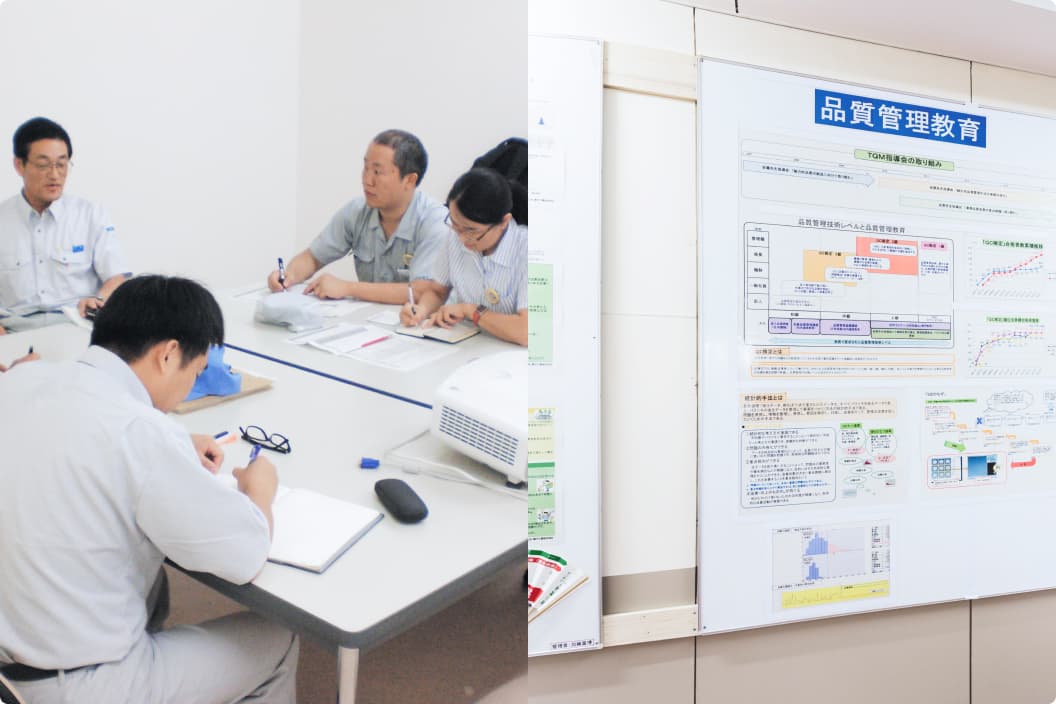
Carbon neutrality
JUKI’s cross-sectional Energy-saving Promotion Team plays a central role in driving JUKI’s progress toward its carbon neutrality targets. JUKI strengthens its environmental load reduction activities by horizontally developing measures focused on the installation of renewable energy, upgrades to high-efficiency equipment, and the adoption of other energy-saving processes.
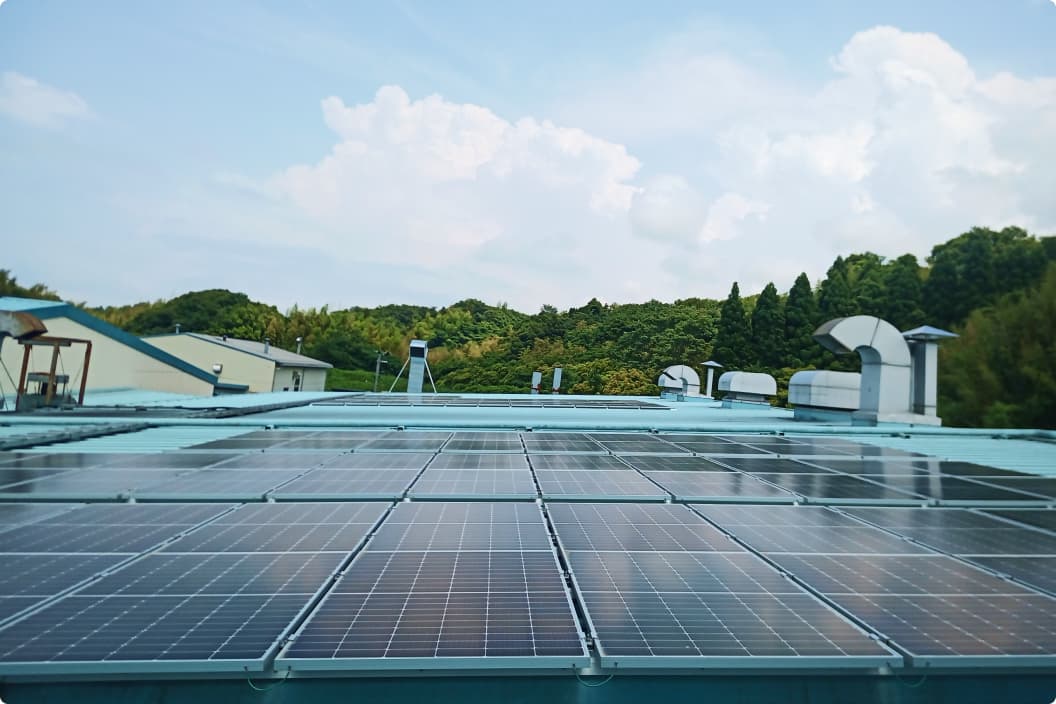
Safety
