部品挿入自動化のヒント
~ねじ締めと部品挿入を一台完結するJM-E01のご紹介~
目次
ねじ締め工程の自動化とは
ねじ締め工程は、さまざまな製品や機械の組み立てにおいて、モノを固定する重要なプロセスです。この工程は、家具や自動車、建築物の一部など、あらゆる分野で広く行われています。その中でも、特に精密さが求められる分野のひとつが「電子基板のねじ締め」です。電子基板は、スマートフォンやパソコン、家電製品など、私たちの日常生活に欠かせないデバイスの中核を成す部品であり、その性能や耐久性を最大限に引き出すためには、正確で効率的なねじ締めが必要不可欠です。
今回の記事では電子基板のねじ締めに特化し、その重要性やプロセス、さらに求められる技術や注意点について詳しく解説していきたいと思います。このテーマを取り上げることで、製造現場での作業の裏側や技術の工夫を知るきっかけになれば幸いです。
現状のねじ締め工程において完全自動化が難しい理由
現在、ロボット技術が進化を遂げる中でも、「ねじ締め作業工程」の完全な自動化は依然として難しいとされています。
従来のねじ締め工程において、電動ドライバによるねじ締め作業自体は「自動」で行われているものの、その電動ドライバを取る動作や、ねじを取る動作は「人手」に頼っています。また、ねじを締める「だけ」部品を固定する「だけ」といった単純な動作を行う「半自動ロボット」は存在しますが、これも完全な自動化とは言えません。
では、なぜこの工程を完全に自動化することが難しいのか、具体的に見ていきましょう。
1.部品の形状やサイズの多種多様であること
最初に挙げられる理由として、ねじを締められる部品の形状が複雑であることが挙げられます。
特に微小ねじや細かい部品では、高精度な位置決めが必要ですが、各製品で異なるサイズや種類のねじを使用する場合、自動化装置を柔軟に対応させるのは非常に困難です。さらにねじの種類やサイズのバリエーションが多数あり、
人の目で判断する方が容易であることが、自動化を進める上での大きなハードルとなっています。
2.ねじの供給と整列
2つ目に挙げられる理由として、ねじの供給と整列が難しいという点があげられます。
ねじ締め工程では、正確な方向で安定して供給する必要がありますが、自動だと不揃いなねじの供給ミスや整列不良が発生しやすいのです。
特に小さなねじや特殊形状のねじでは供給システムの調整が難しく、安定的に供給し続けることが困難です。
3.ねじ締め工程が煩雑であること
たくさんの種類のねじ締め作業を1工程で行うとき、締める箇所に合わせたねじを認識すること、それぞれのねじの保管場所を把握することが必要です。そのため、作業員のスキル差や体調などにより作業の質、量に大きく影響されます。また狭い場所での作業が必要な場合、ねじを締める側を定位置で固定することが難しいことも、工程を煩雑化させる理由として挙げられます。
4.締め付けトルクの制御
各ねじの締め付けトルクが製品性能に影響する場合、微細なトルク調整が必要になります。
ねじの素材や設置面の状態により摩擦が変動し、トルクの一貫性が損なわれることがあるため、トルクの均一性の確保が難しいという課題があげられます。
5.リアルタイムのフィードバック
トルクや角度にずれが生じた場合、すぐさま次の生産に対応しないと不良品を作り続けてしまいます。リアルタイムでフィードバックを監視し、調整するシステムを導入する必要がありますが、ねじ締め工程だけのシステム導入は難しい場合が多いです。
6.工程の複雑さ
ねじの位置や方向がバラついている場合、カメラやセンサを用いた補正が必要ですが、これは装置のコストや設計を複雑化させてしまいます。また、一部の部品では、仮締め後に本締めを行う必要があり、これを自動化するのは工程が複雑になる原因でもあります。
7.人間の柔軟性との比較
