シャツ生産の中でも技能度が求められる衿・剣ボロ工程での生産性と品質を上げたい・・・。
事例紹介:シャツ工場
- ホーム
- ソリューション一覧
- JUKI Smart Solutions
- 事例紹介:シャツ工場
国 | インド |
---|---|
生産アイテム | 紳士ドレスシャツ |
生産量 | 14,400枚/日 |
提案した ソリューション |
![]() 自動化 ![]() デジタル化 ![]() ネットワーク化 |
得られた効果 |
![]() 生産性向上 ![]() 省人化 ![]() 脱技能 ![]() 品質向上 |
概要
現工場と同規模の工場を1棟新設するに当たり初期設備投資額は増えるものの、自動化率の高いスマートファクトリー提案により短い期間で投資回収が可能になりました。
対象
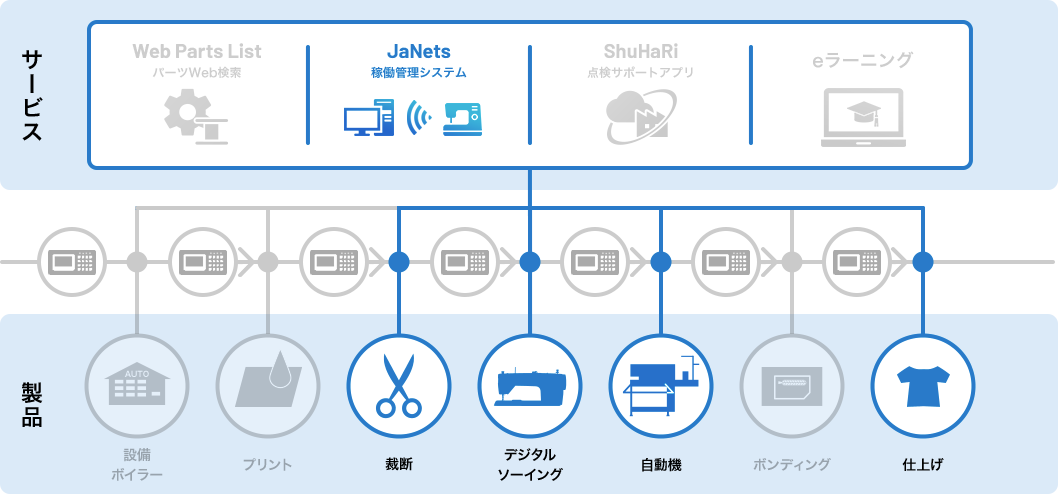
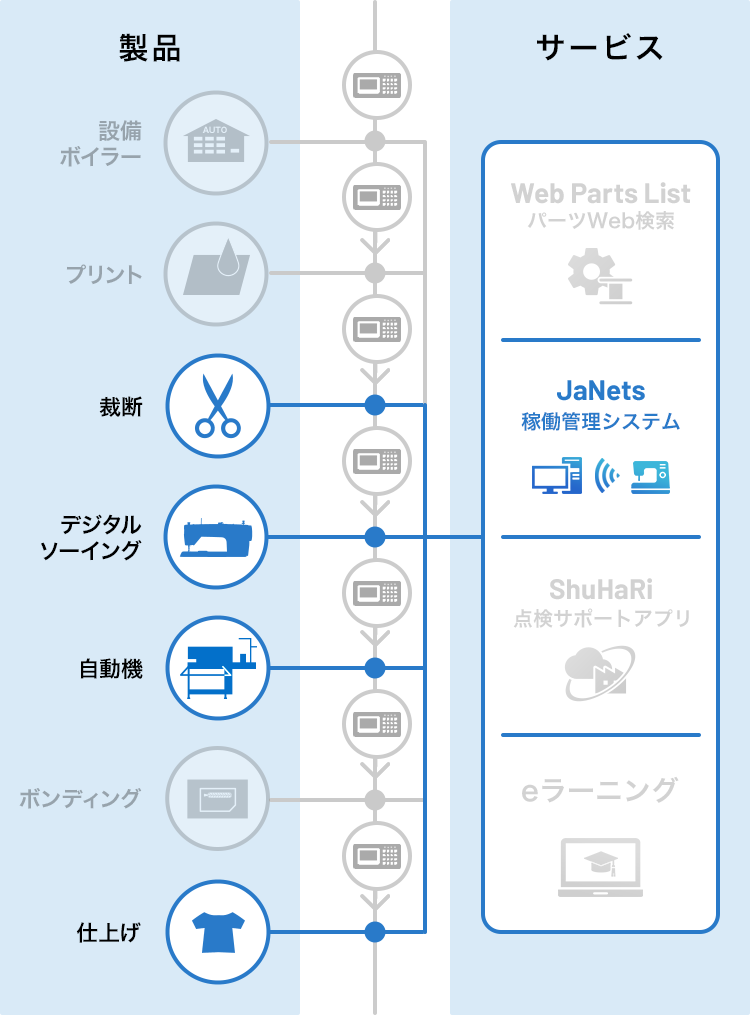
ソリューション
Point 1
裁断・縫製・仕上げ工程を自動化!
裁断工程にはCAMや自動延反機、仕上げ工程には自動畳み機などのアライアンス機器、縫製工程にも多くの自動機導入を提案しました。
人員も時間も要す難しい工程を自動化することで省人化を実現でき、かつ安定した品質で生産性を向上させることが期待できます。
(1)裁断工程
Before
手作業による延反
自動化

