We want to improve productivity and quality in collars and Sleeve plackets...
Success Story: Shirt factory
- Home
- Solutions
- JUKI Smart Solutions
- Success Story: Shirt factory
Country | India |
---|---|
Manufacturing items | Men's dress shirts |
Production quantity | 14,400 shirts/day |
Proposed solution |
![]() Automation ![]() Digitization ![]() Networking |
Achieved benefits |
![]() Improvements in productivity ![]() Manpower saving ![]() Deskilling ![]() Improved quality |
Overview
When building a new factory of a similar scale to the existing factory, despite of little larger initial investment, our proposal of smart factory allowed the company to achieve the target ROI in a shorter period of time.
Target
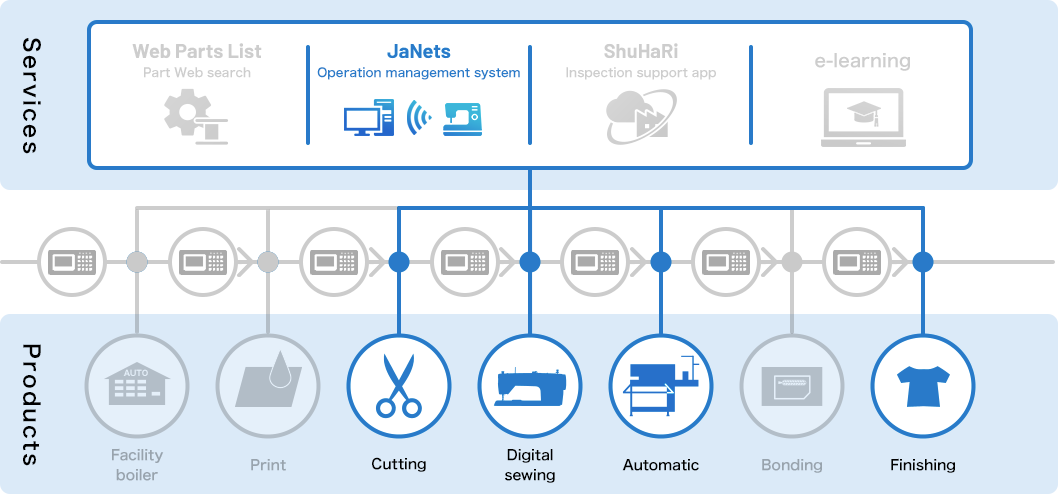
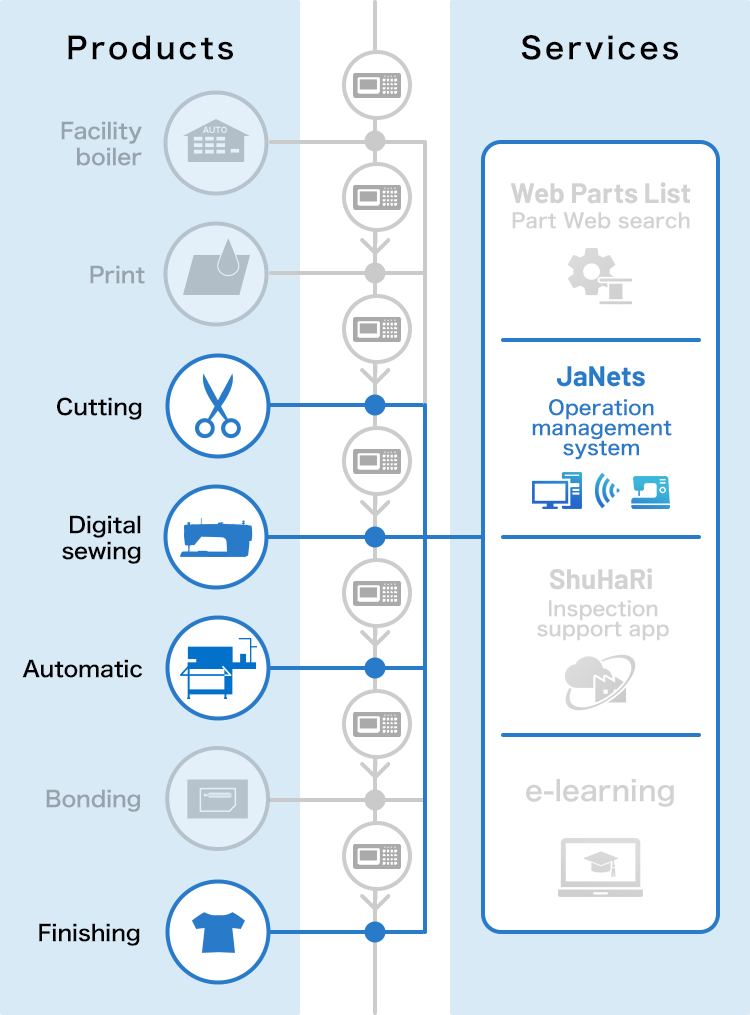
Solutions
Point 1
Automation of cutting, sewing, and finishing processes!
A number of automatic machines was proposed to the cutting process (CAM and automatic clothes spreading machine), finishing process (alliance equipment such as automatic folding machines), and sewing process (variety of automatic machines).
By automating these processes lacking manpower and time, the new factory was successful to improving its productivity with stable quality, while reducing required manpower.
(1) Cutting process
Before
Clothes spreading by hand
Automation

