Core factory producing industrial sewing machines
The Ohtawara plant was completed in 1971 as a production base for industrial sewing machines. The plant continues to pursue forward-looking innovations as the “mother factory” in the production of industrial sewing machines for the JUKI Group and the producer of the world’s largest share of products in its class.
Our employees planted about 400 “plum trees” on the factory grounds at the time of starting operation. The trees bloom in full splendor every March, filling the premises with flowers. Fish swim in the pond. The pond on the grounds takes in a study stream of clean effluents discharged from the production lines, attesting to the environmental “safety” of the plant.
Six elements of production
We continue to enhance production levels through improvement activities focused on “M” (for man) while carrying out a management cycle based on six elements of production: 〈 Q 〉 for quality, 〈 C 〉 for cost, 〈 D 〉 for delivery date, 〈 S 〉 for safety, 〈 T 〉 for training, and 〈 N 〉 for new products. These six elements of production make up the nuts and bolts of manufacturing.
Maintenance of quality
-
-
Acquisition of ISO9001 certification
Since acquiring ISO9001 certification, the international standard for quality management systems, in September 2003, we have maintained and managed quality focused on seven quality management principles: Customer Focus, Leadership, Engagement of People, Process Approach, Improvement, Evidence-based Decision-making, and Relationship Management.
-
Promotion to have JUKI employees take and pass a national technical skills test
Based on the notion that “manufacturing is a form of human development,” we actively encourage our employees to take and pass a national technical skills test. Seventy-eight percent or more of the employees in our manufacturing department hold national qualifications.
-
Repeated practice of screw-tightening and the in-house screening system to confirm screw-tightening performance
Employees in our assembly department take part in a screw-tightening exercise every morning. They work at a stable level by training every day and repeatedly committing the motions of screw-tightening to muscle memory. Once every six months we perform an “in-house screening of screw-tightening performance.” The top performers in the screening earn an in-house certification for outstanding manufacturing skill.
* Screening of screw-tightening performance
The persons screened are asked to tighten 100 screws from five directions (from straight above, from an angle, from straight below, etc.) at specified levels of strength using four screwdrivers with different thicknesses and lengths. Any person who scores 95 or more out of 100 points (one point per time) five times in a row is granted an in-house certification for outstanding manufacturing skill. -
Factory credited for the winning of the Deming Prize
The headquarters of the Industrial Sewing Machines Business was awarded the Deming Prize (Deming Application Prize for Division) in October 1981. The Ohtawara plant was judged to be instrumental in the prize-winning performance as the “production department” for the business. The Ohtawara plant has embodied a “Quality Management” and “Customer-Focused” mindset since its founding.
-
Approach to the environment
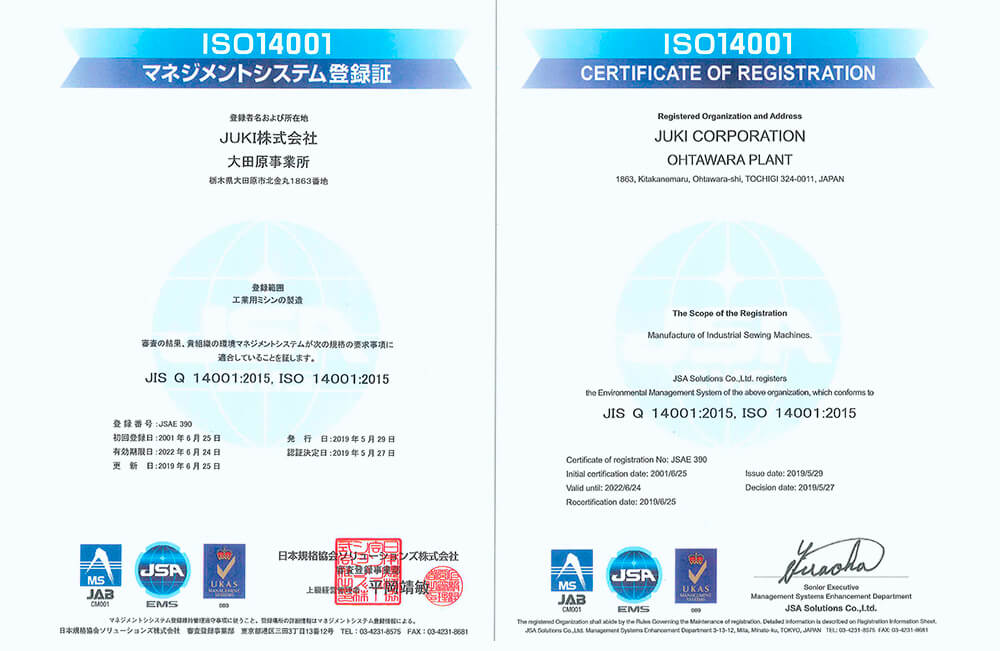
Environment policy of the JUKI Ohtawara plant
- We promote energy saving and the prevention of global warming. We strive to effectively use resources with the aim of becoming a zero-waste factory.