After
自動延反機による延反
Before
竪刃裁断機による手裁断
自動化

After
CAMによる自動裁断
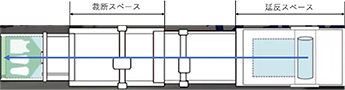
*延反から裁断までの一連の作業を自動で行うスマートソリューションをご提案。オペレーターは初めの生地のセットと、終わりのピックアップ作業のみ行います。
(2)仕上げ工程
Before
自動化

After
ハンガーを利用した
仕上げシステムラインの提案
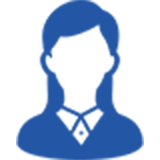
お客様の困りごと
(3)縫製工程
Before
①衿工程
1本針本縫いミシンによる作業
自動化

After
PS-800(パターンシーマー)に
置き換え
型に付けたRFIDをミシンが読取り、セット
するだけで1台で様々な工程のパターンを
縫製できるように
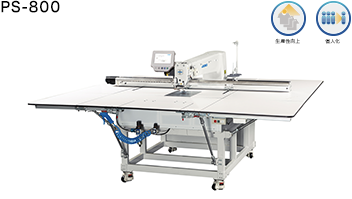
Before
②剣ボロ工程
剣ボロ縫製には2工程が必要
(剣ボロ折りアイロン
・剣ボロ付け縫い+ステッチ)
自動化

After
剣ボロ自動機導入で2工程が
1つの自動機で行えるようになり
生産性がUP!
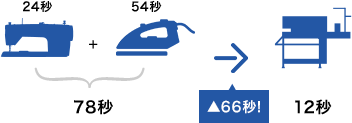
Point 2
縫製工程にはデジタルミシンを、工場全体はJaNetsで見える化!
デジタルミシン導入により、サンプルデータを実際のラインに反映できることで理想の縫製への実現性が高まり、さらに稼働管理システム”JaNets”を導入することでリアルタイムでの工場状況把握・管理が可能になります。
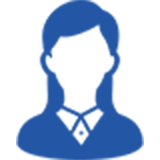
お客様の困りごと
品番切り替えが多く、1日に2~3回替わることも。その度にミシンの設定や調整が必要・・・。
(1)デジタルミシンの導入
Before
①本縫いミシン
従来の本縫いミシンでは品番が切り替わるたびに
生地特性に合わせて縫い調子を変更する必要があった
Before
②ボタン穴かがりミシン
従来のボタン穴かがりミシンでは品番が切り替わるたびに
穴かがりの形状や大きさによって調整の必要があった
デジタル化

After
サンプル縫いで使用したパターンのデータを
コピー&ペーストすることで調整することなく縫製が可能に
切り替えに伴う調整時間が大幅短縮
***あいろ工程への応援の際にも、
応援用のミシンにデータをコピー&ペーストするだけなので
調整が不要です
(2)JaNets
Before
現場の状況が翌日のレポートでしか把握できなかった
ネットワーク化

After
事務所にいてもリアルタイムで現場の状況が見えるように
効果
従来
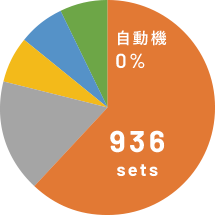
改善

標準
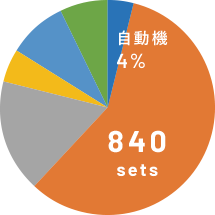
イノベーション

スマートファクトリー
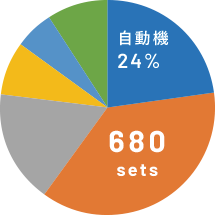
従来からまず標準的な改善を行い、
更に自動機やデジタルミシンの割合を増やすイノベーションを実施。
自動機導入により全体の機械台数を大幅に削減できました。
-
オペレーター人数
1,227人▶︎586人
-
生産性
11,680枚/日▶︎14,400枚/日
-
スペース
400.1m² ▶︎386.0m²
-
投資回収期間
1.90年