工場全体の効率化ソリューション
設備毎、システム毎に保有する分断されたBig dataを連携することにより、[生産性の改善]、[作業効率の向上] 、[品質の維持・向上]、[製造品質の保証]を実現するソリューションです。
①生産進捗モニタ導入事例
事例概要
実装ライン管理者が事務所で[計画対比での進捗状況]、[機種切替タイミング]を把握し、適切な次アクションの指示を行う事が可能となります。
また、ライン作業者も現状を共有し、指示内容を理解し効率の良い行動が出来ます。
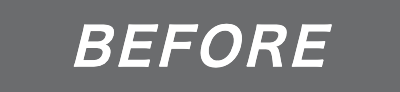
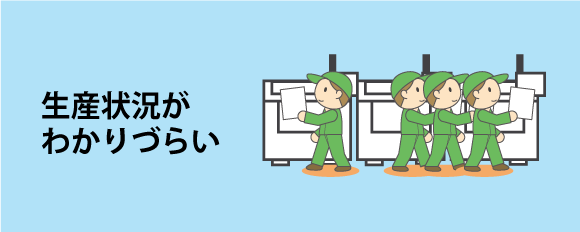
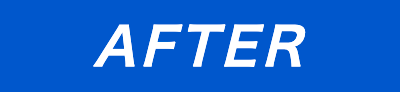
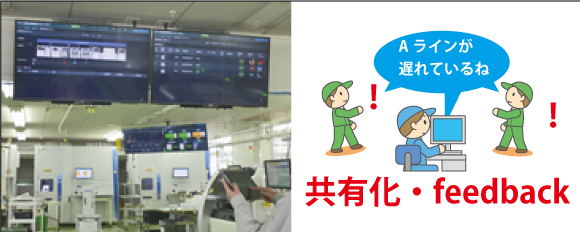
事例による効果
- 段取りタイミングの明確化により作業者集中による生産遅延の挽回
- ライン稼働状況の情報共有
②設備稼働モニタ導入 稼働率30%改善
事例概要
設備の稼働状況を色分け表示することにより、対応が必要な設備を見逃すことなく迅速に対応が出来ます。
また、設備のタクトタイム表示により正しい対応順序を決定できます。
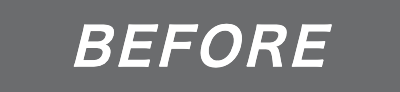
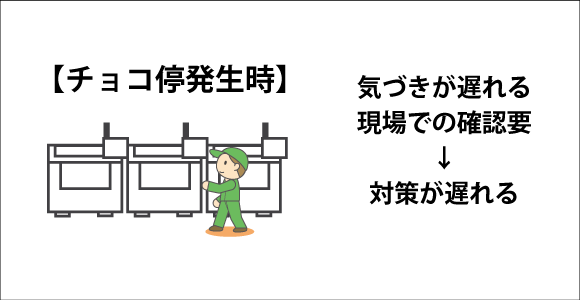
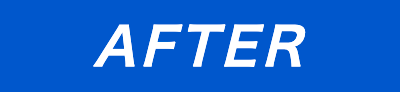
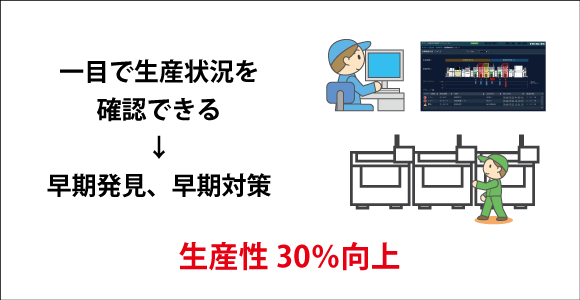
事例による効果
- ライン稼働率の向上
③JaNetsと 自動倉庫連携