- We reduce the environmental load of our products by considering the full product lifecycle from parts supply, production, and shipment to final disposal.
- We promote steady environmental improvements as a factory situated in a leafy park full of trees planted with our own hands.
- We strive to prevent environmental pollution, to remain ever-aware of our environmental aspect (impacts), and to obey all laws, regulations, agreements, and other requirements relating to environment.
- We set environmental objectives and environmental goals to work to continuously improve our environmental performance and environmental management system.
- We conduct education and enlightenment activities for all of our employees to strive to raise the demand for environmental protection in-house.
Corporate history
Apr. 1971 |
The Ohtawara plant is completed in Otawara-shi, Tochigi.
![]() |
---|---|
Dec. 1973 |
The Nasu training center is completed.
![]() |
Jul. 1975 | The Ohtawara plant wins the Outstanding Performance prize as “a factory outside of an industrial complex” in the Tochigi-ken Fourth Factory Environmental Greening Competition. |
Aug. 1975 | The softball club of the Ohtawara plant is selected to represent Tochigi-ken in the national athletic meet one year after its establishment. |
Mar. 1977 | The new painting factory launches operations. |
Feb. 1985 | The full sewing machine production site moves from the Head Office factory to the Ohtawara plant. |
Aug. 1985 |
The world’s first electric painting robot is deployed in a painting line.
![]() |
Dec. 1992 | The JUKI Sports Center (gymnasium) is completed in the Ohtawara plant. |
Oct. 1993 | The third factory is completed. |
Jan. 1999 |
The Parts Center moves from the Head Office factory to the Ohtawara plant.
![]() |
Jun. 2001 | The Ohtawara plant acquires ISO14001 certification. |
Sep. 2003 | The Ohtawara plant acquires ISO9001 certification. |
Nov. 2009 | The second development department for industrial sewing machines moves to the Ohtawara plant. |
Apr. 2004 | The Minister of Health, Labour and Welfare awards the Ohtawara plant an Excellent Performance prize in recognition of its accident-free record. |
Oct. 2004 |
Digital cell production starts.
![]() |
Jul. 2011 |
The repairs to the office damaged in the Great East Japan Earthquake are completed.
![]() |
Jan. 2016 | The Ohtawara plant starts to participate in the group business (as a contracted development and manufacturing business). |
Apr. 2018 |
The Ohtawara plant sets up the JUKI History Museum.
![]() |
Information on the JUKI Ohtawara plant
Address | 1863, Kitakanemaru, Ohtawara-shi, Tochigi, 324-0011 |
---|---|
tel. | +81-287-23-5111 |
Site area | 185,188㎡ |
No. of employees | 306 (December 31,2021) |
Access
BY RAIL
Get off at either Nasu-Shiobara Station on the Tohoku Shinkansen or Nasu-Shiobara Station on the JR Tohoku Line.
By taxi
It will takes about 15 minutes from Nasu-Shiobara Station by taxi.
By bus
Get on the bus at the bus stop of Nasu-Shiobara Station on the Nasu-Shiobara Station Line and get off at JUKI Ohtawara Koujyoumae. It takes about 40 minutes by bus and another about three minutes by foot.
*Timetable (check the timetable on the Ohtawara City Hall website:)
BY CAR
Expressway outward bound from Tokyo
It takes about 35 minutes from the Yaita Interchange Exit on the Tohoku Expressway or about 25 minutes from the Nishi-Nasuno-Shiobara Interchange Exit on the Tohoku Expressway.
Expressway outward bound from Fukushima
It takes about 25 minutes from the Kuroiso-Itamuro Interchange Exit on the Tohoku Expressway or about 25 minutes from the Nishi-Nasuno-Shiobara Interchange Exit on the Tohoku Expressway.