Core Technologies
The core technologies integrated into JUKI products stabilize quality, streamline operability, improve workability, and reduce power consumption.
JUKI accurately captures the ever-more diverse and sophisticated needs of markets to create appealing functions that respond to the demands of global customers.
Introduction of core technologies
Independently driven thread take-up lever
A technology to drive the thread take-up lever mechanism using an independent motor
This technology detects the load on the thread take-up lever during sewing to monitor the thread tension stitch-by-stitch. The technology helps the machine accurately discern between good and bad stitches by visualizing the load on the thread take-up lever when stitching troubles such as stitch skipping and single-yarn threading occur. The data are also fully recorded to ensure traceability.
The independently driven thread take-up lever works with the intermediate presser mechanism to reduce stitch skipping and thread tangling (the formation of so-called bird’s-nests) at the start of sewing.
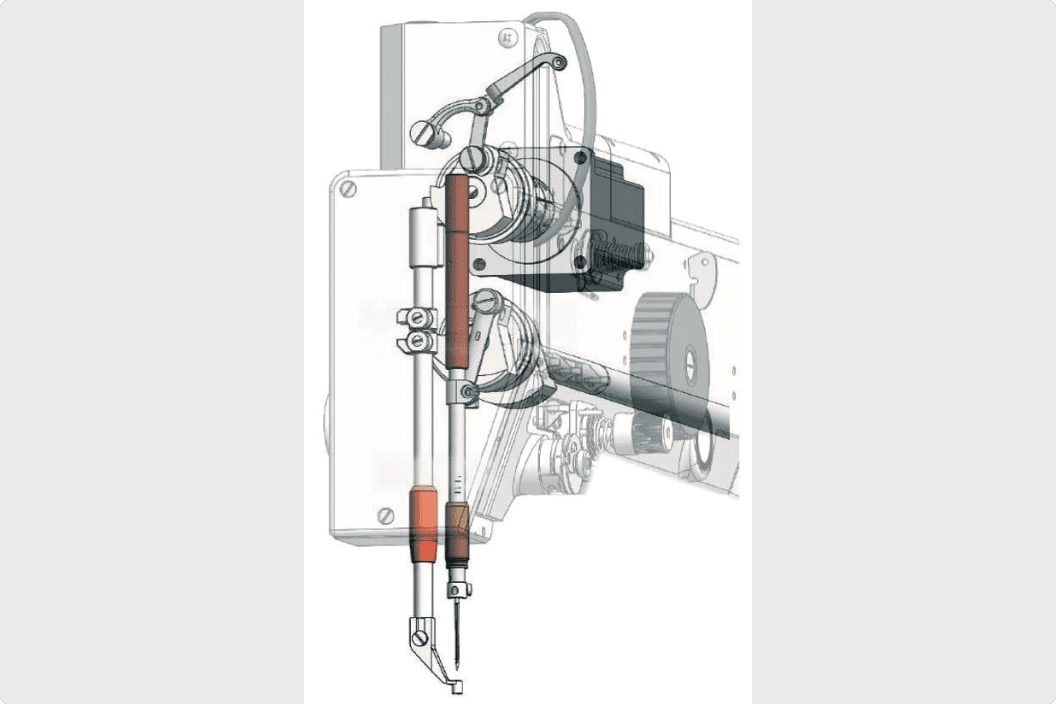
Independently driven intermediate presser foot
Technology to drive the intermediate presser foot mechanism using an independent motor
This technology makes it possible to set the motion of the intermediate presser foot, a mechanism that directly affects the thread tension, as desired. The adjustments enabled by this technology help the sewing machine produce more beautiful and stable seams.
The timing and duration of the clamp onto the fabric by the intermediate presser foot can be digitally adjusted to stop the fabric from rising, improve the stability of needle entry, and reduce stitch-skipping.
When the mode is switched, the thickness of the sewing material can be detected from the motor load.
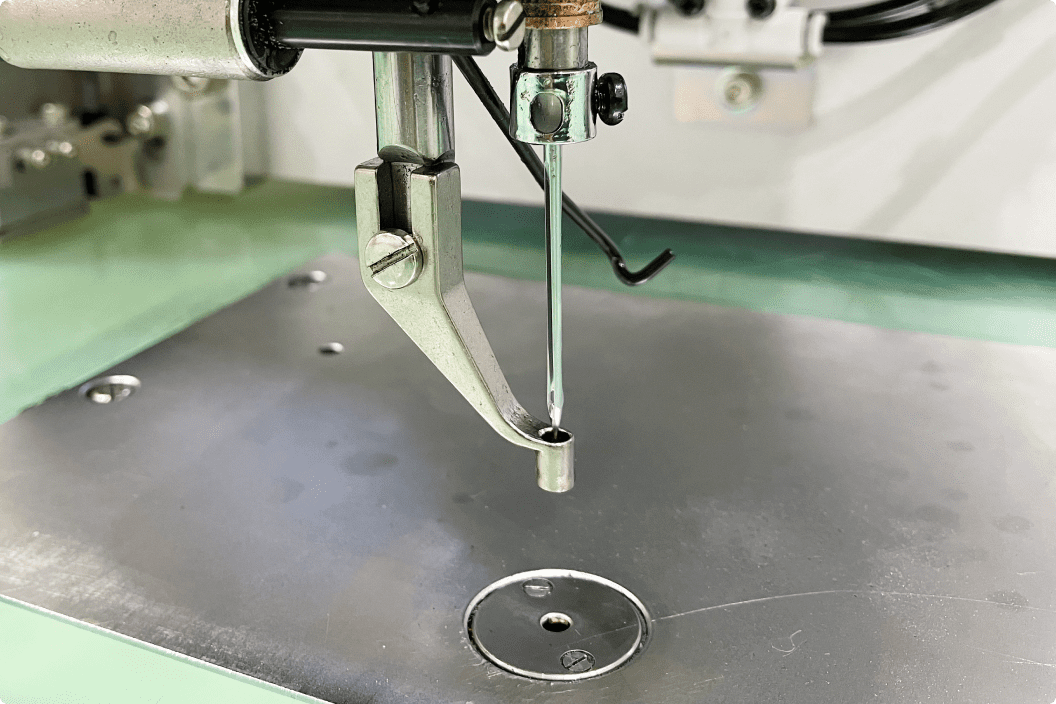
Automatic winding and feeding of the bobbin thread
A technology that feeds the lockstitch machine with a near-infinite supply of bobbin thread
This technology automatically removes the remaining bobbin thread and changes the bobbin (the part that winds the bobbin thread). The following eight steps are executed in sequence to ensure continuous production without the frequent bobbin thread changes experienced with conventional machines: the hook section opens, the carrier arm moves, the bobbin is set, the remaining thread is removed, the thread is unraveled, the thread is wound, the nozzle operates, and the thread is fed.
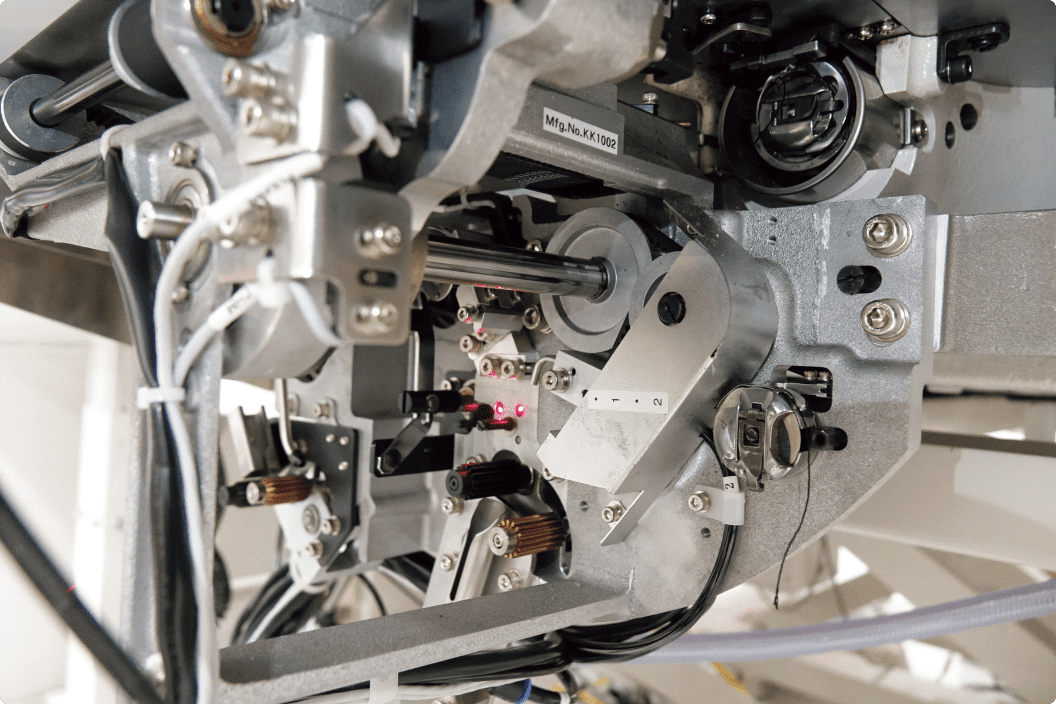
Image processing technology
Image processing to correct deviations between the program data and actual sewing results
This technology enables the sewing of soft and elastic materials such as perforated fabrics while the level of fabric shirring is corrected with a camera. The technology measures the shirring at markers on the fabric, calculates the deviation between the measured data and program data, and makes the needed corrections to keep the stitches at the target positions and output a finished product with no impairments in design.
