Solving Social Challenges
Creating employment opportunities
We support the growth of the sewing industry, a labor-intensive industry in emerging economies, through our industrial sewing machine business.
We will evolve workplaces from simple and labor-intensive places to people-friendly places by providing equipment and systems that make factories smarter.
- Items related to the SDGs
-
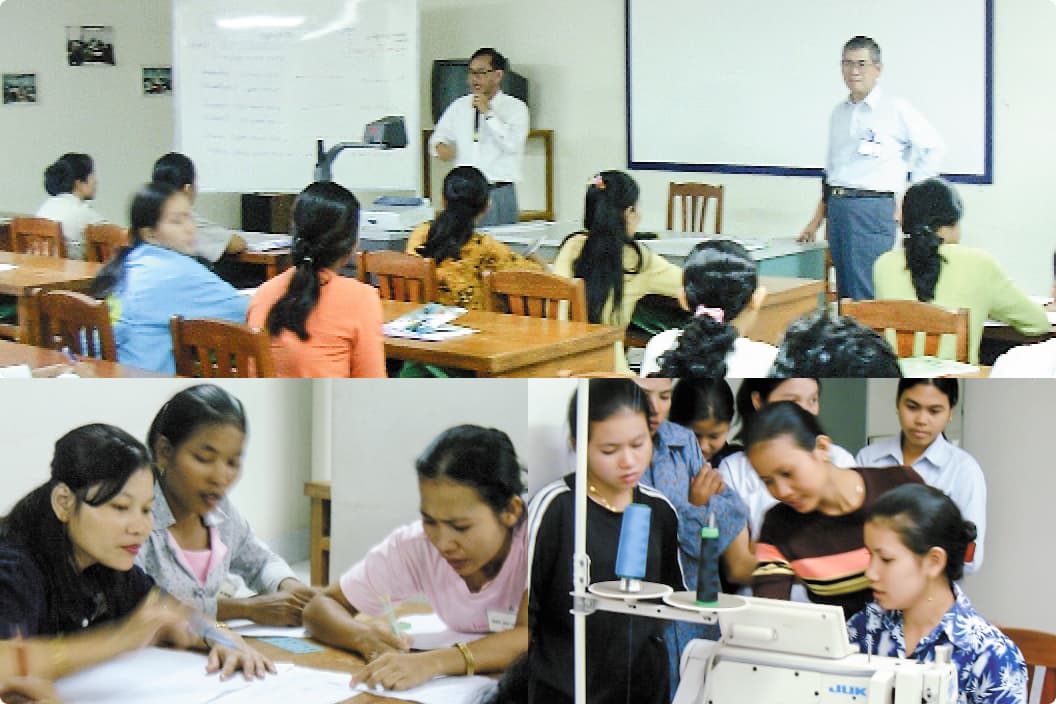
Creating employment opportunities in emerging countries
The Sewing Efficiency Laboratory, established in 1959, continues to provide support activities that use production management and industrial engineering (IE) to optimize operational performance by maximizing the power of “materials, equipment, and people.”
Based on this activity, we participate in ODA (Official Development Assistance) projects that foster export industries in developing countries and ultimately support the creation of national prosperity and employment.
We have provided equipment and educational training to local apparel training centers through partnerships with government agencies in developing countries such as Cambodia, Myanmar, Ghana, and Madagascar.
Our goal is to put the participants on track to becoming managers and other key personnel, and to thereby create a cycle of employment in developing countries.
Promoting the participation of various human resources in society
There are still many illiterate people in the world, especially in emerging countries.
JUKI’s ongoing support for vocational education will help to grow working populations, improve the treatment of workers, and produce other positive effects in those countries.