事例概要
システムソフトJaNets (マウンタ)と、自動倉庫ISMシリーズの連携によりオペレータ作業を削減します。
- 生産プログラムからの部品自動出庫指示
- 部品切れ警告での部品自動出庫指示
- 部品残数の自動更新
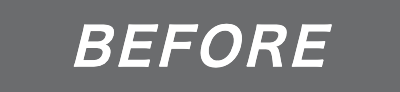
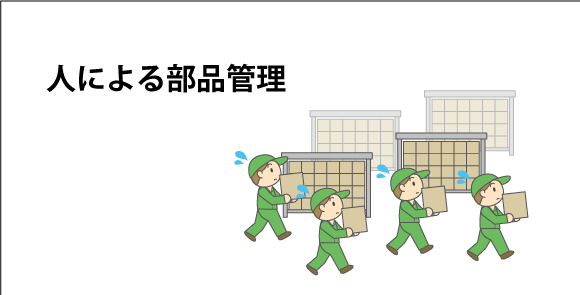
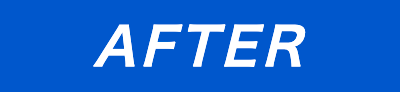
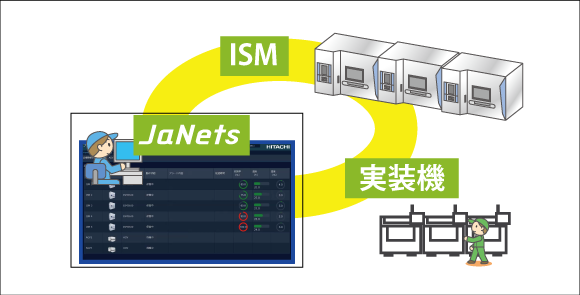
JaNetsとISMサーバー連携により、マウンタでの部品使用数が自動で減算・管理される
事例による効果
- プログラムからの自動部品出庫指示
- 在庫確認工数削減
- 棚卸工数の削減
④JaNetsとMES連携 既存システム活用で費用90%削減
事例概要
既運用中の誤装着防止を活用しながら、JaNetと顧客MESシステム連携でMESからのOK情報が来るまではマウンタにインターロックをかけ、誤造を防止します。
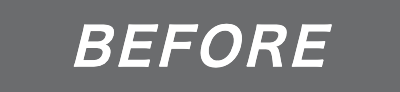
作業者の意識次第で生産スタート可能
インターロックが機能せず誤った部品を搭載する可能性あり
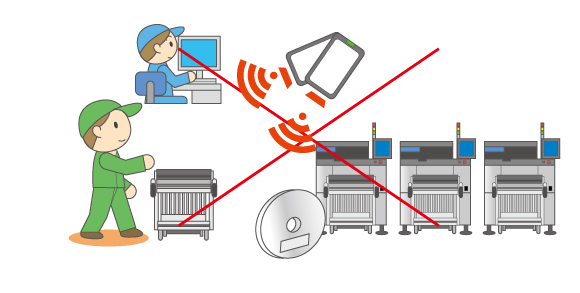
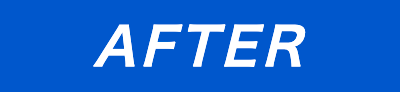
MESから照合OKの情報が来るまでは生産開始不可
事例による効果
- 新システムの導入コストを削減
- インターロックにより製造品質の維持
⑤JaNetsによる設備間連携
事例概要
印刷機・検査機・マウンタ連携により、製造品質の維持・向上を行います。