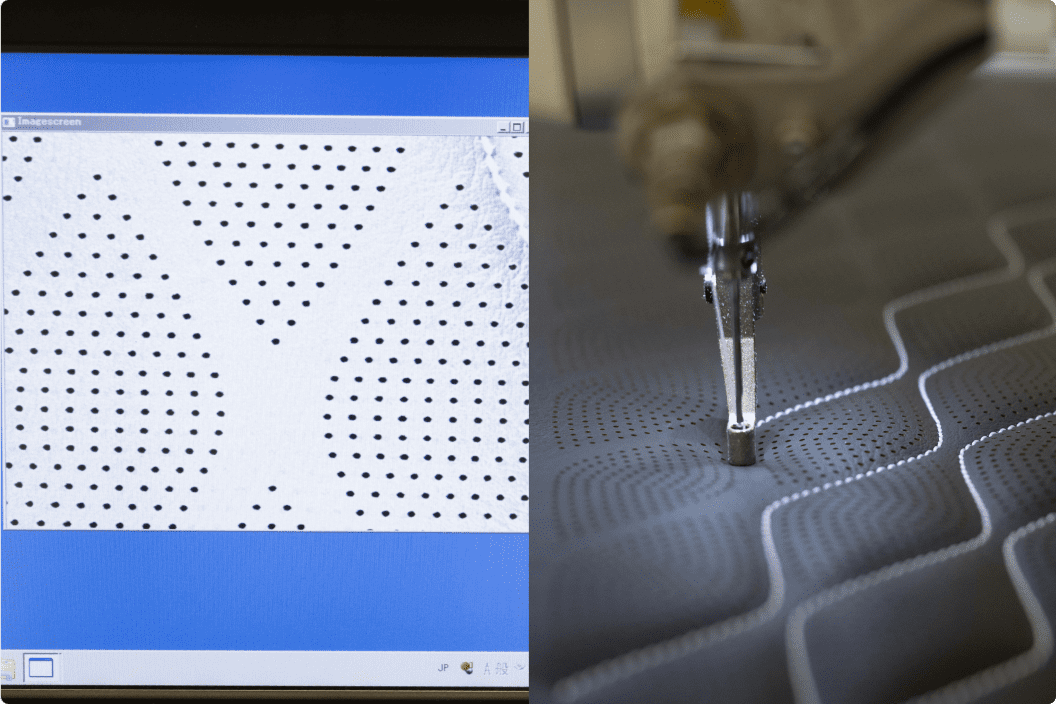
Perfect stitch
Independent vertical drive and synchronous control technology for JUKI’s 1-needle, lockstitch CNC sewing machine
This technology enables the sewing machine to perform perfect stitching regardless of the XY travel direction during sewing. The independent drive mechanism rotates the hook independently from the vertical needle movement, which synchronizes with the XY movement to eliminate hitch stitches and produce well-tensed and beautiful seams with consistently shaped stitches.

Digital control
Digitalized stitch adjustment and data transfer using IoT
This technology digitalizes five stitch adjustment functions (feed dog height, feed pitch, feed locus, presser foot pressure, and needle thread tension) and stores the adjustment data in memory as numerical values. The adjusted data can also be stored on a tablet running dedicated app and wirelessly transferred to other sewing machines simply by holding the tablet over their operation panels (non-contact transfer by Near Field Communication (NFC)).
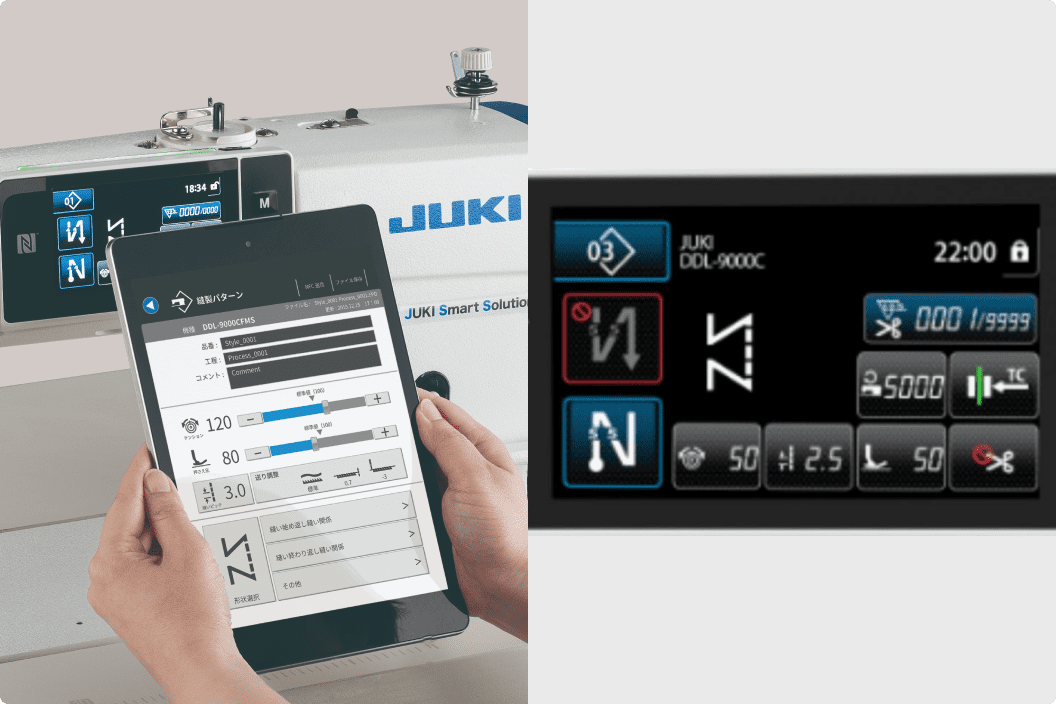
Energy-saving technology
Controlling and optimizing motors to reduce power consumption
This technology optimizes the power consumption of motors using a unique JUKI tuning technique that maximizes engine performance and eliminates waste based on the specific features of the engine. Numerous other energy-saving techniques are deployed in parallel, such as a motor circuit design enabling instant power circuit shutdown when the motor stops and rapid re-start when the motor operation resumes.
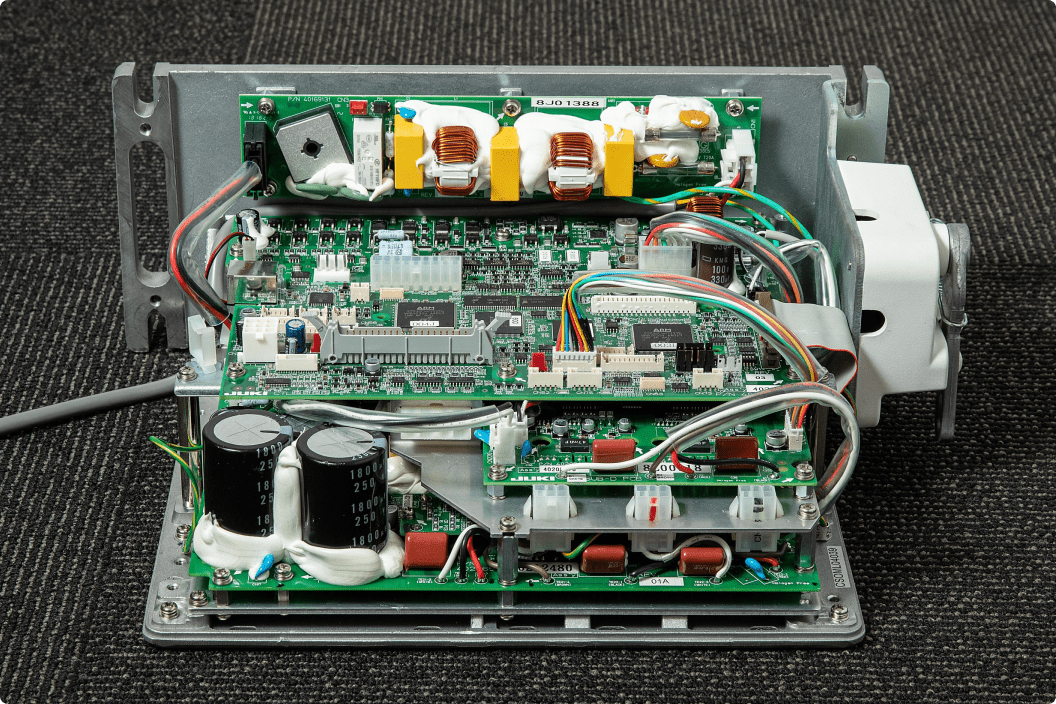
Drying technology
Minimizing the lubricating oil
This technology eliminates oil from the frame by minimizing or reducing the usage of lubricating oil, an essential input for an industrial sewing machine designed to rotate at high speeds. The frame design adopts an original mechanism innovated by JUKI in its pursuit of the optimal lubrication condition for the sewing machine operation. The needle bar is coated with a superhard DLC (diamond-Like Carbon) film to prevent damage and a thin layer of “JUKI Grease” to protect against wear.
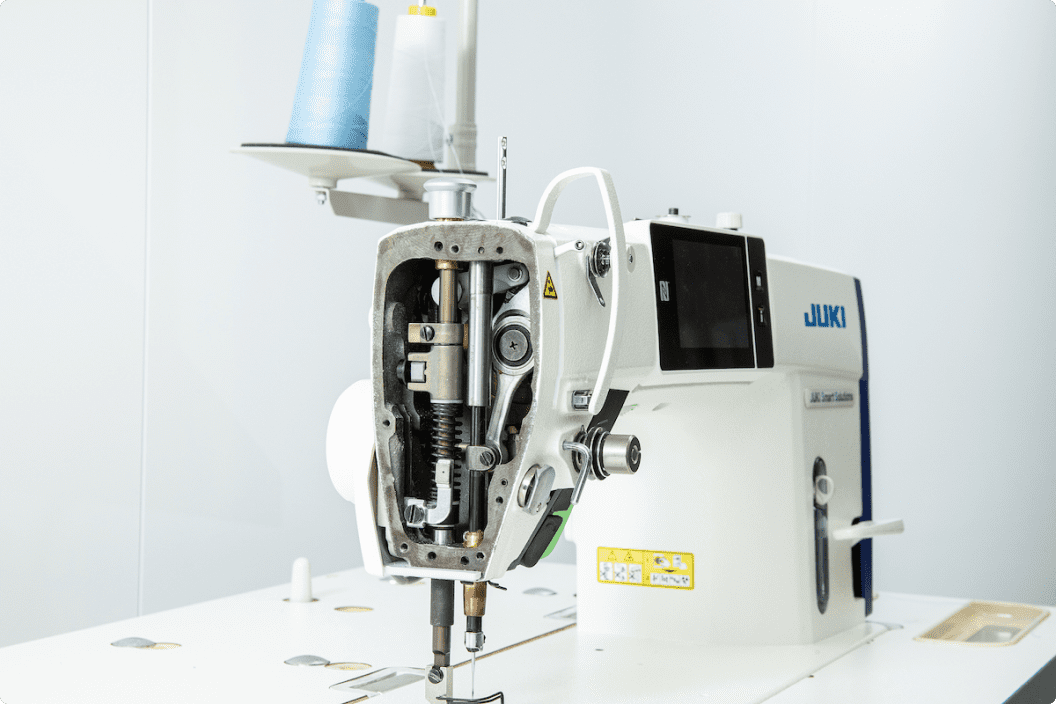
Bird’s nest preventing and shorter-thread remaining technologies
Improving sewing quality on the reverse side of the fabric by eliminating thread picking
This technology prevents thread tangling in at the start of sewing and cuts the thread to the shortest possible length at the end of sewing. The thread-nipping device catches the needle thread at the start of sewing and keeps it firmly in its grip until the end of sewing. After the sewing and the normal thread-trimming operation are completed, the needle and bobbin threads left remaining at the end of sewing and the needle thread left at the beginning of sewing, which is held by the thread-nipping device, are cut short by the knife of the shorter-thread remaining mechanism, and the remaining threads are vacuumed away.