作業者は、微妙な位置調整や部品のばらつきに柔軟に対応できますが、ロボットや自動化装置では同じレベルの対応が難しいです。不規則な部品配置や異常発生時の対応は、作業者の判断力に依存している部分が多く、なかなか人手の作業から自動化に移行できない原因となっています。
外部環境の変化と自動化の必要性
外部環境の変化
これまで、ねじ締め工程において人が基板や部品に直接触れることが当たり前とされてきました。しかし、近年では「人が基板に触れることは望ましくない」との認識が広まりつつあります。その理由の1つが、不良の発生リスクです。人が基板に触れることで、微細な汚れや油分が基板に付着する可能性があり、それが原因で電気的な不良や動作不具合を引き起こすことがあります。また、繊細な部品に対する直接的な力の加わり方が不適切である場合、部品の破損やねじ締め不良が発生する可能性もあります。このような状況では、製品の品質が低下し、生産効率も悪化するため、人手による作業には限界があるとされています。
さらに、現代の生産現場では、生産性の向上やコスト削減が強く求められています。その一環として、作業の自動化が推進されており、ねじ締め工程もその対象の一つとなっています。特に精密機器や基板を扱う工程では、人手を排除して完全自動化を実現することで、品質の安定化と不良率の削減が期待されています。これらの理由から、ねじ締め工程の自動化は避けられない課題となっています。
ねじ締め工程の技術的課題
ねじ締め工程におけるもう1つの重要なポイントは、ねじを「締める側」と「締められる側」の「2工程を同時に自動化」するという点です。
ねじを締める側(工具やロボットアームの制御)と、締められる側(部品や基板)の位置や固定状態を安定させる必要があります。この2つの要素を同時に精密に管理するのは技術的に非常に難しく、これが自動化が進まなかった大きな理由の1つです。
2台同時制御の課題
2台のロボットを同期させて制御することが難しい理由として、上部のロボットがねじを締める際の力や角度に合わせて、下部のロボットが基板を正確に支えなければならないことです。締め付けトルクや部品の固定位置にわずかなズレがあるだけでも、作業全体の精度が損なわれてしまいうため、ねじ締め作業の自動化が進みませんでした。
ひっくり返す工程による不良の発生
従来の自動化ロボットは、1方向からのアプローチしかできず、対象物を動かして作業を行うのが一般的でした。ねじ締め工程においても、上方向からしかねじを締められないという課題がありました。そのため、裏面にねじ締めを行う場合には、基板をひっくり返す必要がありました。
しかし、基板をひっくり返す工程そのものが不良の原因になることも大きな問題でした。この工程では、基板の位置がわずかにずれたり、基板に固定された部品が正確に保持されていなかったりすることで、作業が進むにつれてさらなる不良が蓄積されていきます。特に、精密部品を扱う基板製造においては、これが製品の信頼性に重大な影響を与える可能性があります。また、ひっくり返す動作自体が機械的に繰り返されることで、装置の摩耗や劣化を早める原因にもなります。こうした問題を解決しない限り、自動化によるメリットを最大限に引き出すことは難しいのです。ひっくり返す工程を自動化するために、「反転機」を使うこともありますが、さらに工程が増え、コストが増える一因となっていました。
JM-E01のポイント
そこでJUKIは、設備の中に2台のロボットを配置し、上下両方の作業を同時に行えるような統合型のシステムを導入した「2工程1台完結」のロボットJM-E01を開発しました。
1.2工程1台完結
上部ロボットで部品挿入工程、下部ロボットでねじ締め工程を行うという2工程1台完結のロボットです。従来は多額の費用をかけたカスタマイズ品で対応は可能でしたが、カスタマイズ品ではない汎用品でロボットが2台融合しているものはありませんでした。(当社調べ)
2.高精度