JUKI promotes safe production through not only daily safety inspections and warnings, but also strengthened education on hazard prediction, the remote monitoring of dangerous operations, and risk assessment with cameras on site.
JUKI is also establishing safe and secure workplaces by robotizing heavy works and works that pose possible risks to the human body, and by equipping its machines with automatic shutdown mechanisms to protect humans when they enter hazardous zones.
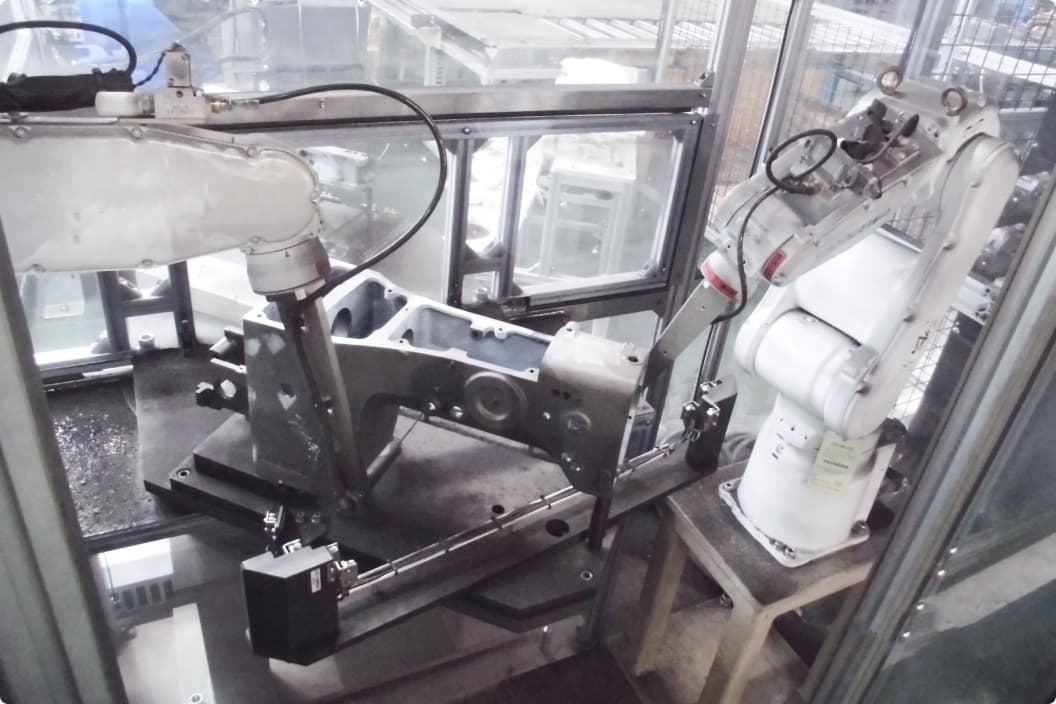