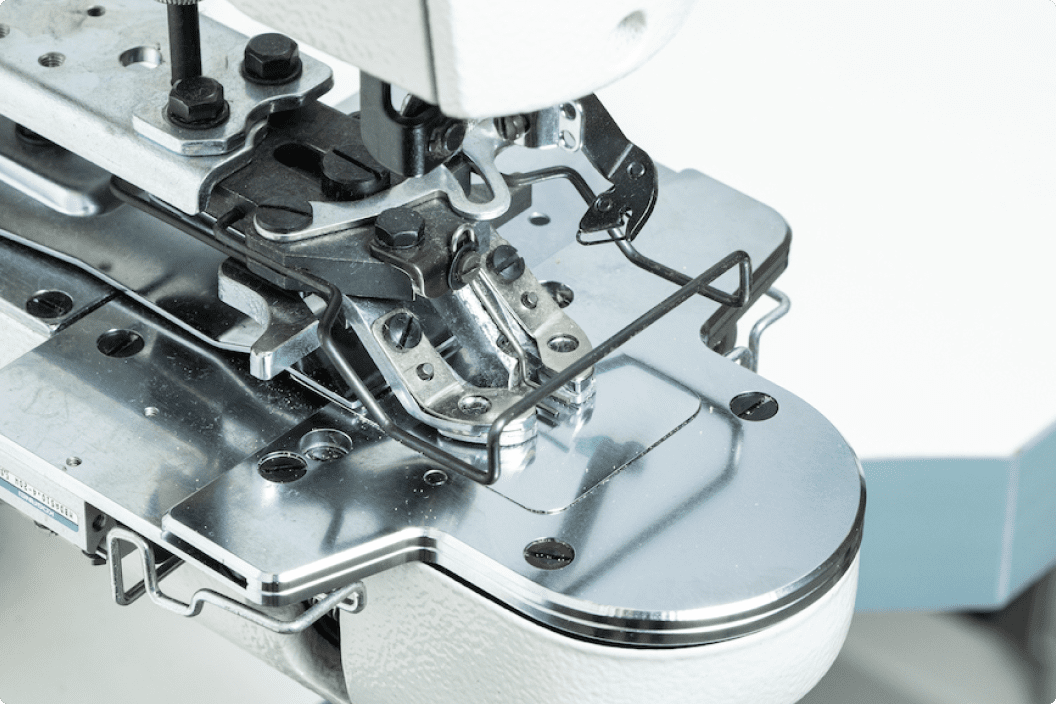
Active tension
Controlling thread tension dynamically to achieve stable “sewing”
This “active tension” technology continuously optimizes the thread tension of the needle and bobbin threads to produce beautifully finished seams. The thread tension best suited to the sewing article is achieved with a mechanism to open/close the tension disk by finely controlling the electric current with a special solenoid. The active tension achieved is used for various purposes, such as thread tension control when the fabric type is changed (e.g., from a heavy-weight to a light-weight or elastic material), the prevention of stitching trouble, or the control of pattern sewing.
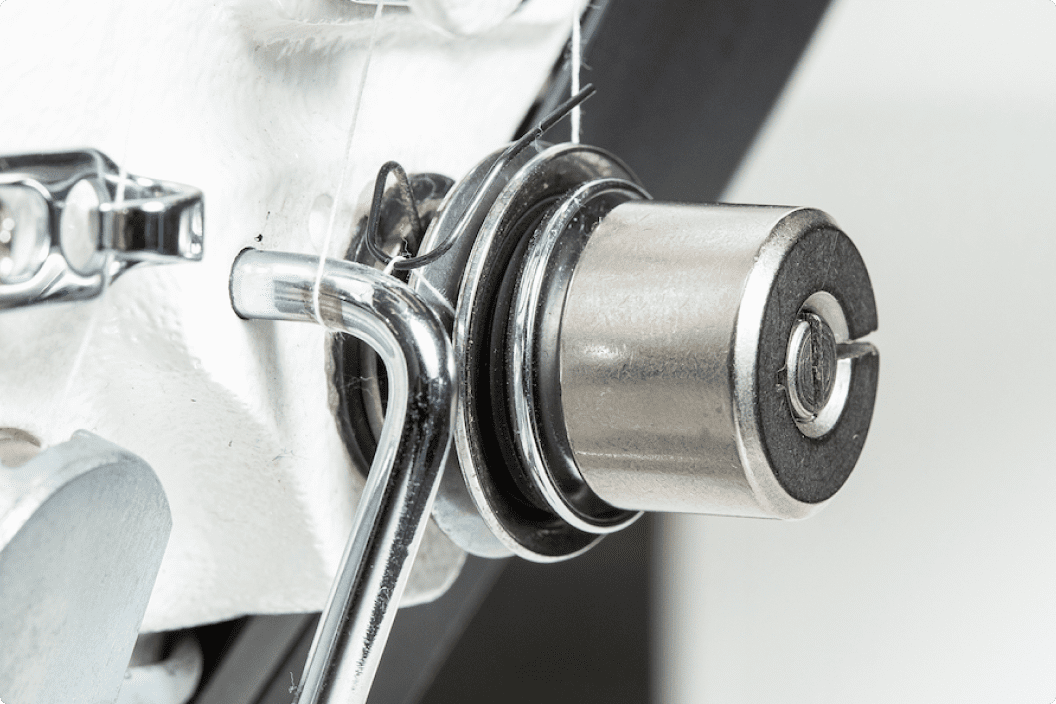
UI/UX Technologies
Easy operation with a highly intuitive, user-friendly panel is achieved.
The “capacitive” type touch panel, the same type used on a smartphone, enables intuitive operation with tap and swipe gestures on the screen.
The easy-to-understand display allows users to quickly reach the desired stitch or operation, with the most frequently used functions grouped together in one place.
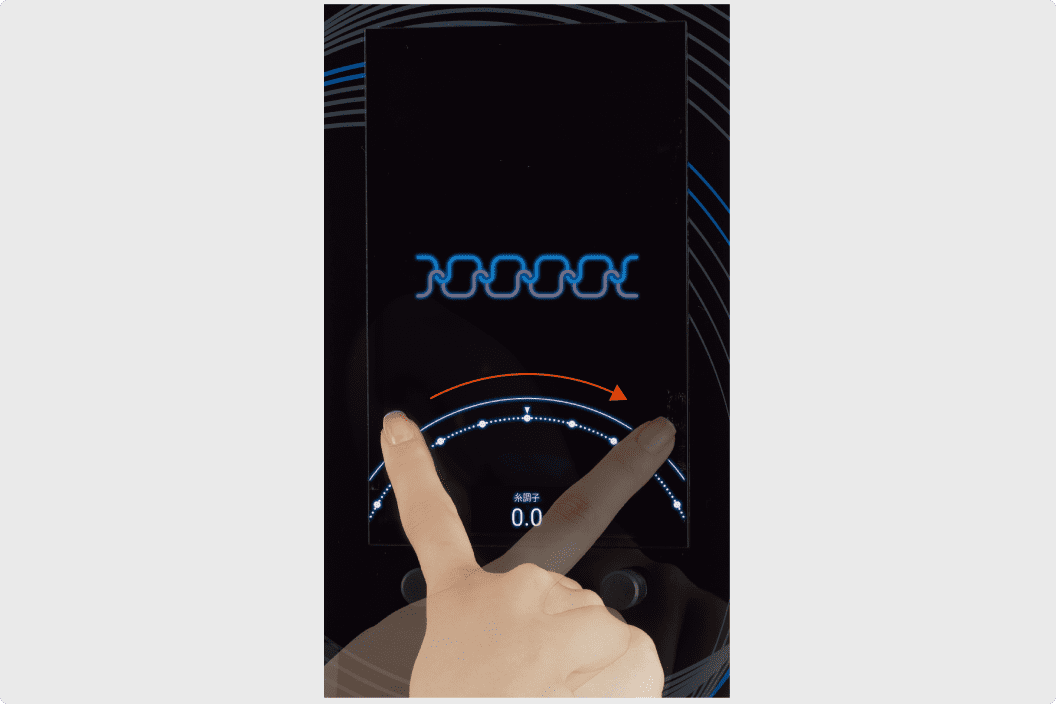
JUKI Sewing Net
A technology that allows users to browse the Internet using wireless LAN on the main unit.
This technology allows users to update software in the sewing machine, view audio and visual guidance (YouTube, Instagram, etc.) with the touch panel screen, and browse instruction manuals online.