- Items related to the SDGs
-
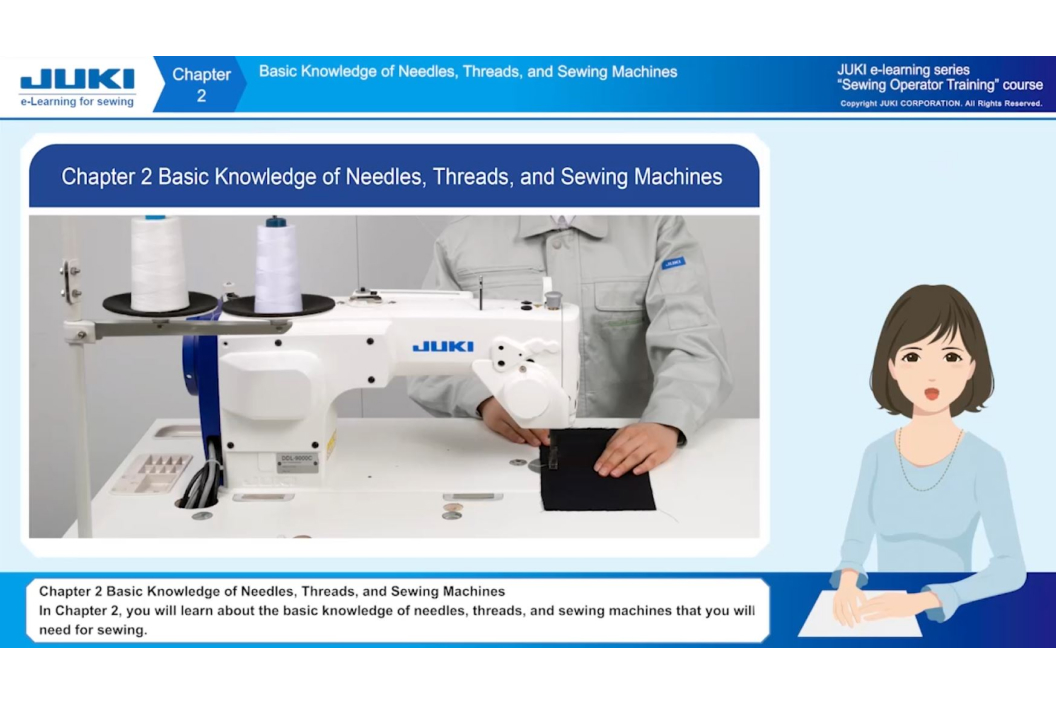
Developing and offering e-learning menus to train workers
We are continuously conducting seminars and group training programs to improve productivity, sewing quality, and maintenance techniques in the sewing factories of our customers.
We started to offer these programs in a menu of “e-learning” activities in 2020.
We will further expand the menu and promote activities to train operators and conservators through highly specialized education.
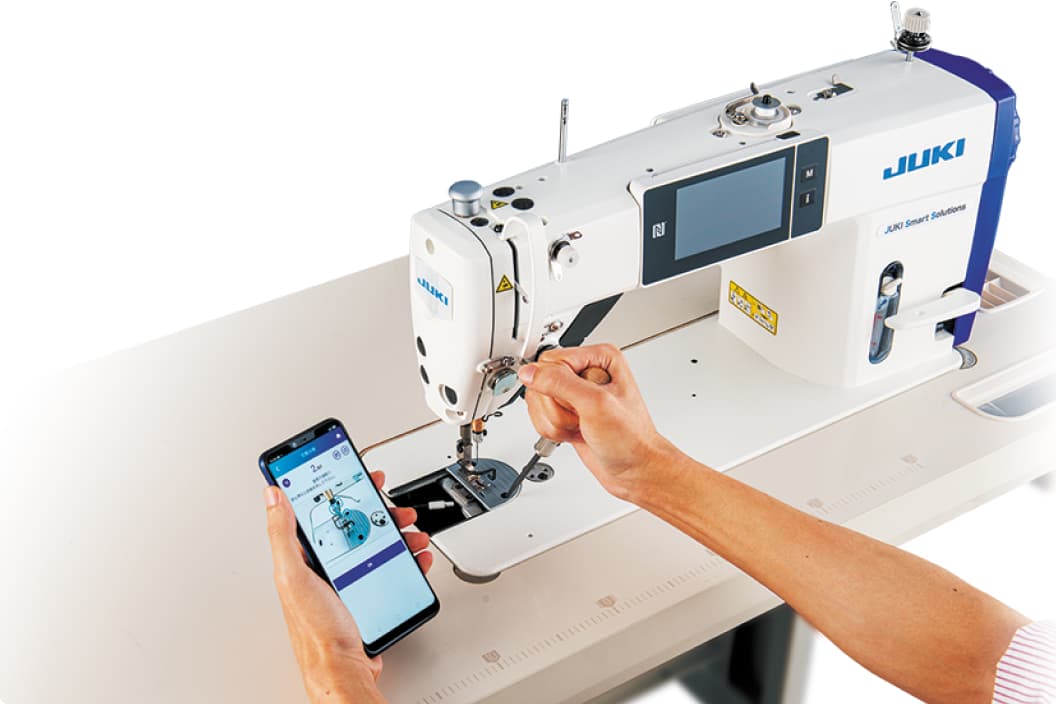
Providing an inspection support system that facilitates employee development
Industrial sewing machines are provided with “voice guidance functions” and “illustrations and symbols” for explanations.