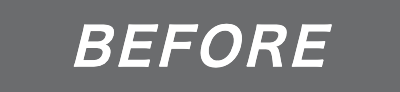
印刷ズレによる小型チップ部品のはんだ付け不良
各設備毎にバッドマークを読み取り
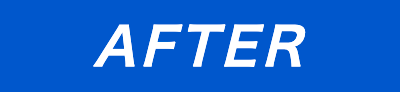
検査機で測定したはんだの位置ズレ量を基に、小型チップをはんだ位置に合わせて搭載 → セルフアライメントにより良品
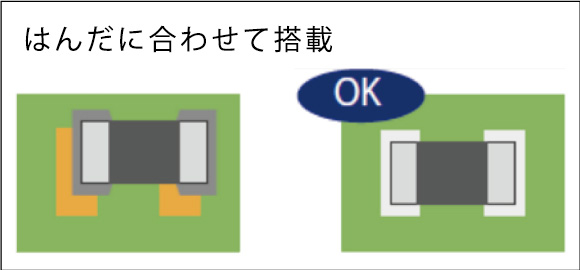
先頭設備のバットマーク情報を下流設備で共有しラインタクトを短縮
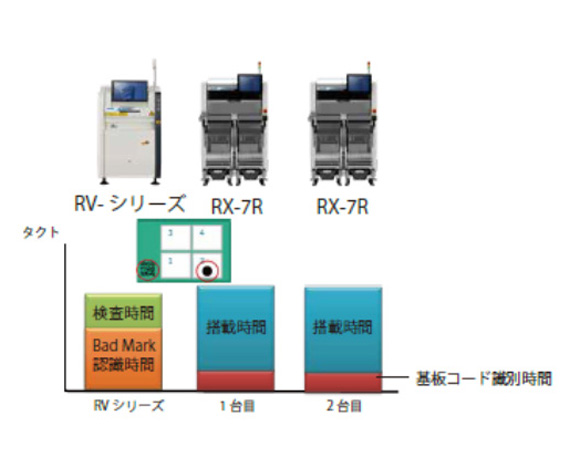
事例による効果
- 品質の維持・向上
- ラインタクト短縮により生産性向上
⑥RS-1R導入
事例概要
高速スマートモジュラマウンタRS-1Rは[部品高さ]を自動で可変する為、搭載部品構成にかかわらず最適なラインバランスを取ることが可能です。
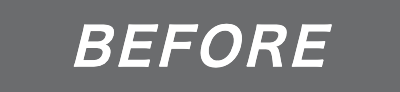
高速スマートモジュラマウンタRS-1Rは[部品高さ]を自動で可変する為、搭載部品構成にかかわらず最適なラインバランスを取ることが可能です。

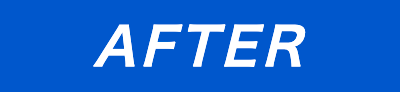
搭載部品高さにより、ヘッド高さを自動制御する為、最適タクトで生産可能。
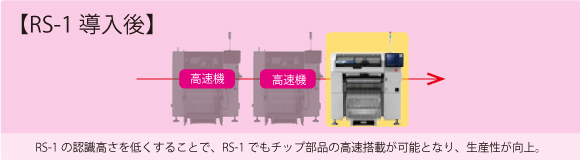
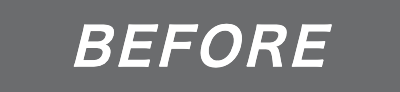
汎用機でのみ搭載可能な部品が多い機種では、ラインバランスが取れず、生産性が下がる。
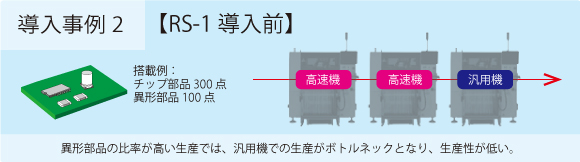