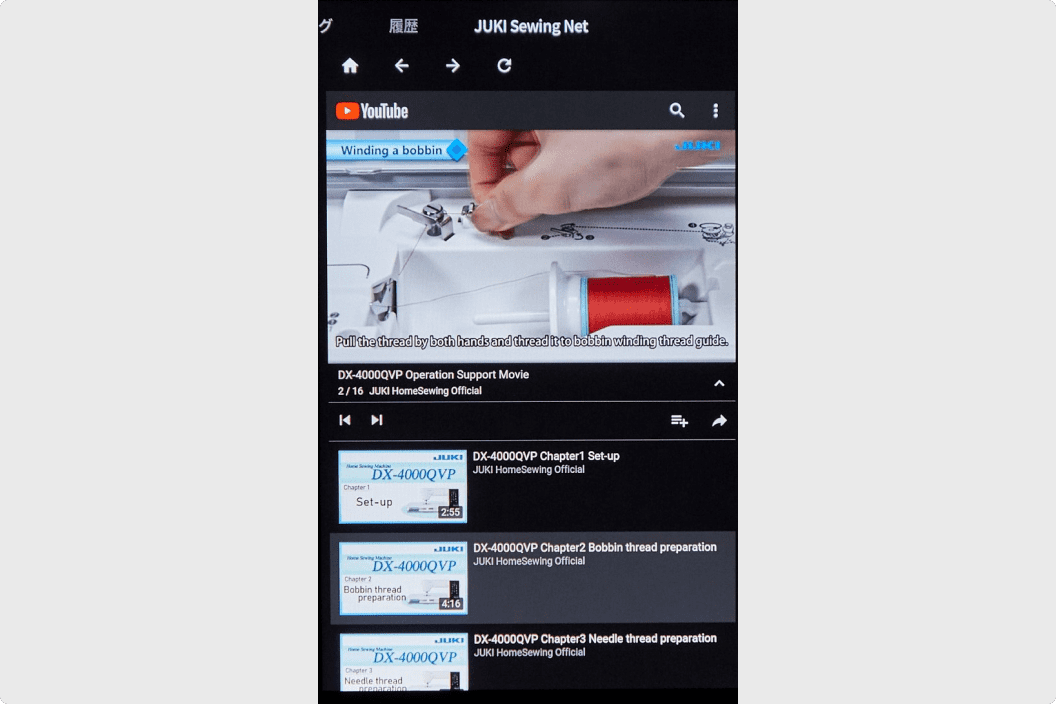
Buttonholer
Buttonhole sewing technology using professional sewing machines
This technology enables the sewing of buttonhole patterns using professional sewing machines dedicated to straight stitches. The computer-controlled XY drive system enables the sewing of various types of buttonholes in the target orientations and volumes without feed jamming, achieving benchmarks that have never been reached with conventional mechanical buttonholers.
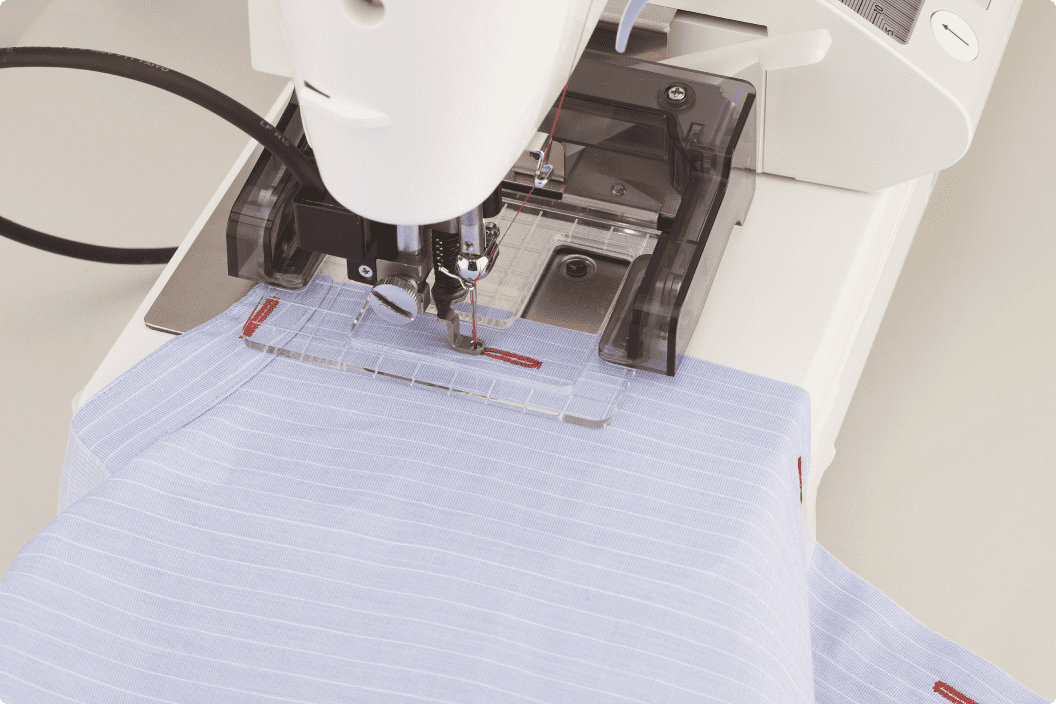
Fully automatic thread guide (Easy threader)
A technology for quickly passing looper threads for lockstitch machines through the looper hole using the force of air
With this technology, a 1 cm length of thread is inserted into the threading hole, passed through a thin pipe, and conveyed to the looper hole.Air sent from a pump powered by an electric motor passes through a narrow slit to a depth of approximately 0.3 mm. The sudden expansion of the air creates a suction force that propels the thread forward. Special processing is applied to the pipe to eliminate frictional resistance of the thread.
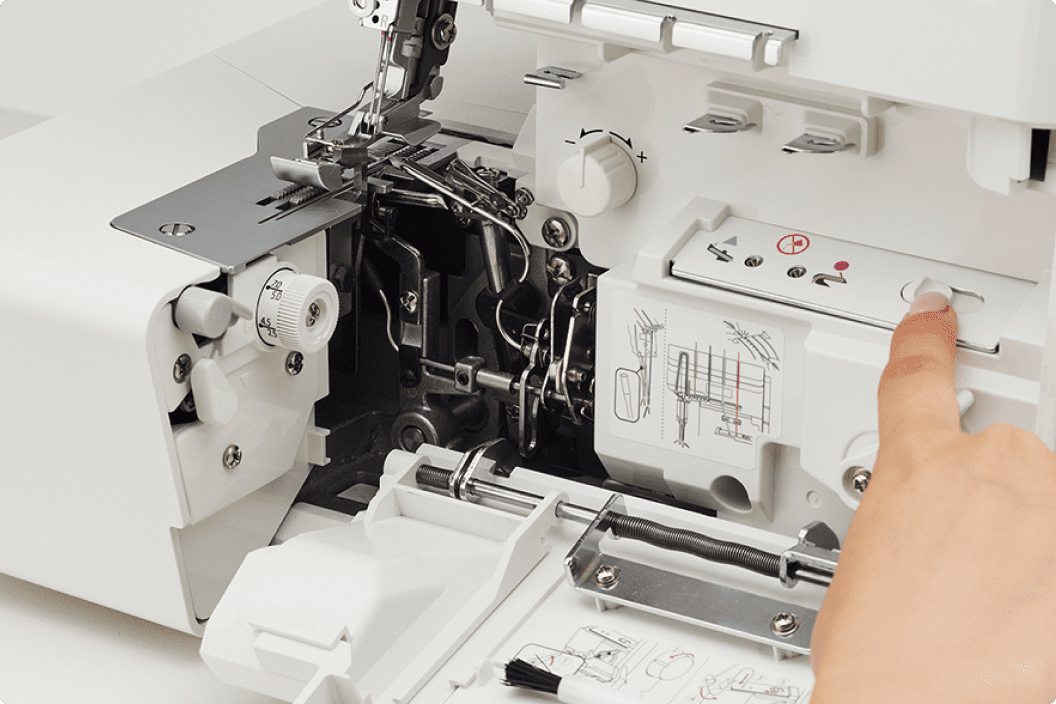
A technology for automatic thread tension
A technology that automatically optimizes the thread tension setting for chain stitch sewing machines
This is a technology for thread tension to pull out the needle thread and looper thread for a chain stitch sewing machine in the order required for each stitch. The optimum thread tension is automatically set while the amount of thread pull out is variable in conjunction with four parameters: the height of the presser foot, width of the knife, feed pitch, and seam type.
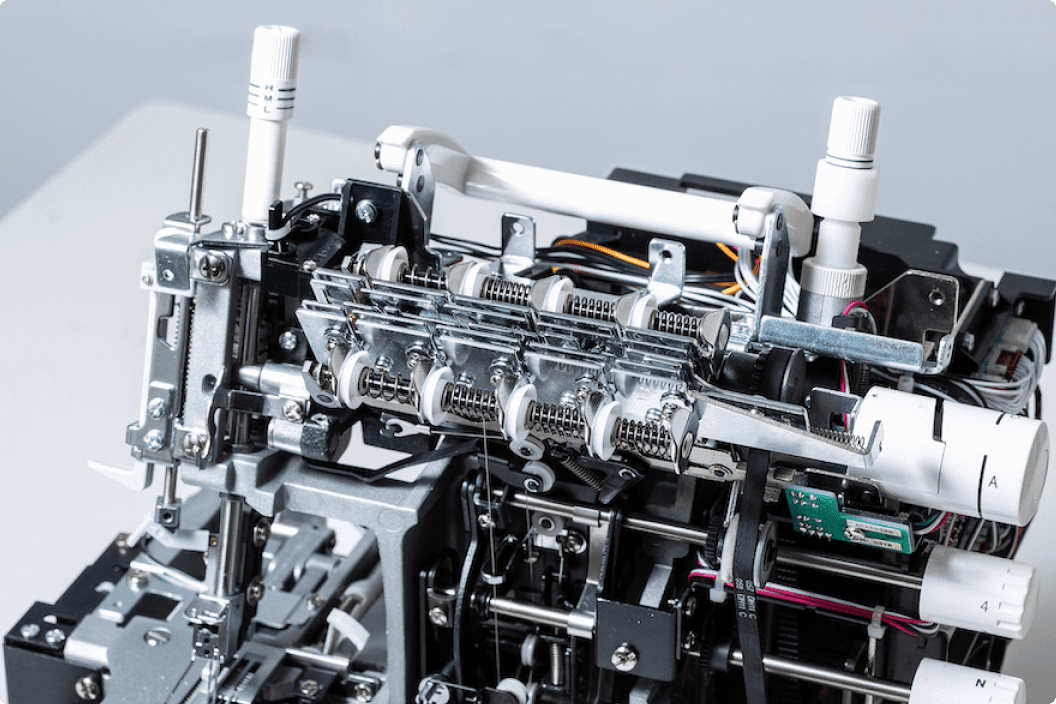
An chain-off thread cutter
An automatic chain-off thread cutter technology that cuts chain-off thread easily and safely with the touch of a button
This is an automatic chain-off thread cutter technology that cuts chain-off thread for household overlock machines with the touch of a button. A rotary knife is used that never gets in the way during the sewing operation. As an added design safeguard, the machine detects foreign objects by sensing the movement of the movable safety cover interlocked with the rotary knife. Direct contact with the knife is prevented even if a finger or another object is accidentally placed within cutting distance.
