Case Studies
Improvement of delivery efficiency (picking)
Before
Customer concerns
- It takes time to collect from the shelf.
- It takes time to pick.
- The picking time varies depending on the level of the worker.
- A picking error occurs.
- We want to thoroughly carry out first-in and first-out of parts.
- Have workers do a variety of work.
- Real-time unloading is not possible according to the number of productions required at the site.
After
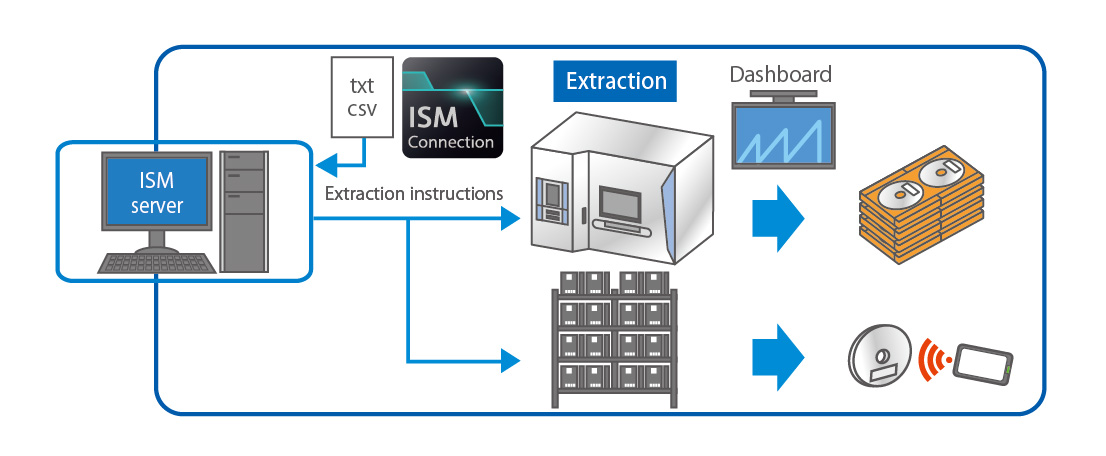
Customer feedback after introduction
- By the system cooperation with the X-ray counter, the inventory time was able to be reduced by about 90%.
- Since ISM automatically go in and out at one time, we were able to reduce the number of hours involved in going in and out.
- It was possible to reduce man-hours, because it was possible to use the used shelf together, and in addition, it became possible to control by free location.
- Since ISM manages the first-in and first-out of the part, the checking operation of the worker was able to be reduced.
- Since the working time was able to be reduced, the worker became able to carry out another work.
- A share of work was achieved.
- Even a new worker was able to easily take in and out.
- We were able to turn the veteran members to other tasks.
- Combined delivery of paired parts is possible.
- Real-time delivery at the site is possible.
Use in assembly parts management
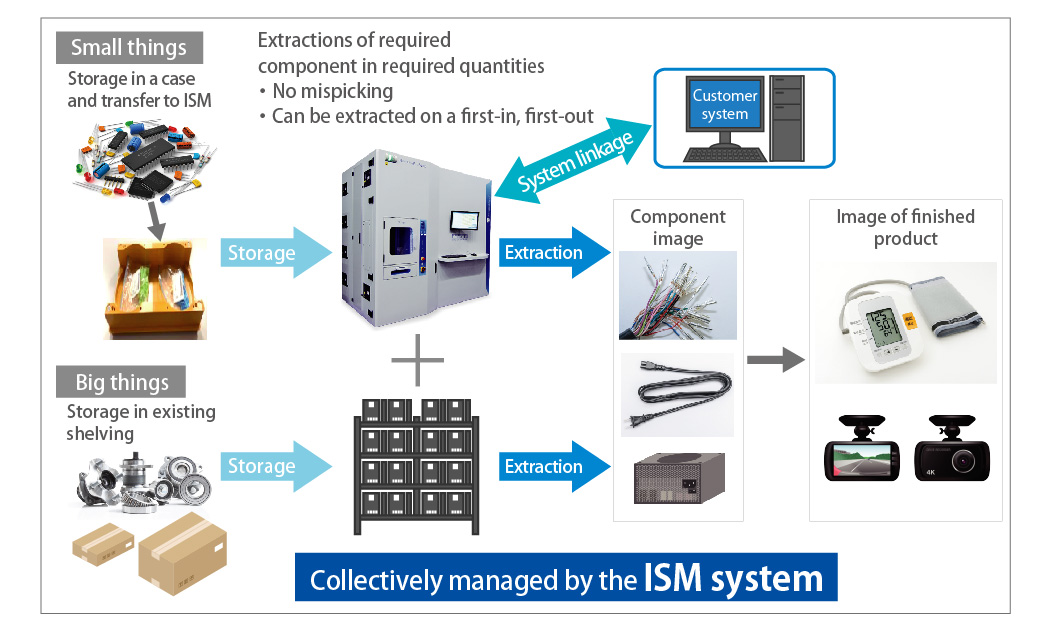
To the list of Parts management cases