We also offer a free system to assist sewing factories in their daily sewing machine inspections with a smartphone app and app for PC browsers.
A menu of 10 to 20 inspection items represented on screen as photographic images can be easily navigated during the inspection process. The app designs ensure that anyone can understand the inspection process and all of the important parts of the sewing machine structure involved.
Through these initiatives, JUKI is promoting employment in emerging countries.
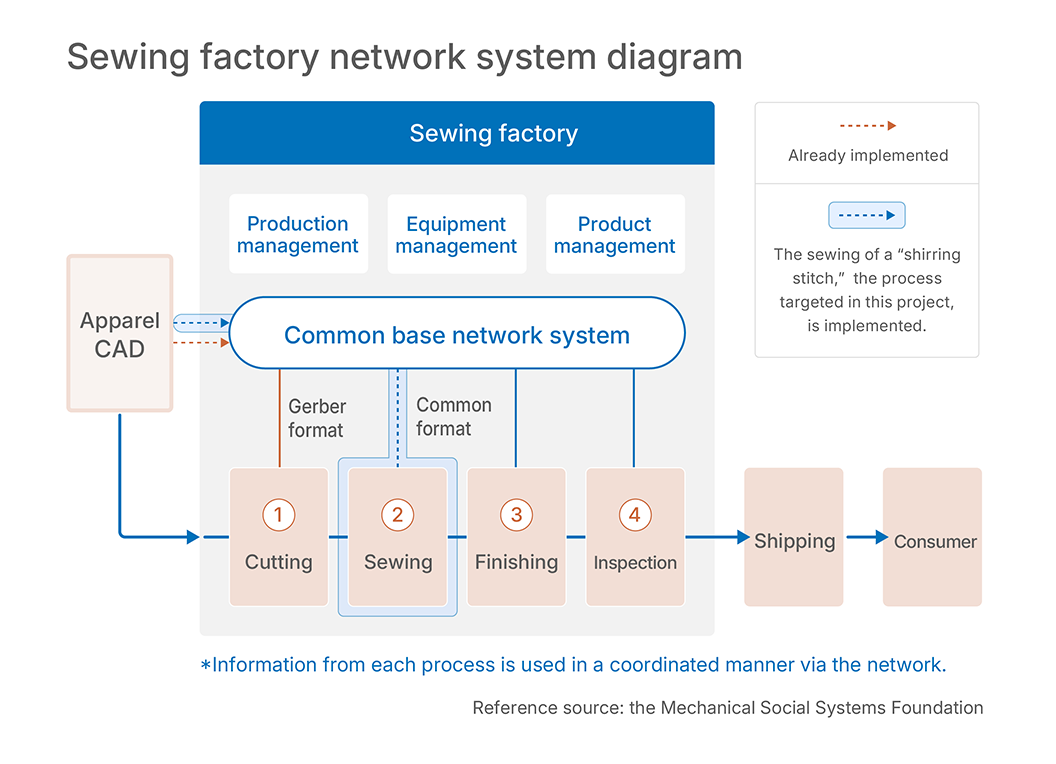
Promoting efforts to simplify difficult processes by linking sewing machines and CAD
JUKI is a member of the Japan Sewing Machinery Manufacturers Association, an organization promoting initiatives to simplify difficult processes that require skilled workers, such as shirring, by directly importing CAD data into sewing machines.
The Mechanical Social Systems Foundation commissioned the association to develop an innovation strategy for fiscal 2023.
After directly importing CAD data in the form of a garment blueprint, a digital machine can sew the garment without relying on the knowhow of a skilled worker.
Our first step in building the CAD-supported sewing system will be to create a “common format” that links all apparel CAD systems and digital sewing machines. A fully linked network of machines will automate the sewing process in a coordinated fashion to optimize the mass and customized production of garments in the future.
-
*
JUKI is a member of the Japan Sewing Machinery Manufacturers Association.