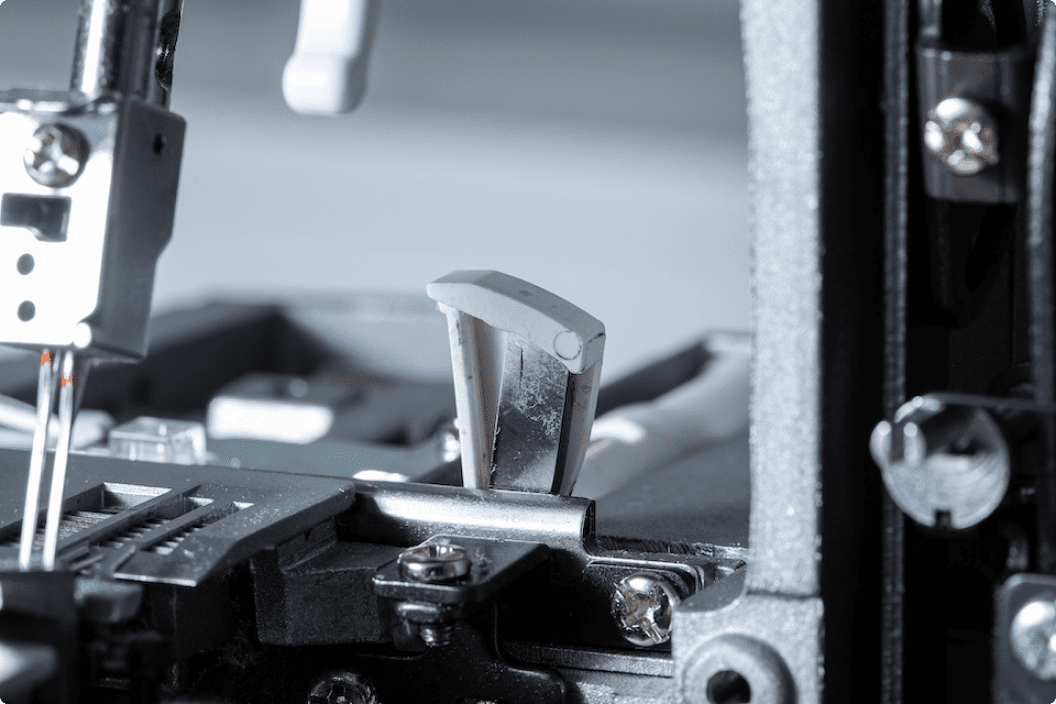
JUKI Smart Stitching
A constant sewing pitch is achieved even when the sewing speed changes.
This is a technology configured in sewing machines that can freely change the sewing direction by 360 degrees while stitching patterns. The machine adjusts its rotation speed based on the fabric movement measured by a 2D sensor attached to the surface of the needle plate. A consistent stitch pitch is achieved even when the sewing speed changes.
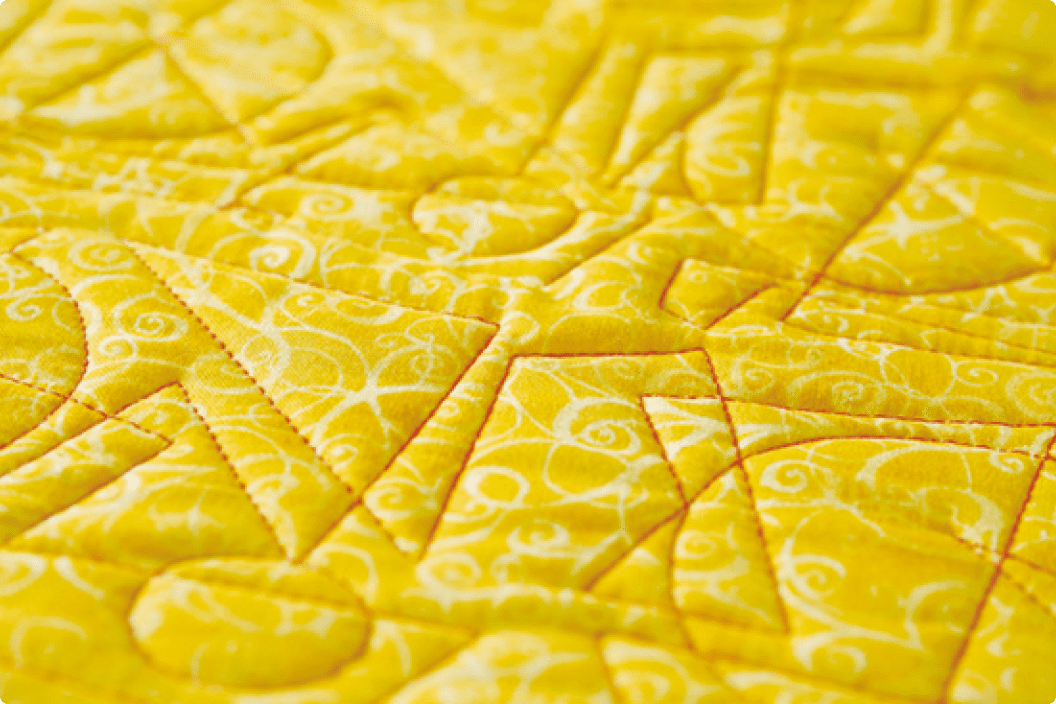
Box feed
Prevention of sewing shrinkage and fabric shifting
This technology stabilizes the feeding of fabric by creating a “square” feed trajectory that allows the fabric to contact the feed teeth without gaps. The technology smoothens the feeding of both thin and thick materials while also facilitating sewing over extreme steps. By designing a specialized cam shape and creating an extreme motion that feeds the fabric horizontally and drops straight down, JUKI has achieved a box-like square trajectory for the needle movement.
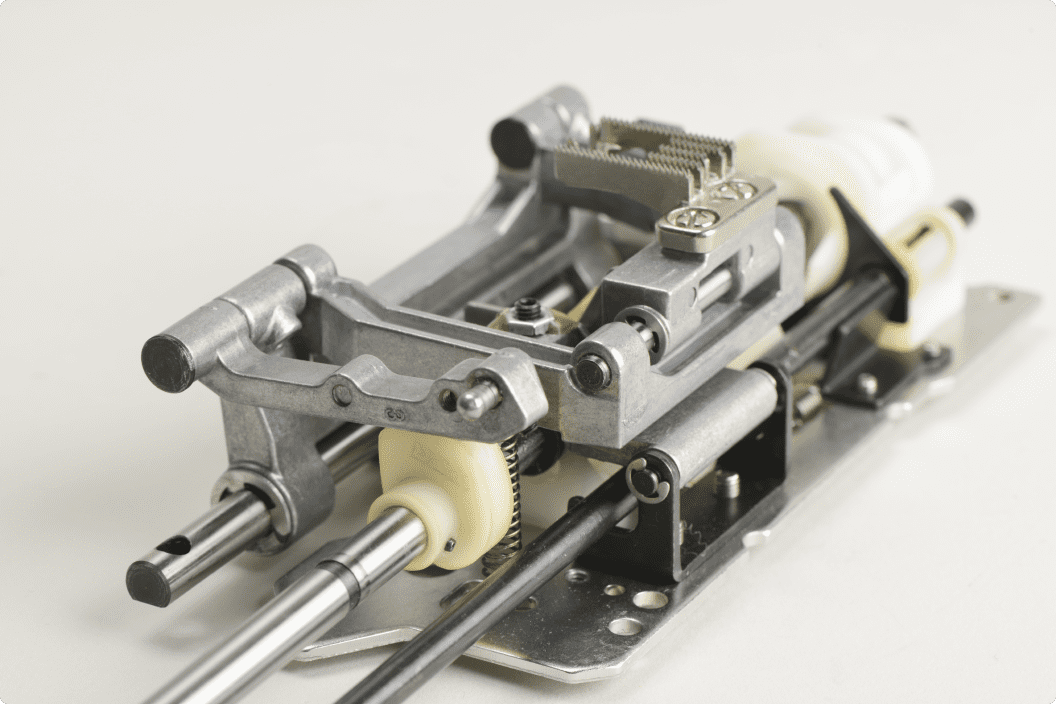
Automatic thread tension
The needle thread tension is adjusted according to the sewing pattern type.
This technology automatically adjusts the needle thread tension according to the sewing pattern. The pressure determined from the swing width and feed amount provides the optimum thread tension to the needle thread for each of the 351 built-in sewing pattern types and character patterns. The rotation angle of the thread tension cam is digitally controlled by a dedicated stepping motor.
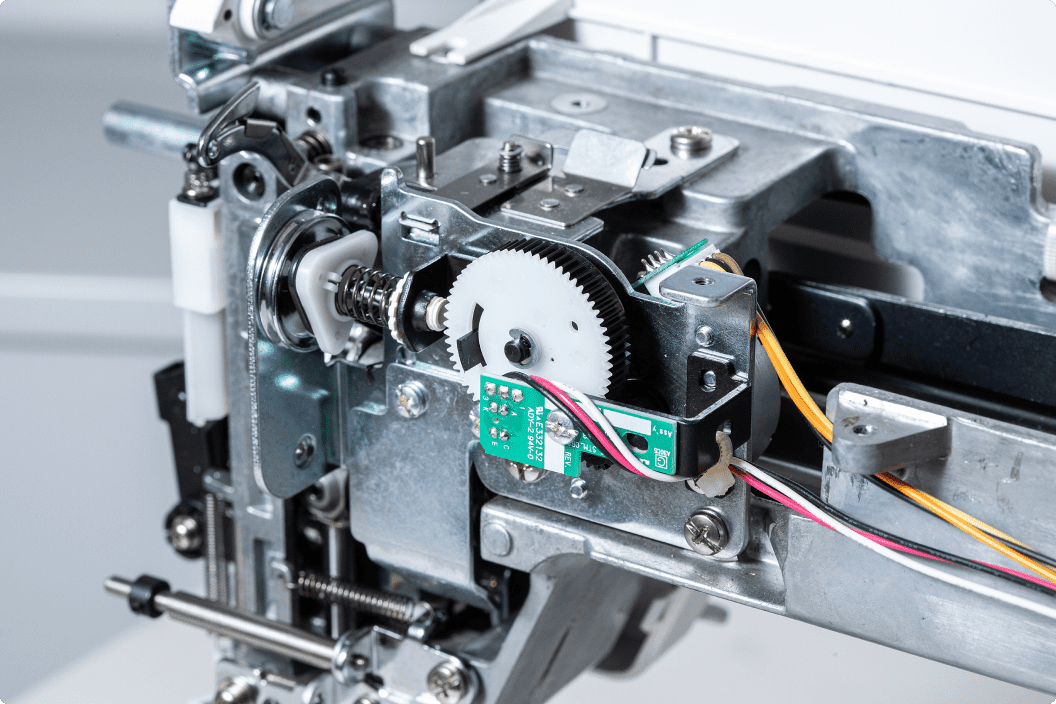
A float mode
A unique technology to recognize the condition of the presser foot
This technology enables sewing with the presser foot slightly raised from the fabric. The encoder constantly detects the height of the presser foot, allowing adjustments in 0.1 mm increments to suit the material. This feature prevents sewing misalignments such as those that occur when sewing with cotton batting between fabric layers.