After
Clothes spreading by automatic clothes spreading machines
Before
Cutting by hand using vertical blade cutting machine
Automation

After
Automatic cutting by CAM

*A smart solution to automate a series of processes from clothes spreading to cutting was proposed. Operators are engaged in the initial clothes setup and the final pickup tasks only.
(2) Finishing process
Before
Automation

After
A proposal of a finishing system line using hangers
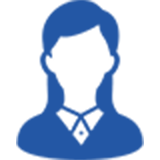
Customer's challenge
(3) Sewing process
Before
(1) Collar process
Operation using single-needle lockstitch sewing machines
Automation

After
Replaced with PS-800 (pattern seamer)
By simply setting relevant forms, scanned RFID data from these forms empowers a single sewing machine to sew different patterns for various processes.
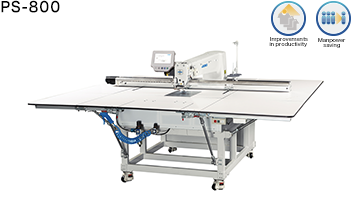
Before
(2) Sleeve placket process
Two processes are involved in the sleeve placket process (sleeve placket folding and ironing and sleeve placket sewing + stitching)
Automation

After
A sleeve placket automatic machine enabled to finish both processes with a single automatic machine, improving productivity!
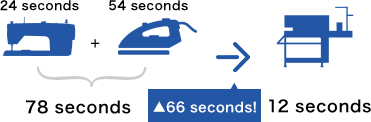
Point 2
Digital sewing machines in the sewing process provide high visualization across the factory with JaNets!
By introducing digital sewing machines, the factory is successful to achieve "ideal" sewing through applying the sample data to the actual production line. In addition, JaNets, an operation management system, allowed real-time monitoring, comprehension, and management of the factory operation.
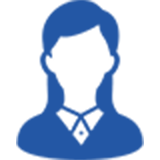
Customer's challenge
Item number changes a lot, sometimes twice or three times a day. We have to setup or tune our sewing machines...
(1) Introduction of digital sewing machines
Before
(1) Lockstitch sewing machines
Traditional lockstitch sewing machines required sewing stitching adjustments based on the fabric characteristics when the item number changes
Before
(2) Buttonholing sewing machines
Traditional buttonholing sewing machines required adjustments based on the shapes and sizes of buttonholes.
Digitization

After
Copying and pasting pattern data used in sample sewing allows sewing without sewing machine adjustments, dramatically shortening the process time
***When backing up bottleneck processes, simple copy-and-paste of data reduces the need of adjustment
(2) JaNets
Before
The production floor status could be only comprehended by a report on the following day.
Networking

After
Real-time monitoring of the production floor from the office.
Benefits
Before
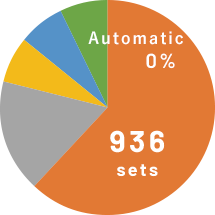
Kaizen

Standard
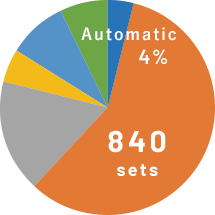
Innovation

Smart factory
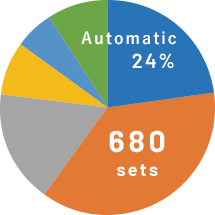
Starting from improvement from Before to Standard, then innovation is introduced by increasing the percentage of automatic machines and digital sewing machines.
By introducing automatic machines, total number of machines was drastically reduced.
-
Number of operators
1,227▶︎586 people
-
Productivity
11,680▶︎14,400 shirts/day
-
Installation space
400.1▶︎386.0m²
-
Period to achieve ROI
1.90 years