Contribution to the reduction of clothing waste
Mass production and large inventories are generating abundant clothing waste.
JUKI, a company that supports the production of sewn products, seeks to solve this issue by optimizing low-volume production, improving the efficiency of mass production, and expanding its business domains.
- Items related to the SDGs
-
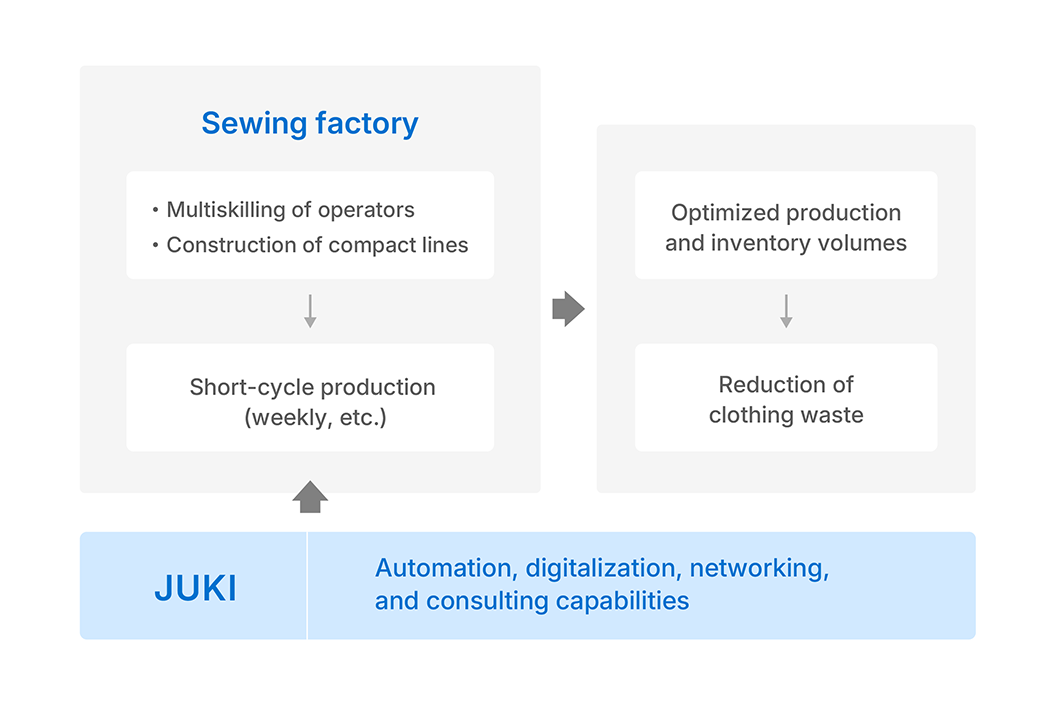
JUKI harnesses its automation, digitalization, networking, and consulting capabilities to achieve the optimized production volumes its customers seek
The aim of JUKI’s initiatives for optimized production volumes is to construct highly productive and compact lines that make full use of JUKI’s forefront automation, digitalization, and networking capabilities to output optimized inventory volumes through short-cycle production.
Digital sewing machines readily accept changes in seam adjustment values with a few touches on the panel, enabling fast and easy changes in the sewn items.
Labor savings are realized by automating the sewing process, and production progress and output are managed by the network-based JaNets system.
JUKI will also be building a production system that eliminates clothing waste in the fashion required by each customer, based on its proven consulting capabilities backed by more than 60 years of experience as a best partner to garment manufacturers.