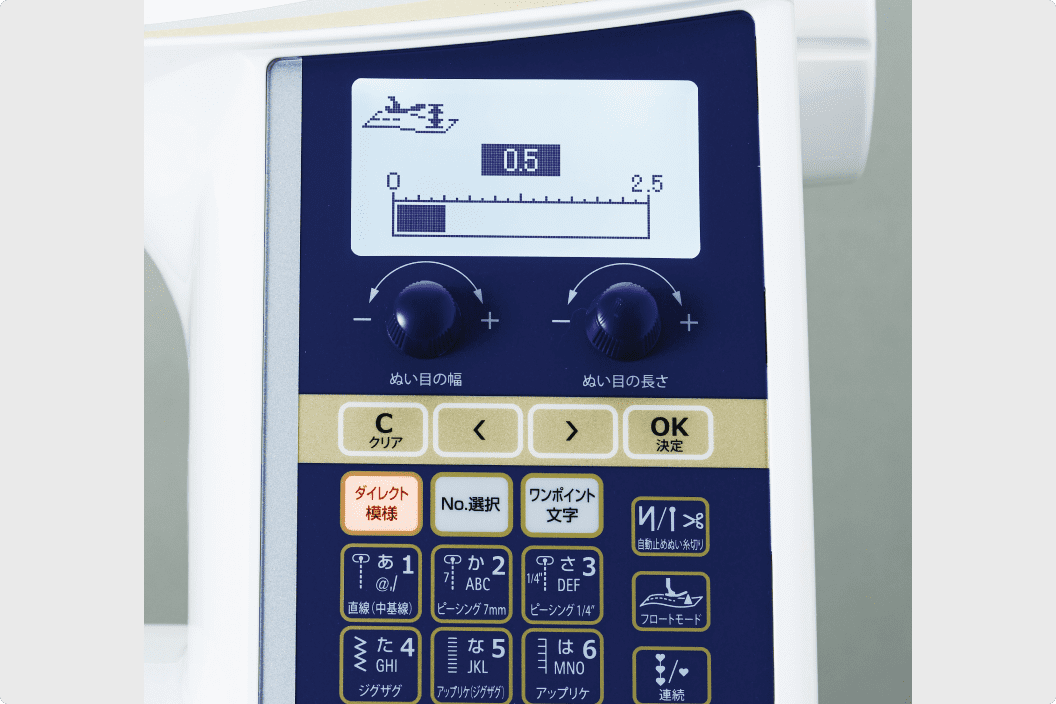
A pivot function
A proprietary sewing machine technology synchronized with sewing start and stop operations
When a sewing operation is paused, this technology stops the machine while the needle is still in the fabric and slightly raises the presser foot.The presser foot height setting can be changed according to the fabric thickness detected by the encoder. When the sewing machine is restarted, the presser foot automatically lowers to save time when sewing the corners and curves of a fabric.
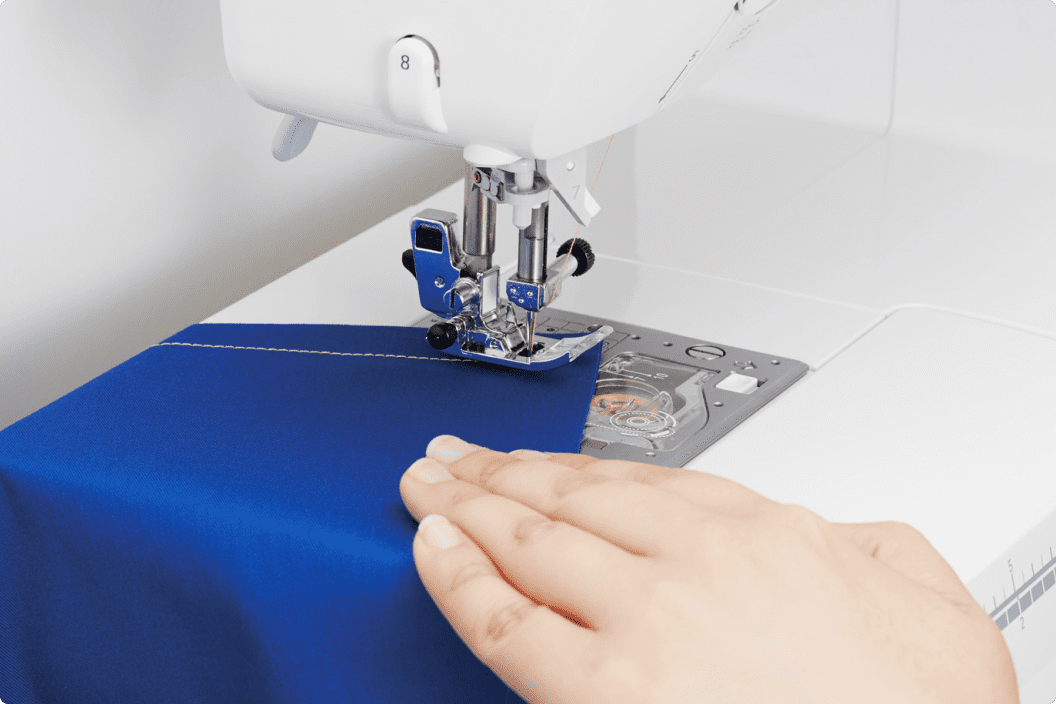
A planet head
A planet head is a rotary-type. The head enables the high-speed placement of small components.
The rotary-type head employs a rotary technology that enables high-speed placement using a compact component pick-up and placement system.
The sequential rotation of picked up components allows for efficient component recognition and shorter tact times. Misplacement can be easily identified, as the components are placed in the order they are picked up. This design also makes it possible to increase the number of nozzles*.
- *Nozzles: the parts that pick up and place components
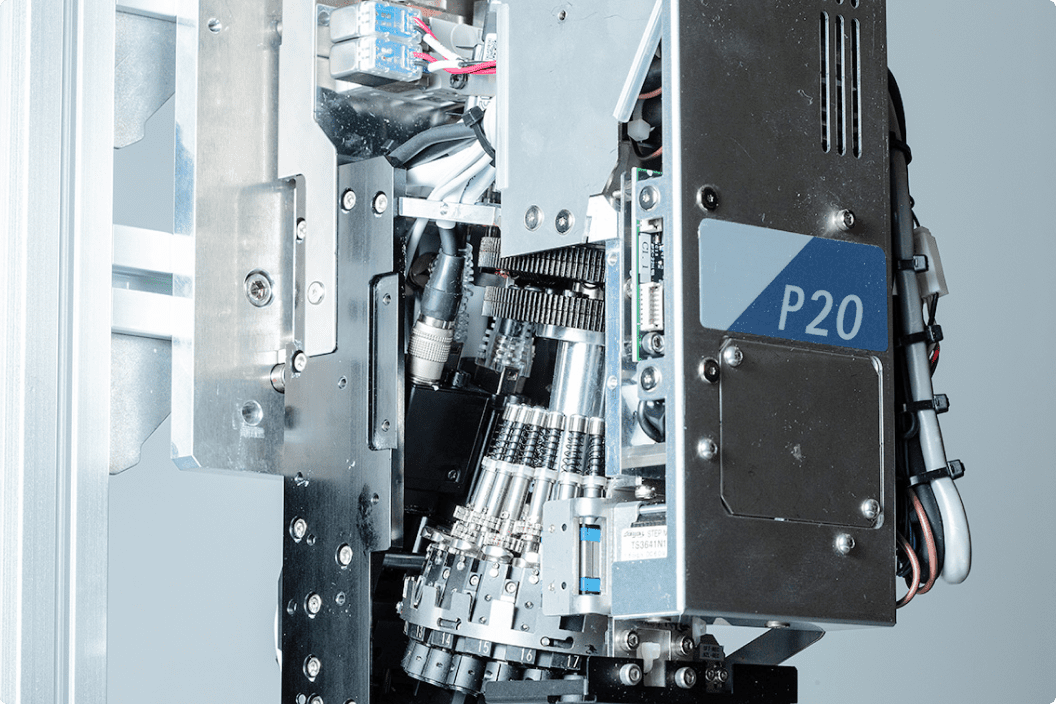
A “Takumi” head
The height at which component recognition occurs varies from one component type to another.
The Takumi head is an in-line type. The in-line type head employs a technology that keeps the head fixed while moving only the laser recognition device up and down according to the height of the components being placed. The components are recognized at the optimum height for high-speed placement. One type of head specification is available for each component height, ensuring both high speed and versatility.