マウンタで培われた技術を活用し高精度に挿入、ねじ締めを実現します。XYZθ軸を上下で制御し、合計8軸をコントロールすることで高精度かつ高速な作業を実現します。さらに新しく開発したねじ締めの技術を加えることで、2工程を1台で完結するマシンが誕生しました。
3.組立工程への展開
ねじ締めの上下同時作業の技術をさらに発展させ、将来的にははんだ付け・基板分割など組立工程への展開も想定しています。
JM-E01が実現できるソリューション
1. 全自動ラインの構築
車両や医療機器の製造においては、不良品の発生が命に関わる重大なリスクとなるため、極めて高い品質が求められます。このような分野では、手作業によるミスや工程間の不安定さを最小限に抑えるため、自動化が不可欠です。最新の技術を用いた画期的なマシンの導入により、部品挿入やねじ締めを含む工程を全自動化し、高精度かつ効率的なライン構築が可能になりました。
2.高品質の確保
これまで悩ませてきた作業者の熟練度に依存し、不適切なトルク管理や締め忘れが発生するヒューマンエラーの課題や、熟練した作業者が退職するとノウハウが失われるリスクがある技術継承問題など、自動化をすることで高品質なモノづくりができます。
特に不良が製品の安全性に直結する車両や医療分野では、全自動化が品質安定に大きく寄与します。自動化することで、人による作業のバラツキを排除し、常に一定の精度を維持することで、トラブルを未然に防ぐことができます。
3.工場全体で結果的に実現する高いROI
初期投資が高額になる自動化設備ですが、初期投資、ランニングコスト、機会損失問題などトータルでの費用対効果を考えると高いROIを実現することが可能になります。不良率の低減とリワークコストの削減をすることで、一定のサイクルタイムを維持し、計画生産が可能になります。顧客からの信頼性が向上することで結果的な利益やトータルの生産効率が向上し、長期的には投資回収が可能となります。
導入事例
実際にご導入いただいたお客様事例として車載のコントロール基板メーカー様をご紹介します。
【導入前】
1.ライン
従来は下記のラインでした。
印刷(自動)、SMT(自動)、リフロー(自動)、コネクタ挿入(人)反転作業あり、ねじ締め(人)、フロー(自動)
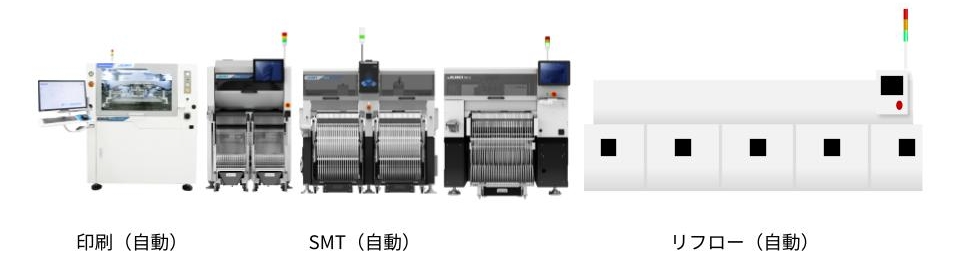
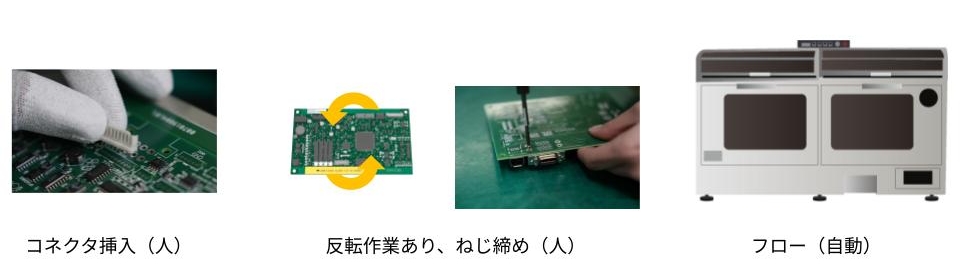
2.課題
1. ヒューマンエラーの発生
コネクタでの挿し間違えやねじが刺さっていない状況が多発していました。特に人手不足で入社間もない作業員が行ったオペレーションではミスが頻繁に発生していました。検証の結果、不良の9割が人の工程で発生していました。
2. クライアントからの厳しい品質管理
自動でできないなら、次の発注は頼めないといわれていたため、どうしても自動化する必要がありました。
【導入後】
1.ライン
工程自体を見直し下記のラインを新たに構築しました。
印刷、SMT(自動)、コネクタ挿入(自動)、ねじ締め(自動)反転作業なし、リフロー(自動)
2.効果
品質が安定し、顧客からの信頼を獲得することができました。また、その噂を聞きつけた他のクライアントからの仕事も受注できました。
完全自動化ラインになったことで、フロー工程が不要となり、電力消費を削減できました。さらに、はんだを使用しなくなったことで、環境によいという評価を得ることができました。
本お客様のラインではJM-E01は絶賛稼働中です。
まとめ
導入事例に上げさせていただいたお客様以外でも、家電製造メーカーのお客様をはじめ、幅広いお客様にも導入され、随時その業種範囲は急速に広がっています。導入いただいたお客様からは、工程、人手が削減され、コスト削減や品質向上など効果が絶大だという高評価を頂戴しています。また、汎用性があるため、多岐にわたり活用されています。SMTのラインにはいることで、全自動のラインが構築され、人手不足だけではなくたくさんのメリットがあります。
ぜひお気軽にお問い合わせください。