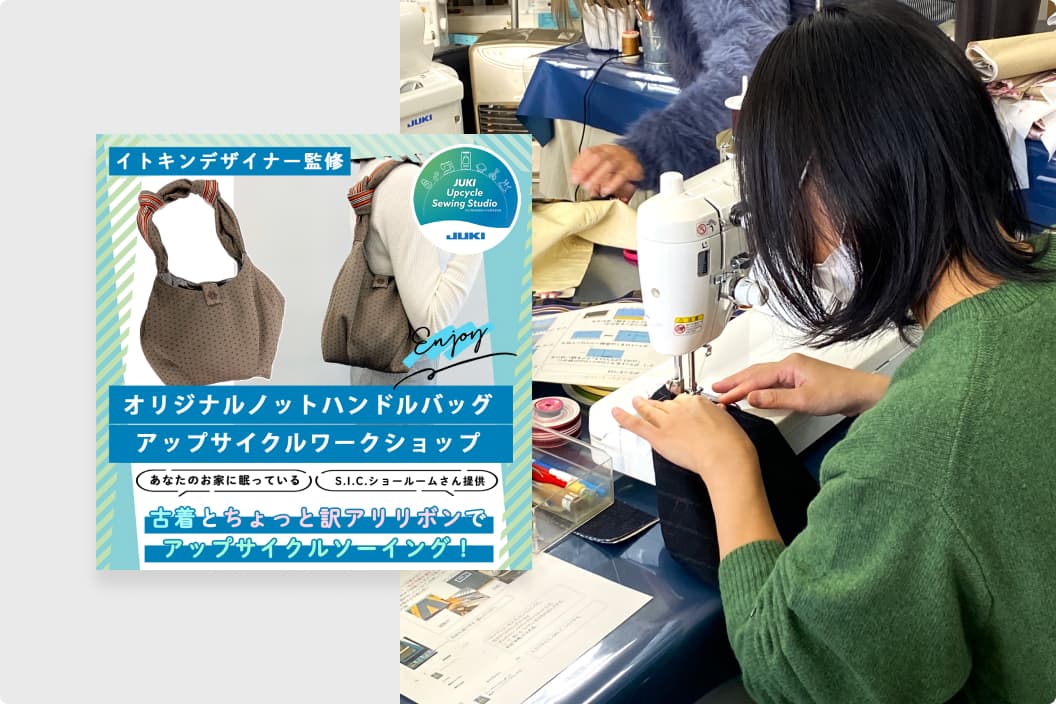
The bags were upcycled into knot handle bags and tote bags designed by Itokin Corporation, an apparel manufacturer that supports this activity.
Spread upcycling activities using old clothes, waste materials, and by-products
JUKI’s “upcycling” activities give a second life to old clothes and waste materials that have outlived their usefulness by recycling them into things that are new. To support these activities, we have been holding an annual Upcycle Award event in-house since 2021.
We have also been promoting workshop activities to upcycle clothes and unneeded fabrics from home into bags and other items. The scope of these activities has been expanded to include our customers since 2023. The sewing machine shops that support these activities around town are now known as “JUKI Upcycle Sewing Studios.”
Securing Occupational Health and Safety
JUKI protects its employees from workplace accidents by providing safe and secure working environments and builds workplaces where every employee can maximize their potential.
JUKI is also committed to creating good working environments for customers through the products and support it provides.
- Items related to the SDGs
-
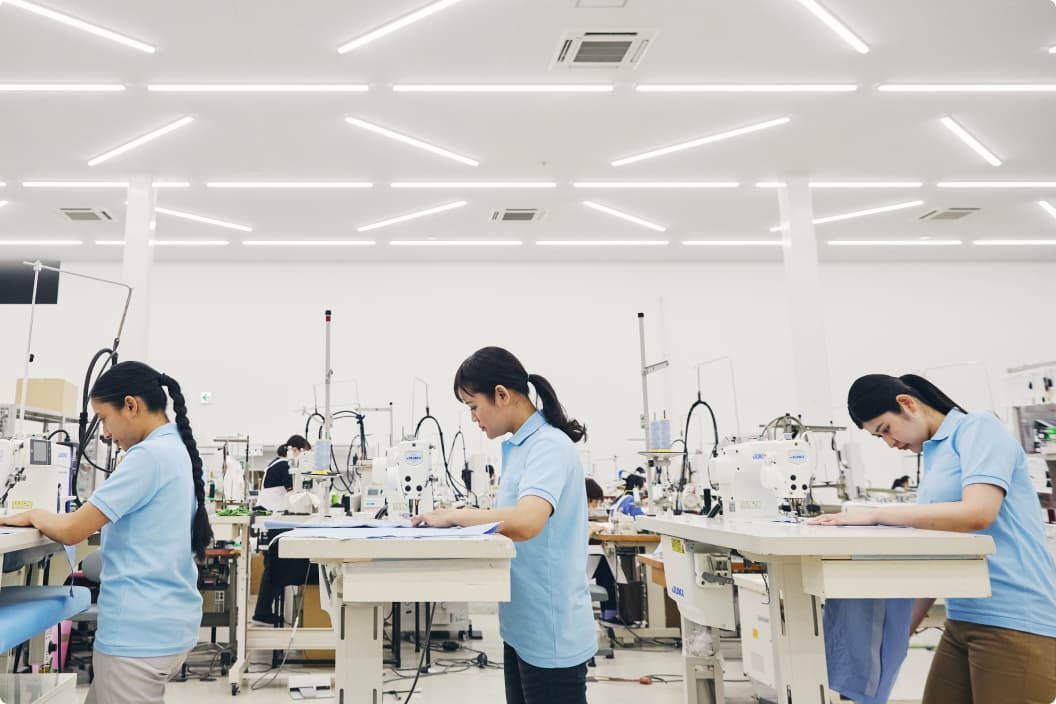
Toward Safe and Clean Sewing Factories
To realize clean and fatigue-free working environments, our product designs duly consider the suppression of the operating noise and vibration of sewing machines while optimizing operability, safety, and the dust-collection functions.