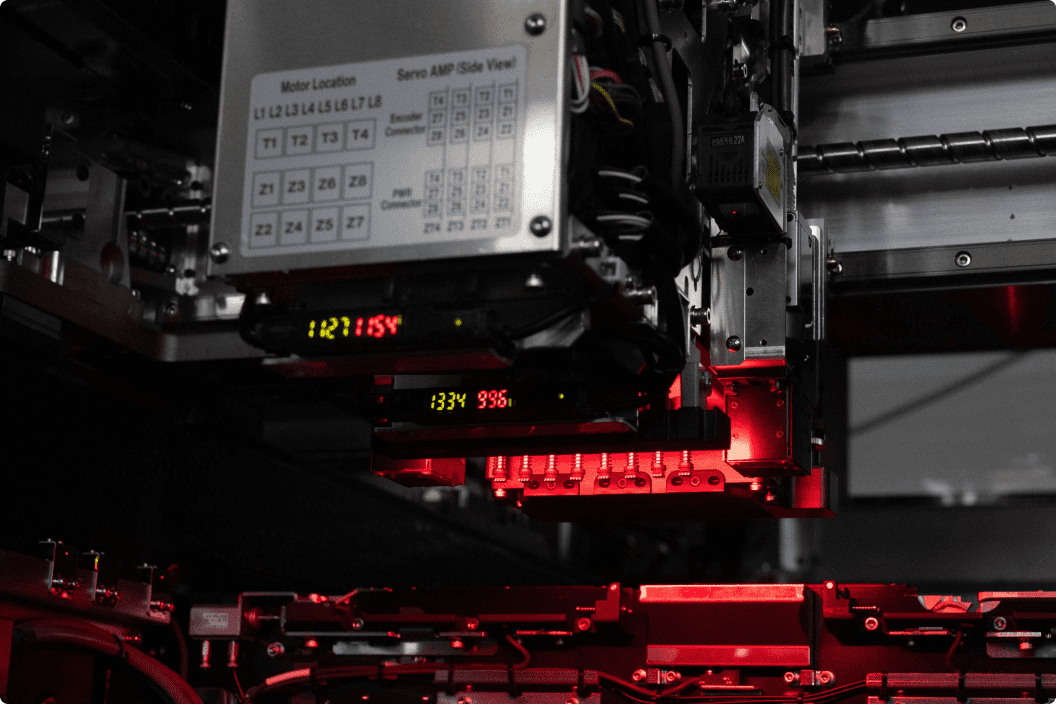
Head replacement
A technology to replace two different heads in a single machine
This technology enables the quick switchover between planetary (rotary) and Takumi (in-line) heads to suit the production item. A manufacturer can easily build a flexible production line that accommodates even drastic production changes.
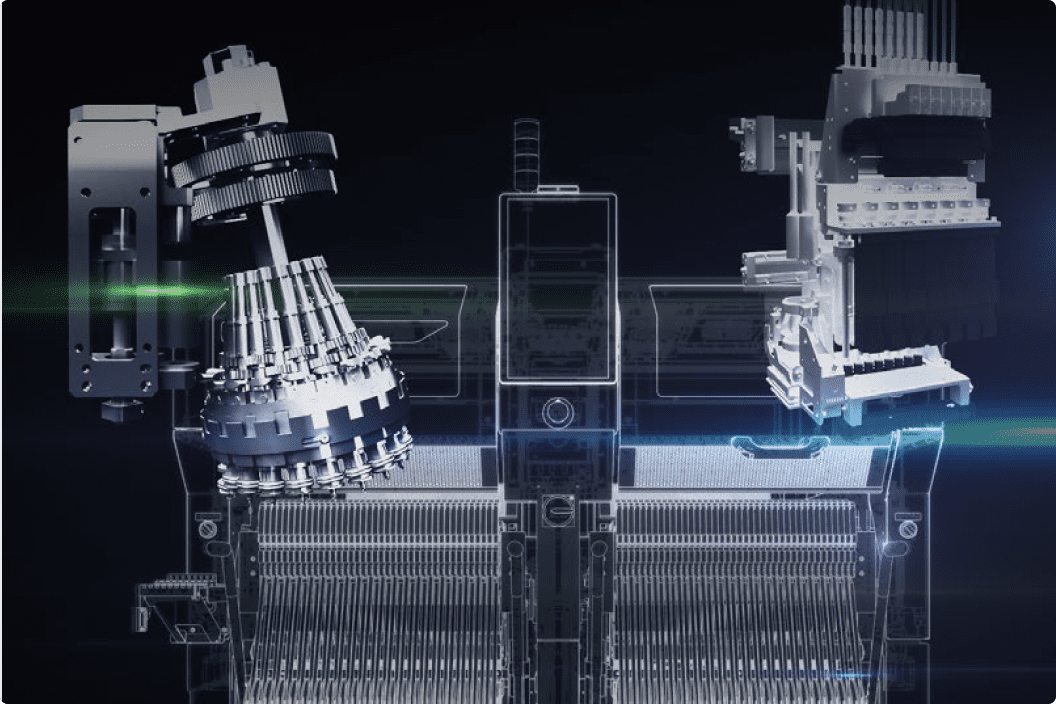
A technology to recognize high-precision pins
Image recognition of inserted odd-shaped components
This technology can simultaneously recognize the positions and lengths of pins, bosses, and other features on inserted components through 3D image processing of their leads.
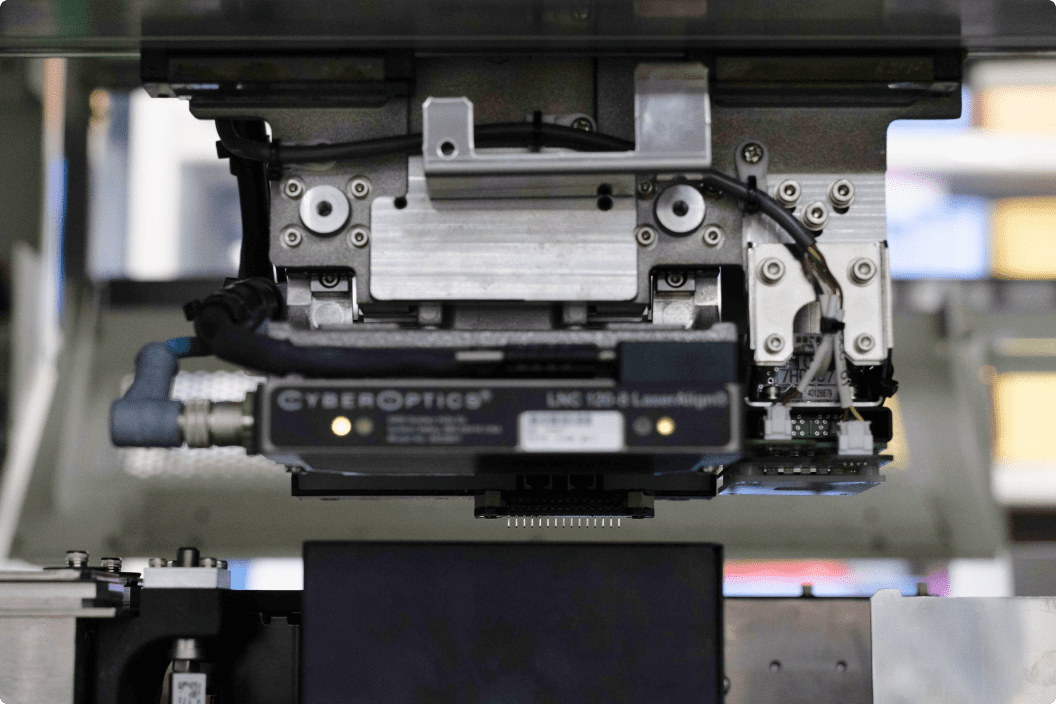
Laser recognition technology
Vision recognition of component status before and after component pickup and placement
This is a technology that calculates the position and angle of components by equipping the head unit with a high-resolution flying recognition unit and reading their silhouettes using transmitted light.
Calculations can be performed instantly during XY movement using the flying vision system, enabling shorter tact times.
By monitoring the state of component pickup up to the point before placement, the system can verify the presence and absence of components during pickup and placement, in addition to confirming normal pickup and placement operations. The system can also detect the presence or absence of defects after component placement, enabling the immediate identification of the causes of defects and high-quality production.
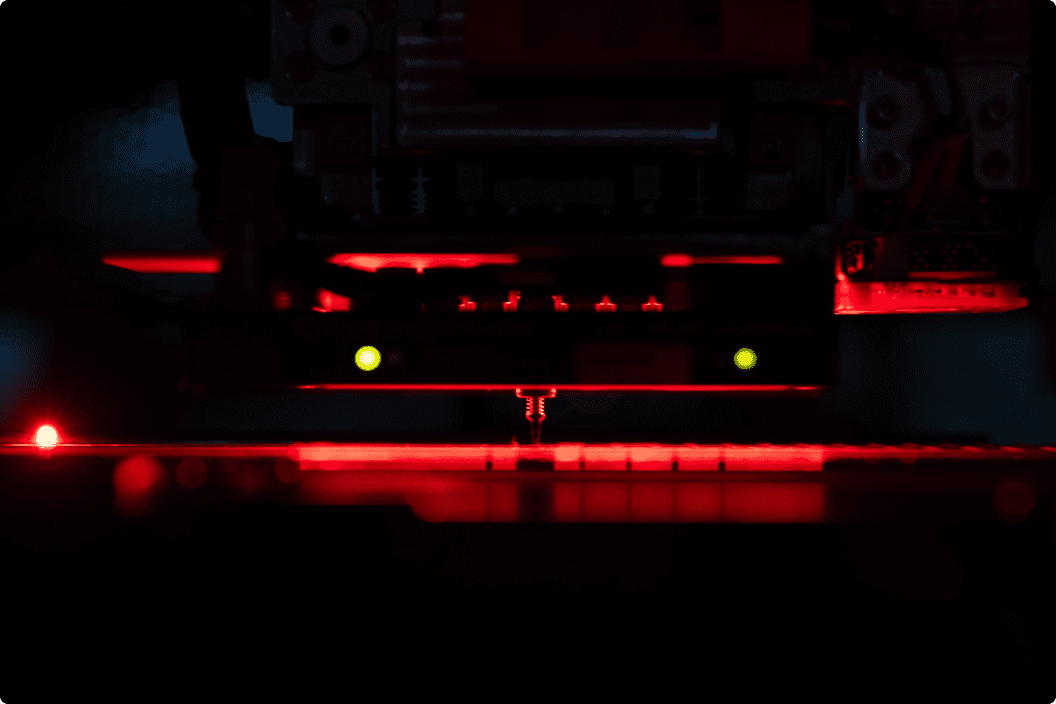
3D image recognition (inspection machines)
Clear imaging using a DLP type projection system
This technology utilizes projection and imaging techniques to perform three-dimensional inspection. Measurement accuracy can be improved by arranging DLP projectors in four directions on the head unit and projecting 32 patterns of striped light onto the component.