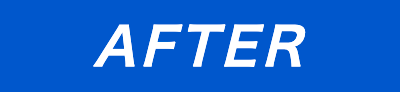
中間にRS-1Rを配置することで、容易にラインバランスを取ることができます。
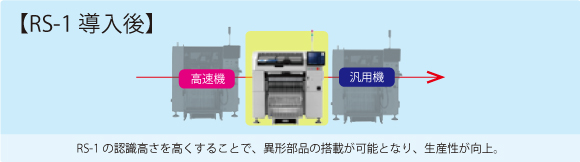
事例による効果
- ラインバランス向上による稼働率向上
- 最適タクトでの生産による生産性向上
⑦RS-1R導入
事例概要
類似の複数機種を一括段取りすることにより、 内段取り時間を削減し、稼働率を向上することが可能です。
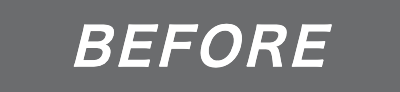
機種切替の停止時間が長く、稼働率が悪い。
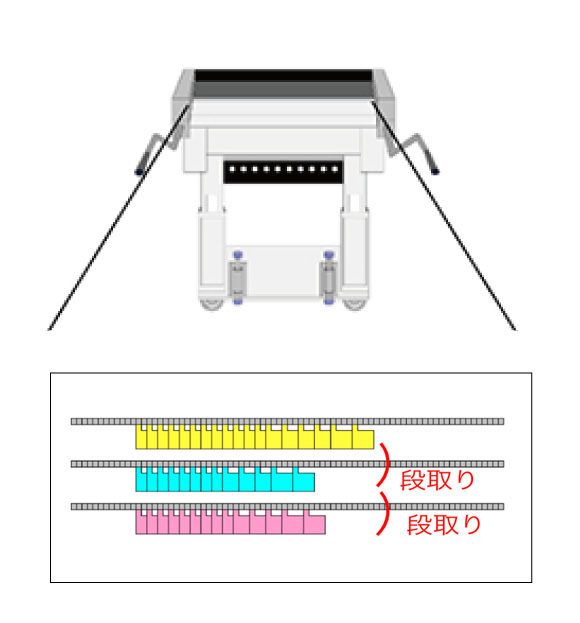
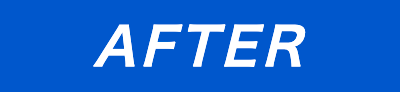
複数機種を一括段取りすることにより、生産機種切替の停止時間を削減。
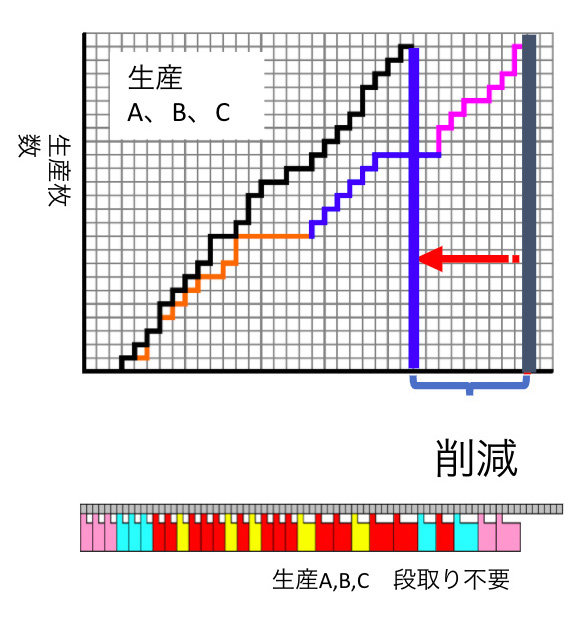
生産量を考慮した最適化を実施。
事例による効果
- 停止時間を最小限にし、ライン稼働率を向上
⑧RX-7R導入
事例概要
高速コンパクトモジュラマウンタRX-7Rと高速スマートモジュラマウンタRS-1Rの連結により面積生産性の向上
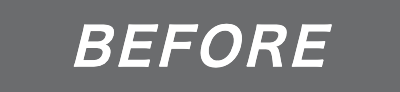
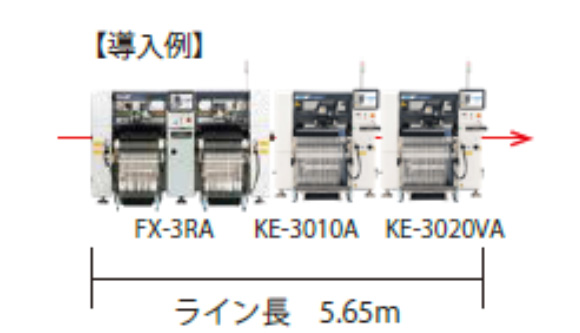
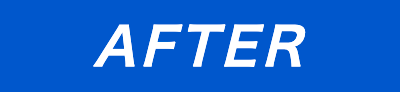
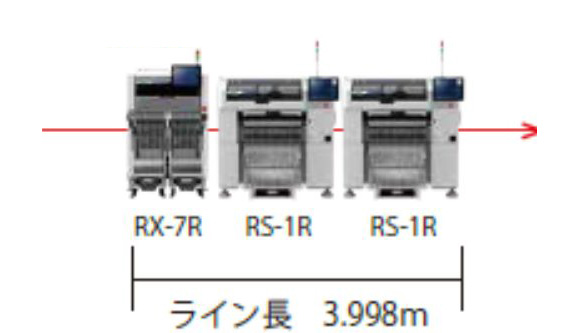
事例による効果
- 面積生産性の向上