We will also realize people-friendly working environments through de-skilling and measures to automate equipment that reduces heavy workloads.
Support for technological innovation by improving productivity in the electronics industry
As a comprehensive manufacturer of PCB mounting equipment, we support the evolution of electronic circuit boards for electronic and electrical products by responding to increasingly miniaturized chip components and complicated odd-shaped components.
Through technological innovation, we contribute to industries that design future society with DX.
- Items related to the SDGs
-
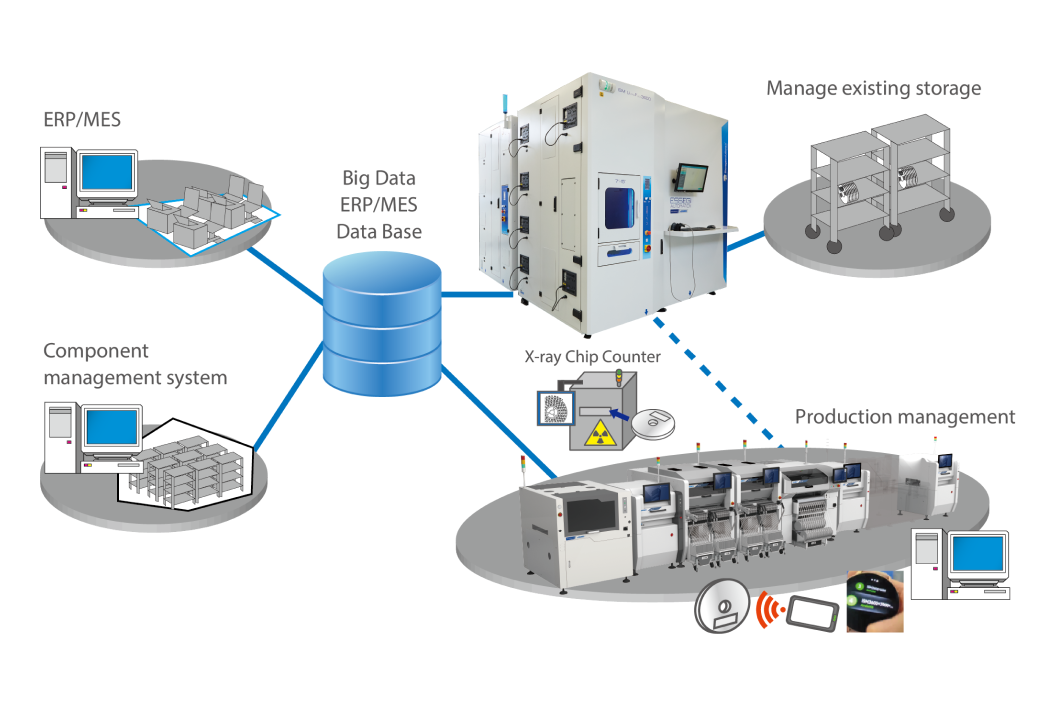
Improving the infrastructure for pre- and post-processes at PCB mounting factories
We are working to realize smart factories that eliminates manpower to the greatest possible extent by incorporating the latest technology.
To save labor in the pre- and post-processes of the labor-intensive PCB mounting line, we are deploying automation of manual work through the use of “automated warehouse” that stores and manages electronic components and “automatic insertion machine” in the post-PCB mounting process. In parallel, we are developing systems that enable linkage with core systems.
Smarter factories through labor savings bring more convenience and comfort into daily life by enabling the distribution of inexpensive, high-quality products around the world.