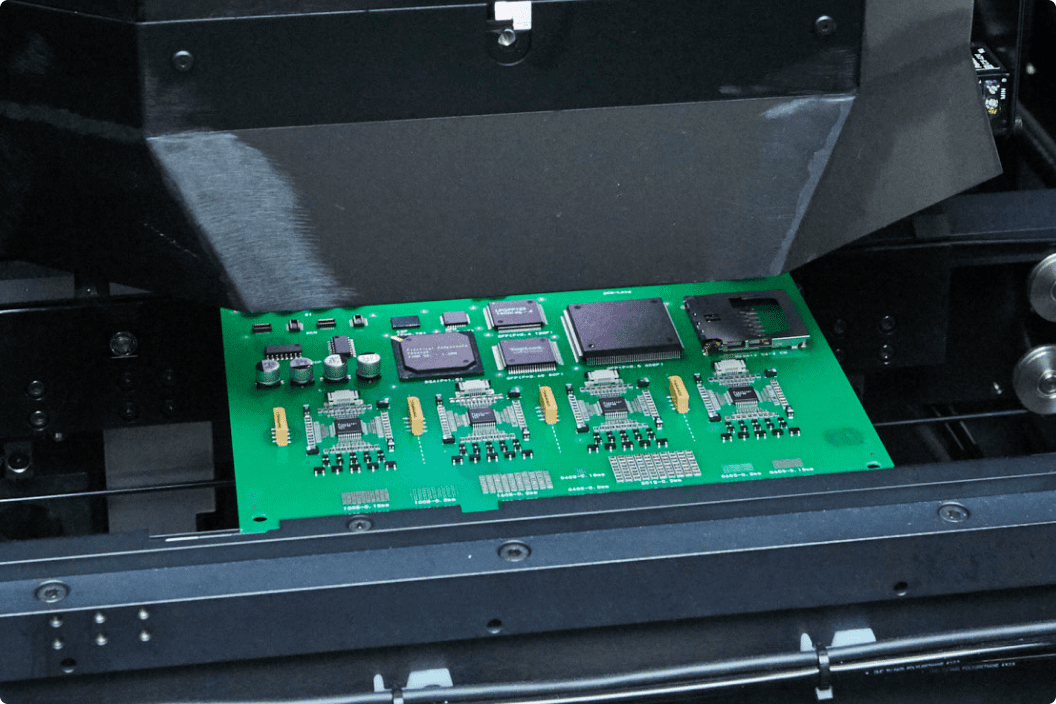
Image recognition technology
A technology that achieves stable component recognition using a dedicated camera and various recognition methods
This technology can determine component positioning and the presence or absence of defects by using various lighting methods and a dedicated component-recognition camera that captures images of everything from small chips to IC components and large or odd-shaped components.
By simultaneously illuminating components from below and the side using different wavelengths, the image-processing system can measure XY coordinates from below and the component thickness dimensions from the side, enabling higher processing speeds.
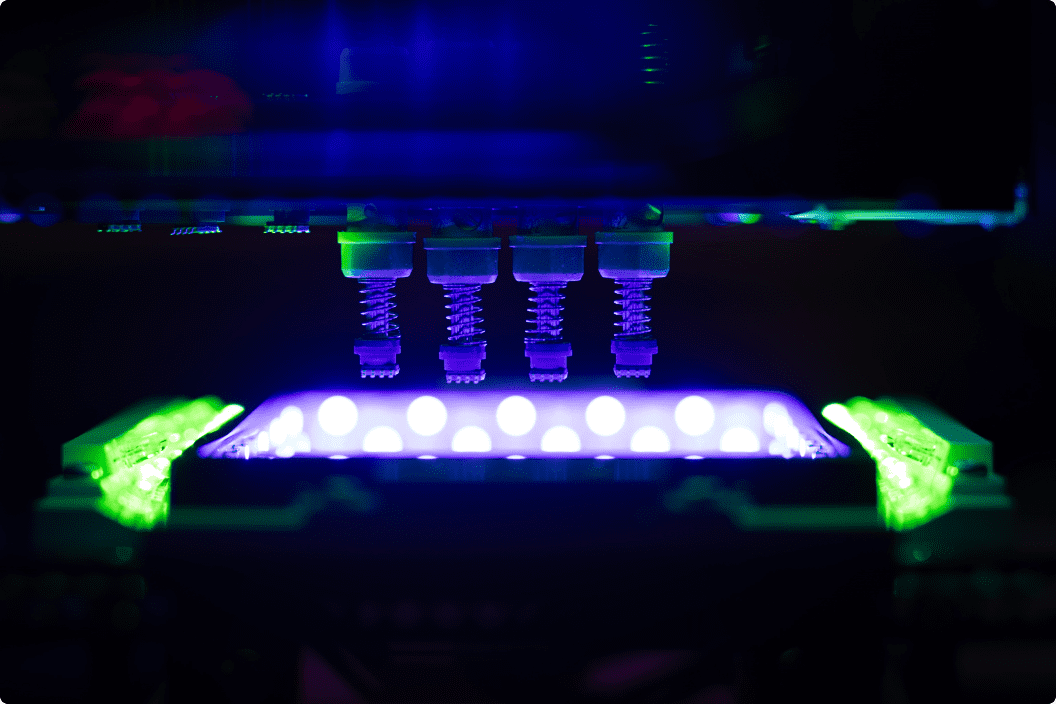
Component verification system (CVS)
A technology to inspect the electrical characteristics of components before the start of production using chip mounters
This technology inspects the electrical characteristics (resistance value, capacitor capacitance, and component polarity) of components to be placed before production starts or when production resumes after a component runs out. With its ability to inspect components that cannot be determined by visual inspection machines alone, this technology prevent component reels from being incorrectly loaded and eradicates the misplacement of components.
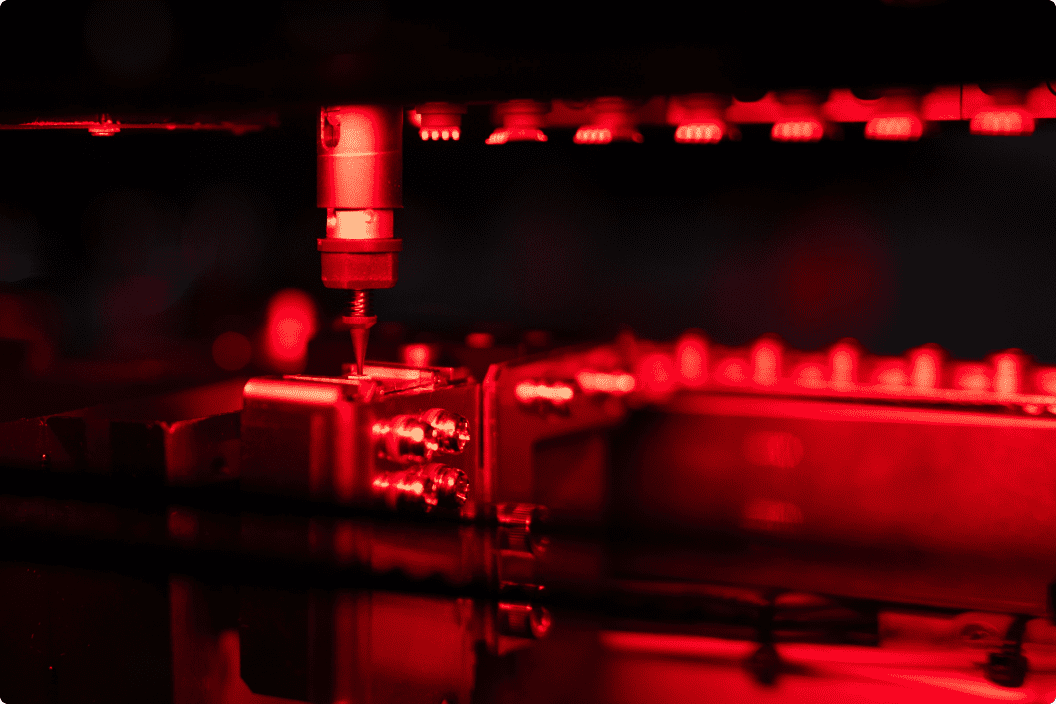
Clear Vision Capturing System
Lighting-based inspection technology
This technology performs inspections using a 12-megapixel color CMOS camera, coaxial illumination, three-stage illumination with shifting illumination angles stage by stage, and a telecentric lens.
The three-stage illumination unit is divided into eight sections at 45-degree intervals. A composite of 8 images captured by illuminating the component sequentially from each illumination area is generated using a photometric stereo technique called i-3D technology. Detection accuracy is enhanced by highlighting scratches and other defects on the component surface.
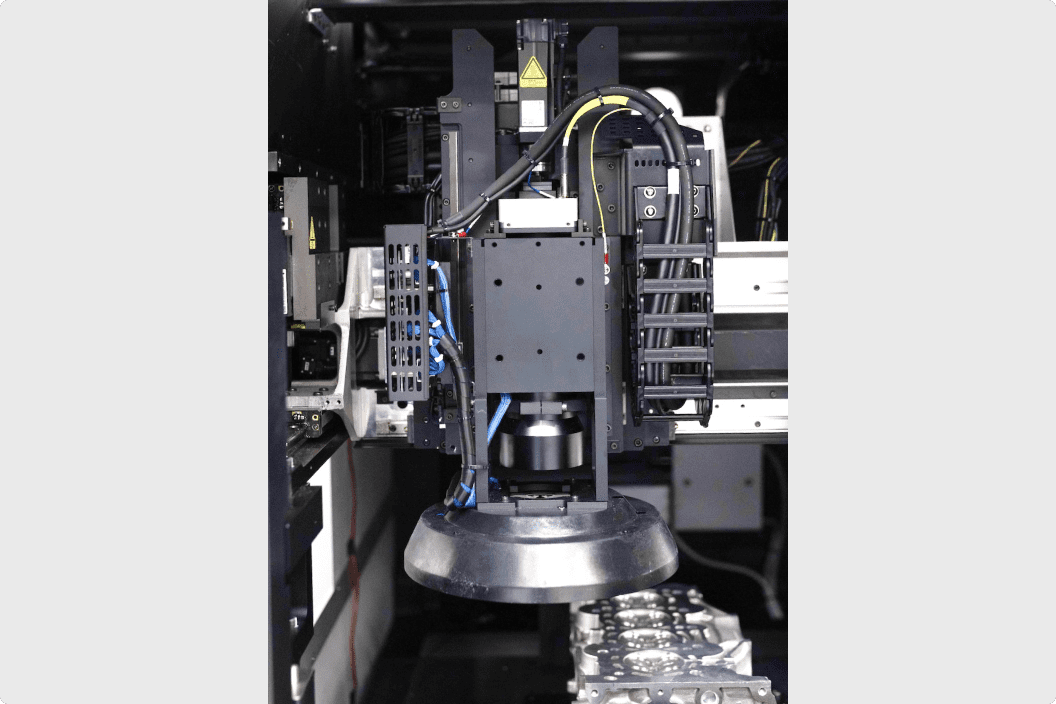